在现代电子制造业中,印刷电路板(PCB)作为电子元器件的载体和连接桥梁,其质量和可靠性对整个电子产品的性能和寿命有着至关重要的影响。然而,在PCB板的制造过程中,回流焊作为一个关键的工艺环节,往往会导致PCB板出现弯曲和翘曲等问题,严重影响生产效率和产品质量。因此,如何避免PCB板在回流焊过程中发生弯曲和翘曲,成为了电子制造业亟待解决的问题。
一、回流焊导致PCB板弯曲和翘曲的原因
回流焊,作为电子元器件组装的关键步骤,是通过加热将预先放置在PCB板上的焊膏熔化,然后再冷却形成永久性的电气连接。在这一过程中,PCB板需要经历快速升温和降温的过程,这种温度梯度会在PCB板内部产生应力,进而导致板的弯曲和翘曲。具体来说,回流焊导致PCB板弯曲和翘曲的原因主要有以下几点:
材料热膨胀系数不匹配:PCB板由多种材料组成,如铜箔、树脂和玻璃纤维等。这些材料在受热时,由于热膨胀系数的不同,会产生不同程度的膨胀,从而在板内形成应力。当应力超过材料的承受极限时,就会导致板的弯曲和翘曲。
加热不均匀:在回流焊过程中,如果加热不均匀,就会导致PCB板各部分温度不一致,进而产生温度梯度。这种温度梯度会在板内形成热应力,导致板的弯曲和翘曲。
焊膏分布不均匀:焊膏在PCB板上的分布如果不均匀,会在回流焊过程中形成不同的熔化区域。这些区域在冷却时会收缩,但由于收缩程度不同,会在板内产生应力,导致板的弯曲和翘曲。
二、避免PCB板弯曲和翘曲的措施
针对上述原因,我们可以采取以下措施来避免PCB板在回流焊过程中发生弯曲和翘曲:
优化材料选择:选择热膨胀系数相匹配的材料是避免PCB板弯曲和翘曲的关键。在PCB板的设计阶段,应对所使用的材料进行严格的筛选和匹配,确保各材料在受热时能够保持相对稳定的尺寸变化。
改进加热方式:为实现均匀加热,可以采用热风循环或红外辐射等加热方式。这些方式能够确保PCB板各部分在回流焊过程中获得均匀的温度分布,从而减少温度梯度产生的热应力。
优化焊膏布局:在PCB板的布局设计阶段,应合理安排元器件的位置和焊盘的分布,确保焊膏在板上的分布尽可能均匀。这有助于减少回流焊过程中因焊膏分布不均而产生的应力。
引入预热和缓冷工艺:在回流焊前对PCB板进行预热处理,可以降低板内的温度梯度,从而减少应力产生。同样,在回流焊后对PCB板进行缓冷处理,有助于消除已产生的应力,避免板的弯曲和翘曲。
强化工艺控制:对回流焊工艺参数进行严格控制,如温度、时间和加热速率等,确保PCB板在回流焊过程中经历的温度历程符合设计要求。这有助于减少因工艺波动导致的弯曲和翘曲问题。
采用辅助支撑装置:在回流焊过程中,可以使用辅助支撑装置对PCB板进行支撑和固定。这有助于减少板在受热时的自由变形空间,从而降低弯曲和翘曲的风险。
三、实际应用中的注意事项
在实际应用上述措施时,还需注意以下几点:
综合考虑成本和效益:在采取避免PCB板弯曲和翘曲的措施时,应综合考虑成本和效益。例如,在选择材料和优化工艺时,应在确保产品质量的前提下,尽可能降低生产成本。
遵循行业标准和规范:在设计和制造PCB板时,应遵循相关的行业标准和规范。这些标准和规范通常包含了避免弯曲和翘曲的最佳实践和经验总结,对指导实际工作具有重要意义。
注重持续改进和创新:随着电子制造业的不断发展,新的材料、工艺和设备不断涌现。为持续提高产品质量和生产效率,应注重引进新技术和进行持续的技术创新。
四、结论
避免PCB板在回流焊过程中发生弯曲和翘曲是一个涉及材料、设计和工艺等多方面的复杂问题。通过优化材料选择、改进加热方式、优化焊膏布局、引入预热和缓冷工艺、强化工艺控制以及采用辅助支撑装置等措施,可以有效地降低PCB板弯曲和翘曲的风险。在实际应用这些措施时,还需综合考虑成本和效益、遵循行业标准和规范以及注重持续改进和创新等方面的问题。只有这样,才能确保PCB板在回流焊过程中的质量和可靠性,进而提升整个电子产品的性能和寿命。
-
pcb
+关注
关注
4220文章
22472浏览量
385778 -
半导体封装
+关注
关注
4文章
213浏览量
13537 -
回流焊
+关注
关注
14文章
416浏览量
16443
发布评论请先 登录
相关推荐
守护PCB板平整度!回流焊防弯曲翘曲全攻略
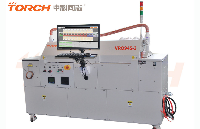
介绍三种SMT焊接工艺:回流焊、波峰焊、通孔回流焊
用AD8221生产电路,需要知道用多大温度的回流焊才合适?
