摘要:随着第五代移动通信技术(5G 技术)的出现与快速发展,电子产品尤其是智能手机、平板电脑等产品,越发朝着高性能、高集成和微型化的方向发展。功耗成倍的增长将导致电子芯片在狭小空间内产生过高的热流密度和工作温度,进一步引发严峻的热失控难题。超薄均热板具有优异的导热性能,较大传热面积、较好的均温性能和高可靠性等优点,是解决电子设备散热问题的首要途径。为满足 5G 时代下现代微型化电子设备散热需求,均热板进一步超薄化是当前业界和学术界的研究热点。基于此,对超薄均热板传热原理进行概述,重点综述国内外超薄均热板结构设计研究现状,包括气液通道排布结构和吸液芯结构等,介绍目前超薄均热板封装制造工艺,并分析其实现极端超薄化中存在的问题,最后对其在高集成超轻薄电子设备等散热领域的研究趋势和发展前景进行了科学的展望。
0 前言
2019 年以来,随着第五代移动通信技术(5G 技术)的出现和快速发展,电子产品尤其是智能手机、平板电脑等产品,越发朝着高性能、高集成和微型化的方向发展。为满足产品的性能和尺寸需求,电子芯片上的晶体管密度越来越大。
2006 年制造的电子芯片每平方厘米具有晶体管的数量仅可以达到 1 亿个,到 2019 年,华为 5G 麒麟 990 芯片已经集成晶体管数量多达 103 亿,而该 5G 芯片面积仅为1.13 平方厘米,芯片晶体管的密度增加了接近 100倍。然而,成倍增长的功耗将导致电子芯片在狭小间内产生过高的热流密度(> 200 W/cm2)和工作温度(> 70℃),进一步引发严峻的散热问题,导致电子芯片无法正常工作,从而制约其进一步发展。
传统的电子设备散热方式,自然对流由于自身换热系数低,难以满足更高热流密度的散热要求,而强制风冷和水冷热管理方式需要外加动力装置,无法适应狭小空间内的封装集成。新型高导热材料石墨片具有较高的平面导热系数(1500 W/m·K),在满足电子设备散热方面具有一定的优势,然而其在厚度方向上导热系数极差,导热性能受到限制。因此,开发新型高效的热管理技术,实现电子产品的有效散热是当今行业迫切需要解决的问题。
相变传热元件利用工质的相变潜热来带走热量,是解决电子设备散热问题的最具有潜力热管理方式。为满足现代微型化电子设备散热需求,常规尺寸的相变传热元件难以应用到产品中,微型化相变传热元件,尤其是厚度超薄化的相变传热元件,是当前业界关注的焦点。
一般而言,超薄相变传热元件包括超薄热管和超薄均热板。超薄热管通常是先制造出管壁超薄的圆热管,再通过加热相变压扁的方式加工而成。目前,大批量生产的圆热管壁厚最薄可达 0.08 mm,压扁加工后超薄热管厚度最低为 0.4 mm,在智能手机三星 Galaxy S7 上得到应用。然而,当厚度进一步降低时,超薄热管传热性能大幅度恶化。更重要的是,采用圆热管压扁制备而成的超薄热管,在薄壁圆管直径限制下,宽度极为有限,0.4 mm 厚的超薄热管宽度最多不超过 3 mm,超薄热管的尺寸无法根据电子芯片尺寸(长宽通常为 10 mm)及实际散热需求进行变更,超薄热管散热能力也因此受到限制。
随着 5G 时代的到来,超薄热管逐渐无法满足便携式移动电子产品散热需求。超薄均热板,通常通过壳板焊接密封成形,外形尺寸可根据实际散热需求进行调整,同时具有优异的导热性能,较大传热面积和较好的均温性能等优点,非常适合于 5G 渗透下现代微型化电子设备等领域应用,吸引了广大研究人员的高度关注。超薄均热板结合石墨烯辅助散热是现阶段智能手机主流散热方案。因此,开发出传热性能优异超薄均热板对促进 5G 移动电子设备的发展显得至关重要。
本文针对超薄均热板在高集成超轻薄电子器件中的应用,从超薄均热板的传热原理理论,超薄均热板的结构设计(吸液芯结构与气液通道排布)以及其封装制造方法等方面展开叙述,总结了目前超薄均热板发展现状,同时对其未来的研究进行了科学的预测和展望。
1 超薄均热板简述
超薄均热板是一种具有超高热导率的传热元件,一般由壳体、支撑柱、真空腔体(蒸汽腔)、吸液芯和工质组成,通过内部工质气液相变巨大的相变潜热来实现高效换热。图 1 所示为两种典型的超薄均热板——沿厚度方向和沿长度方向传热的工作原理示意图。
图 1 两种典型超薄均热板的传热工作原理
超薄均热板完成内部气液循环相变传热的过程包括蒸发端浸润在吸液芯中的液体工质通过壳体传递吸收热源热量,在真空腔体内发生蒸发相变变成蒸汽工质,液-气相变迅速带走大量热量,蒸汽工质在真空腔内蒸汽压差推动下快速流动,迅速扩散至冷凝端;在冷凝端,蒸汽工质通过壳体传递被冷源带走热量,发生冷凝相变变成液体工质,气-液相变快速带走大量热量,液体工质在吸液芯毛细压力驱动下发生回流,流动至蒸发端继续吸收热量,完成整个气液循环。
这里两种典型超薄均热板传热不同之处在于,蒸发端和冷凝端位置,传热方向、蒸汽和液体流动方向不同,一种是沿着厚度方向传热,可以通过大面积冷凝带走更多热量;一种是沿着长度方向传热,可以传递较远距离并且保持优异的均温性能。一般来说,整体厚度小于 2 mm 的均热板称为超薄均热板。随着 5G 时代的到来,厚度进一步降低的超薄均热板需求日益突出。实现厚度进一步减小 (<0.4 mm) , 传热性能优异(热导率>5000 W/(m·K))的超薄均热板结构设计与制造是目前迫切需要的。有学者针对超薄均热板工作原理进行的理论和数值分析研究,并从理论角度提出了超薄均热板优化传热性能的方向。
SUBEDI 等建立了多热源和多散热器下超薄均热板传热理论模型(温度和压力分布),分析了丝网吸液芯几何尺寸包括丝网直径,分离间隔和厚度等因素对其极限传热功率的影响。结果表明,丝网吸液芯的厚度通过影响其毛细极限对超薄均热板极限传热能力具有重大影响;此外,超薄均热板极限传输功率还受限于电子设备正常运行的最高温度。
LEE 等针对丝网吸液芯超薄均热板,提出了超薄均热板极限传热能力与丝网吸液芯毛细性能、重力影响、蒸汽扩散阻力与液体流动阻力的理论计算关系,计算了超薄均热板传热热阻与等效热导率与吸液芯厚度关系。研究结果说明,超薄均热板最大传热能力随着吸液芯厚度的增加而增大,然而,等效热导率却随着吸液芯厚度的增加而减小。
PATANKAR 等提出一种超薄均热板 3D 传热数值模型模拟工作过程中热量传递,气液界面相变和蒸汽流动等,并通过模拟仿真对比分析发现离散沟槽双孔式冷凝吸液芯结构可以有效改善超薄均热板冷凝端温度均匀性,相比于均匀沟槽冷凝吸液芯超薄均热板,离散沟槽双孔式冷凝吸液芯超薄均热板冷凝端温差降低 37%。此外,该团队还提出一种基于超薄均热板的热阻网络模型来分析热阻与工质性能、输入功率和几何参数之间的关系,揭示了工质液体品质因数和蒸汽品质因数对超薄均热板传热性能的影响机理,并指出当超薄均热板厚度减小时,选择工质应该优先考虑工质的蒸汽品质因数,这也说明随着超薄均热板厚度越来越小,蒸汽对其传热性能的影响作用越来越大。
CHANG 等结合试验和数值仿真分析,以气液相变过程传热机理为基础,提出了超薄均热板等效热导率 keff 的半经验测试方法,如图 2a 所示。研究结果表明,等效热导率与超薄均热板的厚度、传热方向和传热功率等参数直接相关,并且当超薄均热板厚度范围在 0.3~0.5 mm 时,厚度参数对其传热性能具有重大影响。
图 2 超薄均热板的传热理论研究
李聪基于流体相变传热传质理论建立了超薄均热板稳态运行时热阻理论模型,研究了不同输入热功率和蒸汽腔厚度对超薄均热板热阻的影响。结果表明,当蒸汽腔厚度减小至0.3 mm 以后,超薄均热板热阻急剧增加,并且随着蒸汽腔厚度进一步减小,蒸汽流动产生的热阻占据超薄均热板总热阻的比重也越来越大,如图 2b 所示。这也说明极限超薄厚度均热板传热性能下降主要来源于蒸汽腔。通过以上研究可知,随着均热板进一步的超薄化,吸液芯与蒸汽腔厚度均被进一步压缩,进而导致均热板传热性能急剧下降。在常规超薄厚度下,液体在吸液芯中的流动是设计制造超薄均热板首要考虑因素;然而,在极端超薄厚度条件下,蒸汽在真空腔体内的流动阻力随着蒸汽腔厚度减小而急剧增大,逐渐成为另一个阻碍超薄均热板气液运行的关键因素。
此外,蒸汽腔厚度极小时,由于尺寸效应会导致蒸汽通道内液塞形成,阻碍蒸汽流动,还会抑制液体发生相变过程,进而严重影响超薄均热板的传热性能。因此,要实现极端厚度下超薄均热板的气液运行,要综合考虑吸液芯结构与蒸汽腔空间设计。
2 超薄均热板结构设计
由超薄均热板的传热工作原理可知,气液蒸发/冷凝相变、蒸汽扩散和液体回流是超薄均热板正常运行的重要环节。要实现超薄均热板气液循环运行,内部要满足压降平衡,即吸液芯驱动液体流动的毛细压力 ∆Pcap,要能够克服蒸发段到冷凝段蒸汽流动阻力 ∆Pv,冷凝段到蒸发段液体流动阻力和液体重力压降 ∆Pg,实现液体顺利回流至蒸发段。∆Pcap≥∆Pv+ ∆Pl+ ∆Pg (1)
保证这些环节的顺利进行,主要通过优化气液通道排布降低蒸汽流动阻力,同时也需要设计吸液芯结构提高吸液芯毛细压力并降低液体流动阻力。优化设计气液通道排布和吸液芯结构是实现超薄均热板的高性能和进一步超薄化的关键,也是目前行业界与学术界高度关注的焦点。2.1 气液通道排布设计
根据超薄均热板的气液通道排布方式可分为气液异面与气液共面结构排布,两种排布类型的超薄均热板气液运行与传热机理示意图如图 3 所示。
图 3 气液异面与气液共面结构超薄均热板传热示意图
由图 3a 可知,气液异面超薄均热板蒸汽通道和液体通道在厚度方向(Z 轴)上是相互分离的,并且蒸汽流动与液体流动在不同的平面(XOY 平面)进行。
图 3b 所示为新型气液共面超薄均热板气液运行与传热机理示意图,该类型超薄均热板蒸汽通道和液体通道在厚度方向(Z 轴)上是不可分离的,并且蒸汽流动与液体流动在同一平面(XOY 平面)内进行。两种气液运行与传热过程类似,都是蒸发段吸液芯中的工质液体吸收外界输入热量,发生蒸发相变变成工质蒸汽,并在压差作用下沿着蒸汽腔长度方向(Y 轴)流动流至冷凝段,工质蒸汽在冷凝段被带走热量,发生相变凝结变成工质液体,并在吸液芯毛细压力推动下流回至蒸发段,进行下一步吸热蒸发过程。超薄均热板在稳定运行下,气液循环持续不断地进行着。两种不同的是,气液异面超薄均热板气液相变方向与厚度方向(Z 轴)一致,气液共面超薄均热板气液相变方向则与宽度方向(X 轴)相同。目前的研究中超薄均热板气液排布方式只有这两种结构,以下分别对这两种气液排布的超薄均热板进行了综述。