真空回流焊是什么?浅谈SMT真空回流焊炉的基本原理
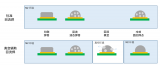
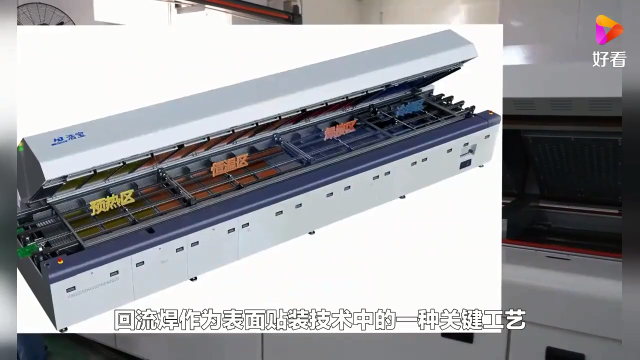
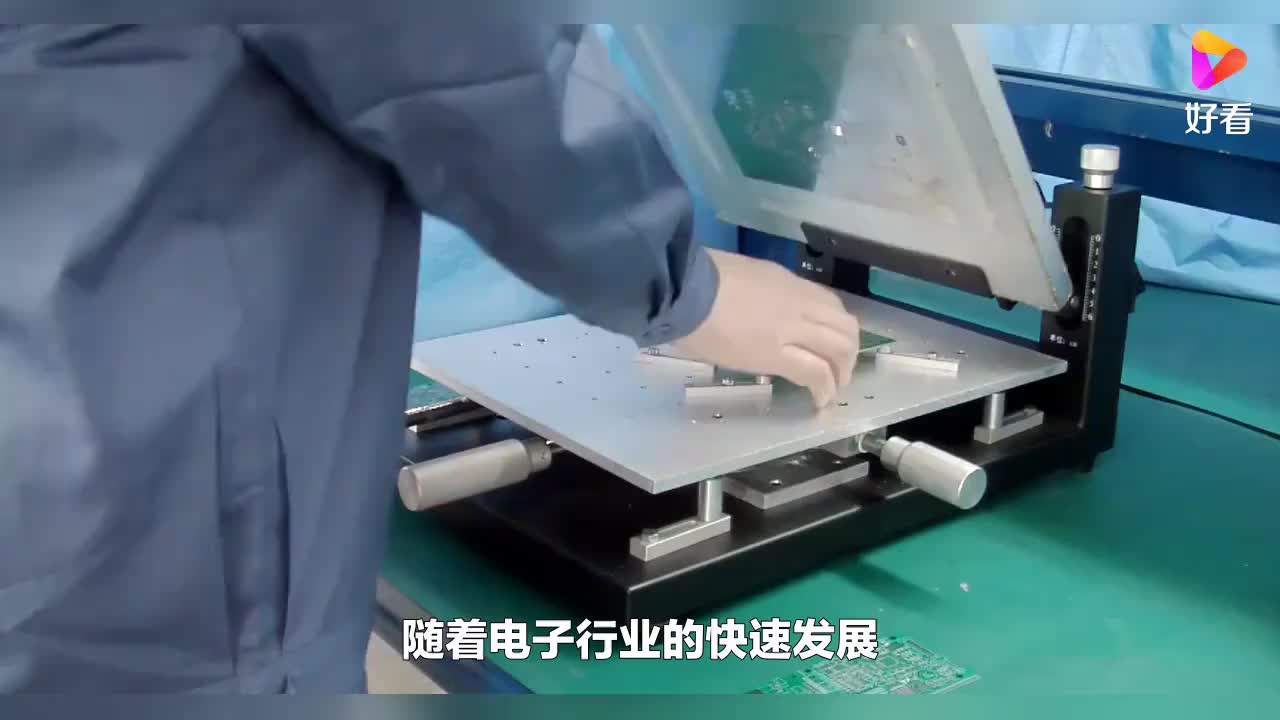
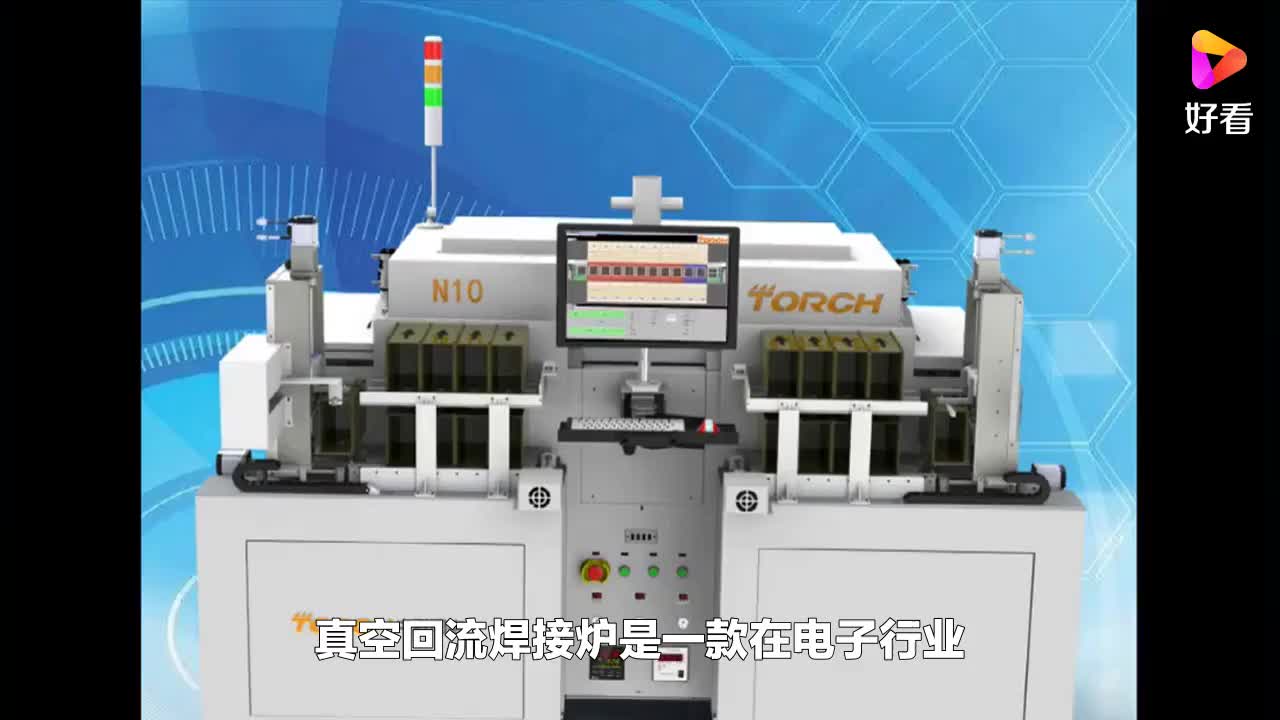