2.1.1 气液异面
沿厚度方向传热均热板通常需要在上下壳板(蒸发端和冷凝端)布置两层吸液芯,中间支撑出蒸汽腔空间,类似“三明治”结构,是一种典型的气液异面超薄均热板结构。
STRUSS 等报道了一种厚度为 0.61 mm 的气液异面硅基超薄均热板,采用蚀刻法加工直径 5 μm,间隔 5 μm 和高度 40 μm 的阵列微针结构作为吸液芯,分布在上下壳板上,采用蚀刻法加工高度较高、周边带有微沟槽的支撑柱支撑上下壳板,留出中间蒸汽腔厚度为 0.13 mm,如图 4 所示。该类超薄均热板主要应用于沿厚度方向传热的大面积热源与冷源散热,由于一般需要两层吸液芯,限制了超薄均热板厚度进一步降低。
图 4 “三明治”气液异面超薄均热板
针对便携式移动电子设备狭小空间散热需求,超薄均热板沿着长度方向传热具有更优的均温性,能够有效保证芯片热量快速传递至电子设备壳体,散热效率高,同时只需要一层吸液芯,厚度相比于“三明治”结构均热板更低。
SHI 等报道了一种厚度为 0.65 mm 的气液异面超薄均热板,采用阵列微柱作为支撑柱,与吸液芯结构在厚度方向上相互分离。YANG 等制造了厚度为 0.53~0.6 mm 气液异面超薄均热板,液体通道采用微纳结构复合泡沫铜,蒸汽通道则采用电镀法在铜板上加工出阵列圆柱作为支撑柱,支撑柱之间的空间作为蒸汽腔,支撑柱另一端与吸液芯接触,实现气液异面结构设计。
CHEN 等设计制造了一种厚度仅为 0.43 mm 的气液异面铜超薄均热板,该超薄均热板采用口径为 46 μm(300 目)丝网作为吸液芯,湿法蚀刻加工支撑柱作为蒸汽腔,吸液芯和蒸汽腔在厚度方向上相互分离,两者厚度分别为 0.15 mm 和 0.08 mm,如图 5 所示。大量学者均采用该类气液异面结构(蒸汽腔层为柱状支撑柱组成的腔体,吸液芯层为整层多孔结构)的设计制造超薄均热板。
图 5 支撑柱-吸液芯分离气液异面超薄均热板与此同时,“双丝网”气液异面结构——粗孔丝网作为蒸汽腔,细孔丝网作为吸液芯的超薄均热板也被广泛学者采用。OSHMAN 等采用三层口径76 μm 铜丝网作为吸液芯,大口径(0.823 mm)尼龙丝网作为蒸汽腔,制备了厚度为 1.31 mm 的聚合物超薄热板,如图 6a 所示。该超薄均热板粗尼龙丝网与细铜丝网在厚度方向上相互分离,尼龙丝网形成大口径提供蒸汽流动通道,铜丝网小孔径具有较好的毛细压力,为液体流动提供流动通道和驱动力,气液相变在尼龙丝网与铜丝网接触界面上发生,是一种典型的气液异面结构。LEE 等制造了厚度为0.67 mm 的“双丝网”气液异面铜超薄均热板,该超薄均热板采用 3 层粗孔铜丝网作为蒸汽腔,1 层亲水处理过的细孔铜丝网作为吸液芯,如图 6b 所示。类似的气液异面结构设计,LIEW 等也分别制造了厚度为 1 mm 和 1.5 mm 的超薄均热板。
图 6 “双丝网”气液异面超薄均热板2.1.2 气液共面
由于内部空间充足,传统均热板的吸液芯与蒸汽腔基本都是气液异面结构设计,气液运动在不同平面进行,相互之间的干扰较少。现有的超薄均热板大部分都是采用气液异面结构设计,并通过减小吸液芯结构的厚度或者蒸汽腔的厚度来实现均热板变薄。但是,气液异面超薄均热板的总体厚度始终需要计算吸液芯结构与蒸汽腔厚度之和,目前很难实现 0.4 mm 以下厚度的超薄化。而 5G 时代下电子设备越来越紧凑,电子设备内部留给散热元件的空间被进一步压缩,这一趋势促使超薄均热板往小于0.4 mm 的厚度下探。而超薄均热板厚度的进一步降低,势必会减小蒸汽腔厚度,进而导致超薄均热板蒸汽阻力急剧增大。此外,随着蒸汽腔厚度的进一步减小,液体工质厚度方向小尺度毛细作用下,在蒸汽腔空间内形成液膜,进一步阻碍蒸汽流动,同时也抑制液体工质相变过程(与沸腾过程中所提及的膜态沸腾类似),称为液塞,会导致超薄均热板传热性能急剧下降,甚至失效。
华南理工大学汤勇教授团队创新性地提出气液共面新型气液通道排布方式,将蒸汽通道(蒸汽腔)与液体通道(吸液芯)排布在厚度方向上的同一平面上,蒸汽和液体流动在同一平面上进行,超薄均热板总体厚度可进一步下降。另外,通过气液通道的交替设置,气液共面均热板在宽度方向可以较好地扩展,特别适用于散热面积较大的场合。这逐渐受到其他研究者的关注。
HUANG 等对气液异面和气液共面两种超薄均热板的蒸汽与液体流动阻力进行了理论和数值模拟分析,如图 7 所示,超薄均热板内部空间厚度越小,气液通道最优配比下的气液共面结构超薄均热板的蒸汽与液体流动阻力总和相比于气液异面结构超薄均热板更小。气液共面结构在总腔体厚度不变的情况下,通过牺牲宽度方向上的空间来保证厚度较大的蒸汽通道,这随着超薄均热板整体厚度的减小将表现出越来越大的优势。
图 7 两种排布结构均热板流动阻力与内部空间理论关系
目前,压扁型超薄热管大多采用与气液共面相类似的结构设计。ZHOU 等将粉末或者丝网吸液芯置于圆管中间,通过相变压扁法制备得到厚度范围为 0.4~1.0 mm 的超薄热管,还研究了吸液芯与蒸汽腔的配比关系对超薄热管传热性能的影响。然而,基于气液共面结构超薄均热板的公开报导极其少。LÜ 等采用超亲水丝网吸液芯制备了尺寸为 100 mm × 50 mm × 0.95 mm 气液共面超薄均热板,测试结果表明该均热板可以传递热流密度 490 W/cm2以上。之后,又采用该结构制备厚度仅为 0.5 mm 的气液共面超薄均热板,并采用可视化试验研究了传热过程中蒸汽和液体流动现象,如图 8 所示。
图 8 气液共面超薄均热板及其气液排布结构HUANG 等采用四条螺旋编织丝网和底层平织丝网作为吸液芯,制造了厚度为 0.5 mm 的气液共面超薄均热板,测试了不同灌注量和摆放位置下超薄均热板的传热性能,如图 9 所示。研究结果表明,超薄均热板在灌注量为 100%时具有最优的传热性能,此时水平放置下超薄均热板的传热极限功率为 7.58 W;顺重力放置可以有效提高超薄均热板传热性能,顺重力放置下的超薄均热板等效热导率高达 25200 W/(m·K)以上。
HUANG 等还进一步优化了吸液芯排布结构,将螺旋编织丝网增加至六条以提高毛细性能,保持超薄均热板厚度为 0.5 mm,有效提高了超薄均热板极限传热功率至 10 W。LIU 等对比了不同螺旋编织丝网下超薄均热板的传热性能,研究结果表明,尺寸为 110 mm× 15 mm ×0.41 mm 的超薄均热板,排布三条编织丝网具有最优传热性能,在顺重力放置下能够传递最大传热量 6 W。
图 9 编织丝网间隔分布气液共面超薄均热板
最近,华南理工大学汤勇教授团队开发出厚度仅为 0.25 mm±0.03 mm 的气液共面结构超薄均热板,采用亲水处理的螺旋编织带作为吸液芯,测试结果表明该超薄均热板等效热导率可达 10000 W/(m·K)以上。这说明气液共面结构是实现超薄均热板进一步超薄化,突破目前超薄均热板临界厚度(0.4 mm)的关键。
2.2 吸液芯结构设计
超薄均热板的吸液芯结构具有驱动液体工质回流、提供液体工质流动通道、促进工质气液相变和将壳体热量传递至液体工质等功能,是均热板完成内部气液循环的重要部件之一。根据超薄均热板吸液芯结构的不同类型,可以将其分为微沟槽型、粉末烧结型、泡沫金属型、丝网烧结型和复合结构型。此外,随着微纳加工技术的兴起,微纳复合尺度吸液芯也受到高度关注。
2.2.1 微沟槽吸液芯
微沟槽吸液芯具有结构简单、渗透率高的优势,通常用于加工硅基、铝基均热板。LIM 等采用激光加工制备了深度为 0.3 mm 的扇形微沟槽吸液芯,并封装制造成尺寸为 56 mm × 8 mm × 1.5 mm 的超薄铜均热板,如图 10 所示。该超薄均热板测试输入功率到 13 W 时才出现烧干现象,并且在功率 8 W 时热阻为 5.45 ℃/W。
图 10 激光加工微沟槽吸液芯超薄均热板CHEN 等设计了一种厚度为 2 mm 的纵横交错微沟槽吸液芯铝超薄均热板,采用冲压工艺成型加工壳板,微铣削技术加工出表面覆盖颗粒结构的微沟槽作为吸液芯,并采用丙酮作为工质,如图 11 所示。测试结果表明,该铝基超薄均热板在水平测试下最大传输功率可达 160 W 以上,在 140 W 时达到最小热阻,热阻值为 0.156 ℃/W。
图 11 微铣削微沟槽吸液芯超薄均热板
PAIVA 等提出了尺寸为 100 mm × 30 mm × 2 mm 的铝基超薄均热板,采用平行金属线阵列结构作为微沟槽吸液芯,同时也作为真空腔体的支撑柱,如图 12 所示。测试结果表明,在不同工质(丙酮、甲醇和水)下该超薄均热板极限传热能力分别为0.19 W,0.23 W 和 1.25 W。
图 12 平行金属线微沟槽吸液芯超薄均热板
DING 等制造了尺寸为 30 mm × 30 mm ×0.6 mm 钛基超薄均热板,通过蚀刻加工高深宽比阵列微柱吸液芯,并采用化学氧化法在微柱表面生长了一层头发状纳米钛结构。通过传热性能测试试验可知,该超薄均热板最大等效热导率为 350 W/(m·K)。
总体来说,微沟槽具有加工简便,成本低等优点,但是相对于其他吸液芯,微沟槽吸液芯毛细力较小,液体工质回流速度较慢,会导致超薄均热板均温性能较差。
2.2.2 粉末烧结吸液芯
粉末烧结吸液芯具有高毛细压力,是常规厚度均热板最常用的吸液芯之一。LI 等采用枝状粉末烧结作为吸液芯,封装并测试了尺寸为 100 mm × 50 mm × 2 mm 的超薄均热板,如图 13 所示。测试结果表明,在水平测试下,该均热板能够有效传递120 W 热量,热阻仅为 0.196 ℃/W,等效热导率是铜板的 4 倍以上。
图 13 粉末烧结吸液芯超薄均热板
ZHANG 等系统地研究了不同粒径、不同形貌的铜粉烧结吸液芯,该吸液芯加工有交错互通槽,结果证明该吸液芯能够有效促进气泡成核、生长和脱离,提高超薄均热板界面相变传热性能。LI 等采用 900 ℃高温烧结制备了不同粒径铜粉烧结吸液芯,并通过可视化试验测试了该吸液芯毛细性能,优化粒径参数。