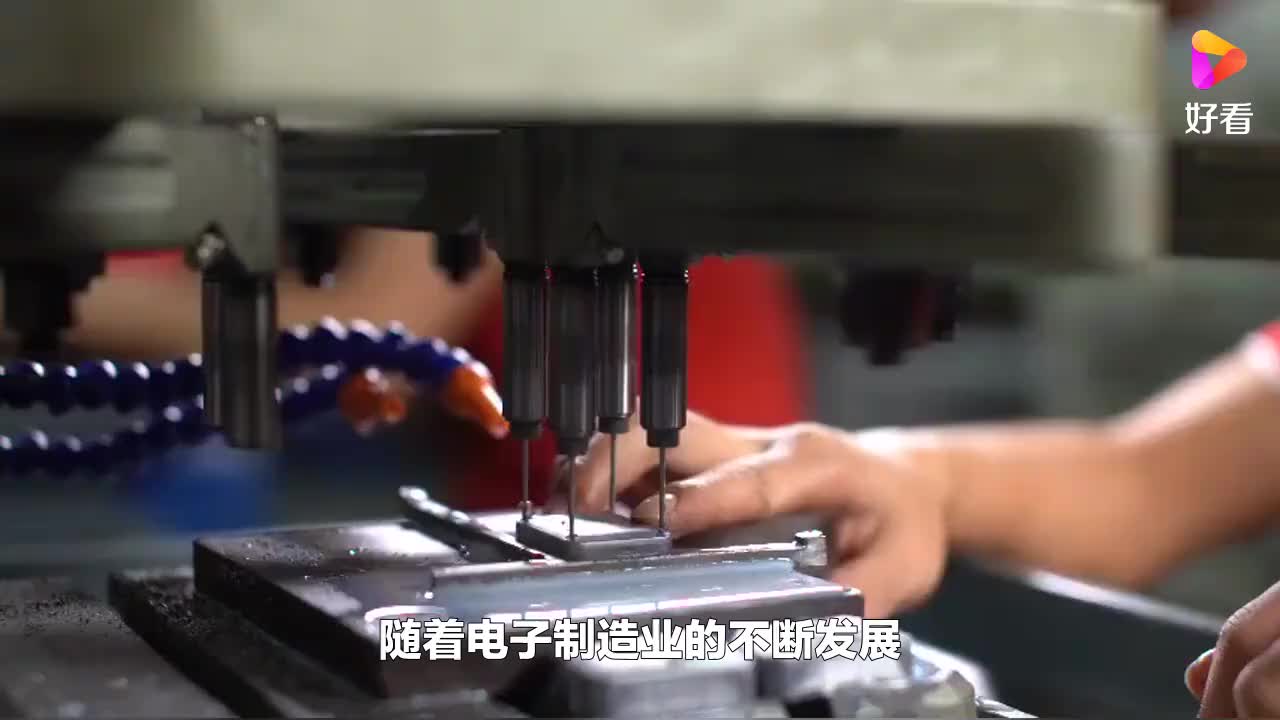
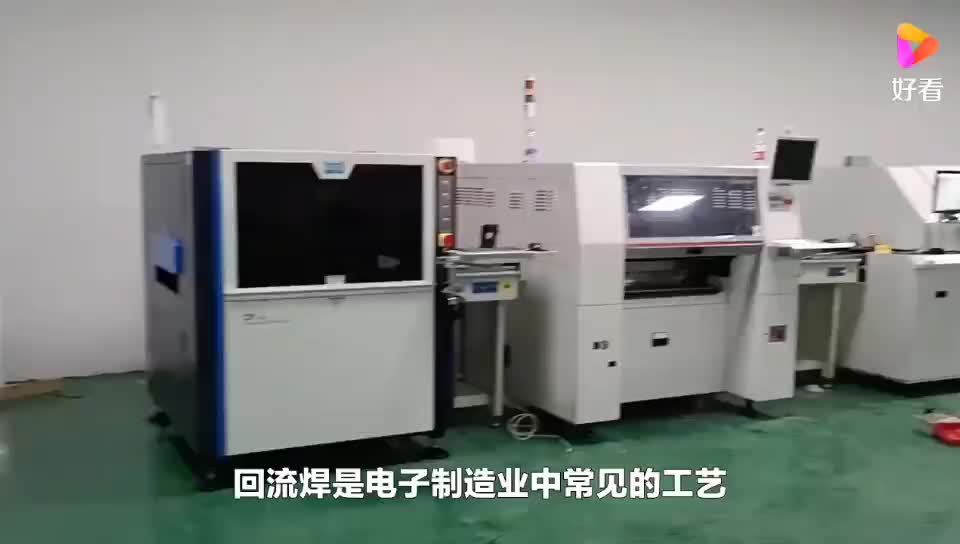
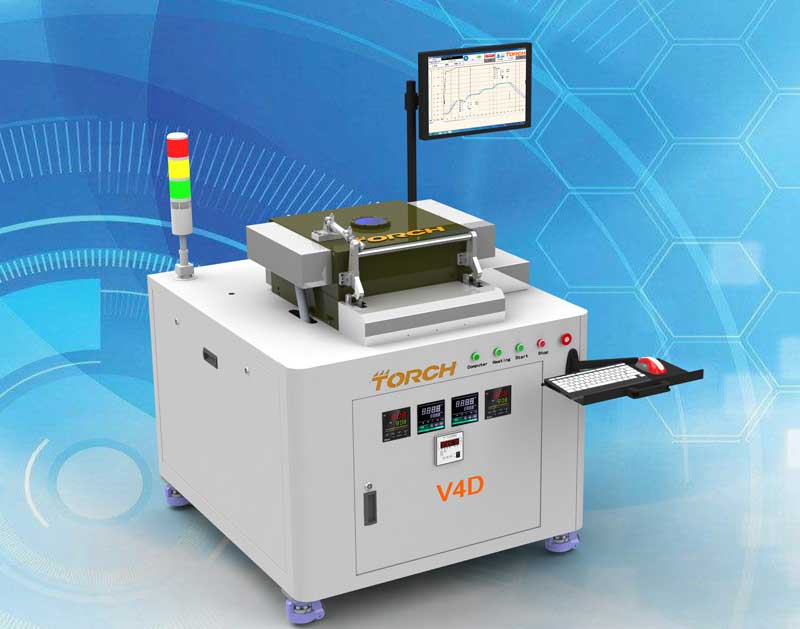
评论