粉末烧结吸液芯虽然具有较大毛细压力,但是其渗透率较低,尤其是超薄均热板应用粒径更小的粉末,进一步降低渗透率。更重要的是,在极限超薄化条件下,粉末烧结吸液芯往往仅有数层粉末结合,结合力较小而容易导致脱落,从而会大幅度降低超薄均热板传热性能甚至完全失效。
2.2.3 泡沫金属吸液芯
泡沫金属吸液芯通常具有较高的毛细压力和较大的孔隙率。YANG 等提出一种微纳结构复合泡沫铜作为吸液芯,制造了总厚度为 0.53~0.6 mm 的超薄均热板,如图 14 所示。并研究了注液量、微纳结构、泡沫铜层数以及蒸汽腔厚度对超薄均热板性能的影响。结果表明,泡沫铜层厚度越大、蒸汽腔厚度越大,超薄均热板传热性能越好,并且厚度轻微的增加能够导致超薄均热板传热性能极大的提升。研究中,超薄均热板等效导热系数可以达到 2207 W/(m·K),极限传热功率可达 22.66 W 以上。
图 14 泡沫金属吸液芯超薄均热板
然而,与粉末烧结吸液芯类似,泡沫金属结构孔隙较高,并且分布不规则,导致其结合强度不够牢固,力学性能较低,且制备工艺较为复杂,成本较高,限制其在极限超薄化均热板吸液芯的应用。
2.2.4 丝网烧结吸液芯
丝网吸液芯是近年来针对均热板厚度需求开发出来的,具有孔隙率大、厚度更薄、结构规则、柔性较好等优点,非常适用于目前均热板超薄化需求。XU 等烧结四层丝网作为吸液芯,制备有效尺寸为 35 mm × 35 mm × 0.62 mm 的超薄均热板,研究了强制风冷下超薄均热板沿着厚度方向的传热性能,如图 15 所示。研究表明,采用该超薄均热板的和比采用相同厚度铜板下热源温度降低了 20℃,并且沿厚度方向上可传递最大热流密度可达 425 W/cm2,具有非常高的极限传热能力。
CHEN 等开发了一种具有高性价比且易于大规模推广的梯度孔隙铜丝网,通过调控丝网内部孔隙梯度分布,能够有效提高丝网吸液芯结构毛细传输性能,同时加速相变过程中的气泡生长,促进超薄均热板蒸发端的相变蒸发过程。
SHI 等开发了一种尺寸为 80 mm × 50 mm ×0.65 mm 的超薄均热板,采用口径为 76 μm(200 目)的丝网作为吸液芯,通过蚀刻圆柱支撑柱来支撑蒸汽腔体,蒸汽腔体高度为 0.2 mm。该研究探索了倾斜角度和注液量等参数对超薄均热板传热性能的影响,发现该超薄均热板在输入功率为 7.1~13.7 W 时具有较好的传热性能,在最优注液量下,超薄均热板表现出较低的热阻(1.2 ℃/W)。
图 15 丝网烧结吸液芯超薄均热板
HUANG 等采用一层大口径(0.89~1.58 mm)粗丝网作为蒸汽腔,两层小口径(154~77 μm)细丝网烧结作为吸液芯,制备了尺寸为 100 mm × 65 mm ×1.26~1.77 mm 的超薄均热板,研究了不同口径丝网、不同冷却水温和不同放置角度对超薄均热板传热性能的影响,如图 16 所示。其中最优超薄均热板(SP2,厚度 1.58 mm)可以传递热量 50 W 以上,在50 W 下热阻仅为 0.107 ℃/W,等效热导率可达5 000 W/(m·K)以上。类似的,LEIW 等采用大口径尼龙丝网作为蒸汽腔,3 层口径为 76 μm(200 目)铜丝网通过电沉积工艺结合在一起作为吸液芯,并在丝网表面利用原子层沉积法加工了超亲水涂层,最终开发了有效尺寸为59 mm × 50 mm × 1mm的超薄均热板。测试结果表明,该超薄均热板最高可传递热量 40 W。
图 16 丝网烧结吸液芯超薄均热板
根据丝网烧结吸液芯超薄均热板研究现状可知,丝网是超薄均热板最具有应用前景的吸液芯之一,然而,丝网吸液芯仍存在毛细压力较低的不足。
2.2.5 复合结构吸液芯
复合结构吸液芯一般是结合上述吸液芯优点,制备出具有更优异性能的超薄均热板。OSHMAN 等采用沟槽复合丝网结构作为吸液芯,制造了尺寸为 40 mm × 40 mm × 1.2 mm 的聚合物超薄均热板,如图 17 所示。该团队研究了超薄均热板在不同重力加速度和输入热功率下的传热性能,结果表明,在 40 W 热输入功率下,超薄均热板在加速度为 0~10g 的等效热导率为 1653~436 W/(m·K)。
HUANG 等采用铜粉丝网复合烧结作为吸液芯,制备了尺寸为 220 mm × 50 mm× 1.34 mm 的超薄均热板,并将其成功应用到质子交换燃料电池辅助散热。结果表明,采用该铜粉丝网复合烧结吸液芯超薄均热板后,燃料电池工作温度与其表面最低温的温差降低至 0.5℃。
图 17 丝网复合沟槽吸液芯超薄均热板
DENG 等提出均匀径向发散沟槽复合铜粉结构作为均热板蒸发端吸液芯,并研究了铜粉口径、形状以及加热面积对均热板传热性能的影响。测试结果表明,该均热板能够传递高达 280 W/cm2的热流密度,而热阻仅为 0.15 ℃/W。此后,CHEN 进一步优化沟槽铜粉复合吸液芯,通过烧结铜粉至Ω 型内凹微沟槽,为蒸汽和液体提供分离的高效流动通道,优化均热板传热性能,并成功将其应用到高功率 LED,降低了 LED 模组基体温度 27%。
复合结构吸液芯可以结合不同类型吸液芯的优势,具有较优的综合毛细性能,但是其复杂的制造工艺与极为有限的吸液芯空间限制了复合结构吸液芯在极限超薄化均热板中的应用和发展。
2.2.6 微纳复合尺度吸液芯
近年来快速发展的微纳加工技术为超薄均热板提供了新型复合多尺度吸液芯的选择。RYU 等采用混合化学溶液NaClO2,NaOH和Na3PO4·12H2O在泡沫铜吸液层和微柱制备一层纳米结构,有效提高微柱吸液芯的毛细性能,可传递最大热流密度相比对照组增加超过 150%,并且具有超高等效换热系数(heff >5 W/(cm2·K))。
JI 等提出采用纳米结构来调控超薄均热板蒸发端和冷凝端润湿性,进而提高超薄均热板传热性能。对比了三种超薄均热板 IE-IE(蒸发端与冷凝端均亲水),SIE-IC(蒸发端超亲水,冷凝端亲水)和SIE-SOC(蒸发端超亲水,冷凝端超疏水)的传热性能,发现样品 IE-IE,SIE-IC 和 SIE-SOC 在相同测试条件下热阻依次降低。
WEN等提出一种化学蚀刻法在烧结丝网吸液芯表面生长纳米草和微多孔结构,如图 18 所示。试验证明,这两种微纳复合尺度结构能够有效提高在丝网吸液芯毛细性能和极限热传输能力。此外,对比纳米草和微孔结构,微孔结构由于具有更低流动阻力和更多汽化成核位点,具有更高的极限传输热流密度。TANG 等采用表面氧化处理法在铜编织丝网表面制备了一层球状微纳结构层,并探索了处理时间与高温烧结温度对微纳结构层的影响,发现经过 15 min 表面处理与 500 ℃高温烧结后的编织丝网毛细上升高度比未处理丝网可以提升 60%以上。
图 18 微纳复合尺度丝网吸液芯LUO 等采用单步法电沉积方式加工了森林状结构作为吸液芯,该结构形成大量的 Ω 型微沟槽,同时其表面具有大量的类似树枝微纳结构,被证明具有优异的毛细性能,如图 19 所示。测试结果表明,工质无水乙醇在森林状结构吸液芯中爬升最高高度可以达到 88 mm。采用该树枝状吸液芯制造出厚度为 0.6 mm 的超薄均热板,在 6 W 时温差仅为1.2℃,等效热导率可达 12600 W/(m·K)。
图 19 微纳复合尺度吸液芯超薄均热板
总体来说,在吸液芯表面加工微纳复合结构层可以有效提高吸液芯毛细性能,进而提高超薄均热板传热性能,同时微纳结构层厚度几乎可以忽略,非常适用于超薄均热板厚度极薄下用以强化吸液芯的毛细性能。
综上所述,目前超薄均热板厚度难以做到0.4 mm 以下厚度,主要瓶颈在于现有气液异面结构设计下导致了吸液芯毛细压力不够、蒸汽腔厚度太小引起的阻力太大和液塞现象。结合超薄均热板结构设计研究现状可知,通过气液共面结构降低蒸汽腔阻力和阻碍液塞现象的形成,同时采用微纳结构复合丝网吸液芯提高吸液芯毛细压力,是设计制造极限超薄化均热板的必然趋势。
3 超薄均热板壳体材料与封装方法
超薄均热板壳体材料与实际应用场景的需求紧密相连。一般来说,绝大部分超薄均热板壳体材料采用铜,主要是因为铜具有高导热系数和可加工性,对于实现超薄均热板优异的传热性能具有较大优势。而其他特殊应用场合,例如对轻量化需求较高的场景如航空航天领域,通常采用铝壳体超薄均热板;半导体芯片一体式集成散热系统,对热膨胀系数匹配要求极高的场景,则采用硅作为超薄均热板壳体材料;近年来柔性电子器件快速发展,对超薄均热板提出新的柔性化需求,聚合物也逐渐成为超薄均热板壳体材料的焦点。
焊接封装制造是超薄均热板主要成形工艺,与壳体材料息息相关,对超薄均热板正常运行和工作寿命具有重要影响。目前,超薄均热板常见的焊接封装工艺主要包括扩散焊、钎焊、热熔胶热压黏接等。
扩散焊一般是在高温高压下超薄均热板上下壳板紧密接触,两壳板原子间发生扩散,从而达到密封作用,也称为固相扩散。该工艺对设备要求高,成本较高,但具有焊接质量好、焊接强度大、无需额外增添焊料等优势,通常用于铜、铝等金属均热板焊接,是目前超薄均热板常见的焊接方式。
ISAACS 等采用扩散焊接将多层丝网和壳板焊接起来,封装成厚度为 0.85 mm 的超薄均热板,LI 等采用扩散焊接(高温 850℃ 高压下保温 30 min)的方式封装了铜超薄均热板。
钎焊则是在焊缝中添加焊料,在利用焊料熔化连接上下壳板,密封超薄均热板。钎焊虽然需要添加焊料,但是对设备要求不高,只需要烧结温度达到焊料熔点即可完成焊接,也是目前超薄均热板常用的焊接方式。焊料焊接对超薄均热板材料要求较低,仅需要能与材料表面润湿贴合,可用于金属铜、铝、不锈钢和聚合物高分子超薄均热板的焊接。例如,YANG 等通过采用高低温焊料钎焊封装了 FR4 基超薄均热板,YANG 等也是通过钎焊方式封装了厚度为 0.53~0.60 mm 的超薄铜均热板,焊接温度为 300℃。
热熔胶热压黏接工艺主要是通过热塑性聚合物膜来黏接超薄均热板壳板,具有操作简便、成本低廉的优点,通常用于高分子聚合物超薄均热板的密封封装。例如,LEWIS 等采用氟化丙烯热压黏接封装了聚合物高分子超薄均热板,热压工艺仅需要在 300℃ 和约 500 kPa 的压力下完成。OSHMAN 等也采用热压接合工艺密封聚合物超薄均热板边沿,与抽口相接的聚合物边沿则采用高真空环氧树脂密封。
综上所述,目前金属壳体的超薄均热板封装相对比较成熟,但是随着均热板进一步超薄化,封装过程中极薄壳体容易出现坍陷、破裂等问题,可通过优化支撑结构、提高壳板材料硬度和降低封装温度等方面进一步完善高可靠性的封装工艺。而对于柔性聚合物超薄均热板,采用热压黏接技术虽然能够进行简便、低成本的封装,但是仍处于初步探索阶段,远未形成完整、可靠的封装工艺。提高聚合物超薄均热板封装成形的可靠性是实现其大规模应用所面临的关键技术问题。
4 结论与展望
随着第五代移动通信技术(5G 技术)的出现与快速发展,电子产品尤其是智能手机、平板电脑等产品,越发朝着高性能、高集成和微型化的方向发展。高性能和高集成化的电子芯片在狭小空间内将产生极大的热流密度和超高的工作温度,进一步引发严峻的散热问题,导致电子芯片无法正常工作,从而制约其进一步发展。
超薄均热板具有优异的导热性能,较大传热面积、较好的均温性能和高可靠性等优点,是解决电子设备散热问题的首要途径。为满足 5G 时代下现代微型化电子设备散热需求,均热板极限超薄化是当前业界和学术界的研究热点。
然而,由于超薄均热板的研究时间较短,极端厚度下系统的理论研究极度缺乏。并且随着均热板厚度尺寸的进一步减小,超薄均热板蒸汽流动阻力急剧增大,实现气液循环运行难度大幅度增加。同时过小的尺寸需求也导致超薄均热板壳体支撑柱、吸液芯与焊接封装等加工难度增加。
因此,建立极端超薄化均热板全新系统的理论体系,优化设计吸液芯结构与气液通道排布结构,开发高效可靠的超薄均热板封装制造工艺,对促进超薄均热板在便携式轻薄电子设备散热方面的发展和应用具有重要意义。
此外,针对不同应用场景的需求,如热膨胀系数匹配和柔性弯曲等,超薄均热板可通过调整壳体材料,例如采用硅/陶瓷和聚合物基体等,在实现高效传热同时实现特殊应用需求。结合目前超薄均热板研究现状,研制传热性能优异、极端超薄化均热板,需从以下方面进行考虑。
(1) 加强极端超薄下均热板的理论研究。
目前关于超薄均热板的理论大部分为常规尺寸下的气液流动规律和相变传热分析。例如,支撑柱的主要理论设计依据以降低蒸汽流动阻力为主,蒸汽通道尺寸对蒸汽流动阻力的影响规律等。然而,在极端超薄尺寸下,超薄均热板壳板厚度急剧降低,壳板极易发生塌陷,进而导致超薄均热板蒸汽通道变形,增大蒸汽阻力。壳板塌陷成为极薄壳板支撑柱设计的首要选择,而目前壳体形变理论研究较少。
此外,在极端超薄下,蒸汽腔体由于尺寸效应具有一定的毛细力,会吸附液体工质形成液塞,导致蒸汽通道堵塞。液塞现象对于超薄均热板气液运行与相变传热的理论还有待进一步研究。因此,需进一步针对极端超薄下均热板壳体支撑结构形变(例如优化支撑结构和提高壳板硬度等)与规避液塞现象(例如增加横向均布超亲水结构来防止液塞形成)等系统的理论研究。
(2) 优化设计气液共面结构。
目前超薄均热板主流的气液通道排布结构主要为气液异面结构。随着厚度进一步减小,蒸汽流动阻力急剧增大,进而导致气液循环难以进行。目前业界量产的气液异面结构超薄均热板最薄厚度始终在 0.4 mm 左右,接近基于该结构超薄均热板的厚度极限,难以进一步突破变薄。在极端超薄化下气液共面结构对于蒸汽与液体流动具有更小的阻力,是超薄均热板实现进一步超薄化的较优结构。因此,研制基于气液共面结构的超薄均热板,优化气液通道配比与内部空间排布,是实现超薄均热板进一步超薄化的关键。
(3) 设计高性能吸液芯结构。
目前超薄均热板吸液芯结构主要为微沟槽、粉末烧结、泡沫金属、丝网烧结等单一结构与两种类型的复合结构。然而,单一类型的吸液芯结构通常难以全面调控其孔隙率,毛细压力、渗透率和整体尺寸,这些因素综合决定了超薄均热板吸液芯的优异毛细性能。吸液芯的毛细性能好坏对超薄均热板性能起到决定性的作用。因此,开发新型高性能吸液芯结构制造方法,结合常用吸液芯结构与微纳结构技术,制造多尺度复合吸液芯结构,可以更好地控制更好地控制其孔隙率,毛细压力、渗透率和整体尺寸,获取具有更优异毛细性能的吸液芯。
(4) 发展新的超薄均热板高可靠性封装制造工艺。
目前针对金属壳体超薄均热板的封装焊接工艺,包括扩散焊接和钎焊等,在极薄壳体下仍然存在一些的缺陷。扩散焊接对设备需求极高,并且需要接近壳体材料熔点温度进行,这极大限制了高毛细性能微纳复合尺度吸液芯结构在超薄均热板中的应用;回流焊接温度相对较低,但是需要额外增添焊料,而焊料需要针对不同壳体进行开发,制造工艺复杂。更重要的是,在封装焊接过程中,高温容易导致极薄壳体出现烧穿、褶皱和破裂等现象,严重影响超薄均热板运行可靠性。
而聚合物超薄均热板主要封装成形技术——热压黏接,面临着微泄露的风险、并且具有不耐腐蚀,不受高温等不足,并且在反复弯折的情况下壳体连接部分很容易发生开裂,从而导致内部工质泄漏、壳体膨胀等问题,严重影响其相变传热性能。因此,开发新型高可靠性封装成形工艺可以进一步促进超薄均热板的应用和发展。
来源:机械工程学报
-
移动通信
+关注
关注
10文章
2537浏览量
69387 -
电子芯片
+关注
关注
3文章
52浏览量
14900 -
5G
+关注
关注
1340文章
47809浏览量
554329
发布评论请先 登录
相关推荐
柔性导热垫有什么作用?怎么使用?
国家专利高端材料-超薄高导热绝缘氮化硼膜
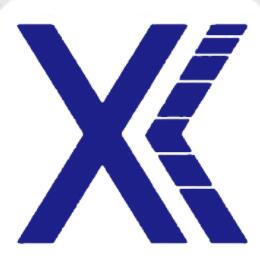
超薄高导热绝缘の膜材フィルム材料
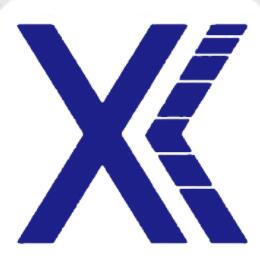
5G高导热绝缘透波氮化硼膜材の折弯测试
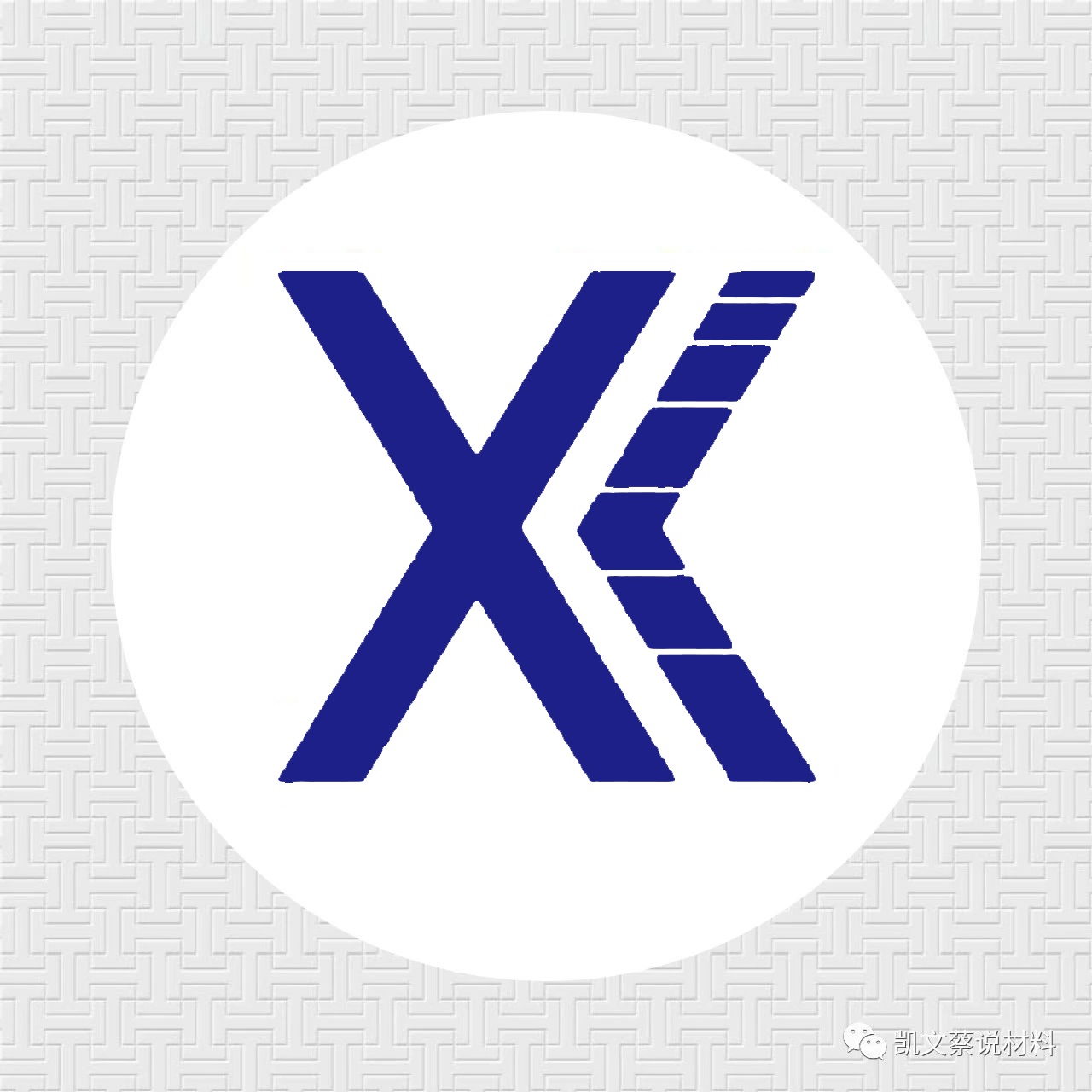
超薄高导热绝缘氮化硼膜的模切加工
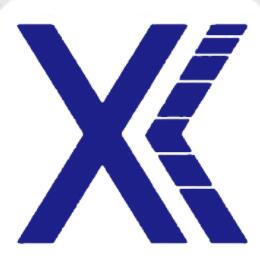
六方氮化硼纳米片导热复合材料的研究进展
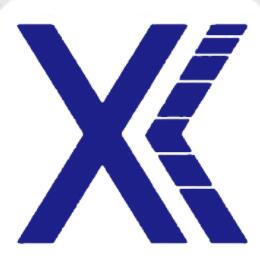
5G新材料超薄高导热绝缘低介电氮化硼膜材
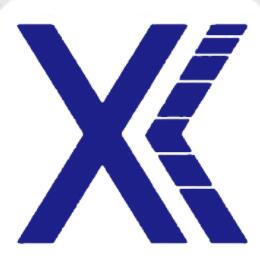
5G高导热绝缘氮化硼膜材垫片介绍
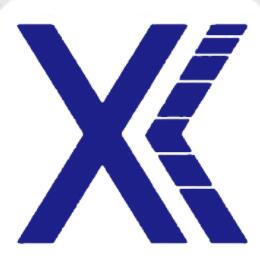
高导热绝缘氮化硼膜材在5G的应用探讨
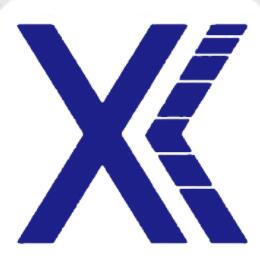
超薄高导热绝缘氮化硼膜的TG值及耐温性测试
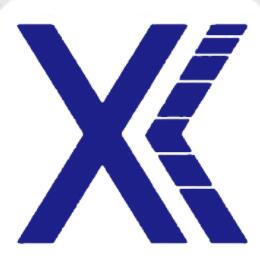
六方氮化硼纳米片导热复合材料及高品质氮化硼粉的介绍
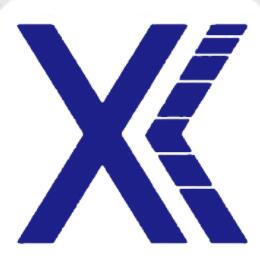
二维氮化硼绝缘高导热低介电材料介绍应用
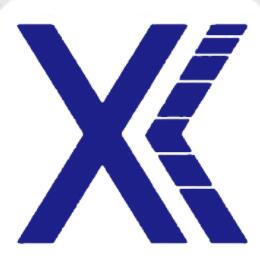
评论