近年来,随着5G、新能源等高频、大功率射频及电力电子需求的快速增长,硅基半导体器件的物理极限瓶颈逐渐凸显,如何在提升功率的同时限制体积、发热和成本的快速膨胀成为了半导体产业内重点关注的问题,以碳化硅为首的第三代半导体材料在这一趋势下逐渐从科研走向产业化,并成为替代部分硅基功率器件的明确趋势。然而,目前行业仍存在一些挑战和改进的空间。未来需要对产业链各环节进行优化和改进。
下面,我们将从半导体材料的发展过程入手,介绍碳化硅作为第三代半导体材料的优势,同时对半导体器件进行分类。此外,我们将对碳化硅产业链各环节进行深入梳理,分析国内外的发展状况,并展望未来的发展趋势。通过这些信息,希望能够为大家了解碳化硅行业提供帮助。
01
优可测行业检测案例
优可测作为专注于高精度测量仪器及传感器品牌,一直以来都密切关注着碳化硅行业的发展动态,深知碳化硅在能源、电子、光伏等领域的重要性,致力于为中国科研事业添砖加瓦,推动碳化硅行业的发展。
下面是优可测在SiC行业中的部分检测案例:
白光干涉仪AM系列:
SiC表面粗糙度测量薄膜厚度测量仪AF系列:
02
概述
1、半导体材料发展过程
根据研究和规模化应用的时间先后顺序,业内将半导体材料划分为三代。
第一代半导体(间接带隙&窄带隙):1950年起,以硅(Si)为代表的半导体材料取代了笨重的电子管,推动了以集成电路为核心的微电子产业迅速发展。硅材料属于间接带隙(电子跃迁至导带时需要改变动量,光利用率低)且带隙窄(不耐压),适用于低压、低频、中功率集成电路,在光电子领域和高频高功率器件方面受限。
第二代半导体(直接带隙&窄带隙):1990年起,以砷化镓(GaAs)、磷化铟(InP)为代表的半导体材料崭露头角,属于直接带隙且具有相对宽的带隙,载流子速度更快、噪音更低。其适用于制作高速、高频、大功率以及发光电子器件,但受限于材料本身,难以满足更高功率、更高电压、更高频率的器件需求。
第三代半导体(直接带隙&宽带隙):近年来,以氮化镓(GaN)、碳化硅(SiC)为代表的半导体材料备受关注。碳化硅作为第三代宽禁带半导体材料的代表,在禁带宽度、击穿电场、热导率、电子饱和速率、抗辐射能力等关键参数方面具有显著优势,满足了现代工业对高功率、高电压、高频率的需求,主要被用于制作高速、高频、大功率及发光电子元器件。
2、SiC作为第三代半导体材料优势明显
SiC作为第三代半导体材料具备诸多显著优势:
(1)耐高压:SiC材料相比于Si材料具有10多倍的击穿场强,因此可以通过更低的电阻率和更薄的漂移层实现更高的击穿电压,相同的耐压值下,SiC功率模块导通电阻/尺寸仅为Si的1/10,功率损耗大幅减少。
(2)耐高频:SiC材料不存在电流拖尾现象,能够提高元件的开关速度,是硅(Si)开关速度的3-10倍,从而适用于更高频率和更快的开关速度。
(3)耐高温:SiC材料具有禁带宽度大(约Si的3倍)、热导率高(约Si的3.3倍),熔点高(2830℃,约Si-1410℃的两倍)的特点,因此SiC器件在减少电流泄露的同时大幅提高工作温度。
SiC不同晶体结构性能各异,4H-SiC综合性能最佳。SiC由于C原子和Si原子结合方式多样,有200多种同质异型晶体结构,其中6H-SiC结构稳定,发光性能好,适合光电子器件;3C-SiC饱和电子漂移速度高,适合高频大功率器件;4H-SiC电子迁移率高、导通电阻低、电流密度高,适合电力电子器件。4H-SiC是目前综合性能最好、商品化程度最高、技术最成熟的第三代半导体材料,是制造高压、高温、抗辐照功率半导体器件的理想材料。
3、碳化硅器件定义及分类
生产碳化硅器件主要包括衬底、外延、器件制造(设计、制造、封测)三大环节。按照电阻性能的不同分为导电型碳化硅功率器件和半绝缘型碳化硅基射频器件:
(1)导电型碳化硅功率器件
功率器件又被称为电力电子器件,是构成电力电子变换装置的核心器件。电力电子器件是对电能进行变换和控制,所变换的“电力”功率可大到数百MW甚至GW,也可以小到数W甚至1W以下。电力电子装置正是实现电能高质量高效转换、多能源协调优化、弱电与强电之间控制运行、交流与直流之间能量互换、自动化高效控制等的重要手段,也是实现节能环保、提高电能利用效率的重要保障。
导电型碳化硅功率器件主要是通过在导电型衬底上生长碳化硅外延层,得到碳化硅外延片后进一步加工制成,品种包括造肖特基二极管(SBD)、MOSFET(金属氧化物半导体场效应晶体管)、IGBT(绝缘栅双极性晶体管)等,主要用于电动汽车、光伏发电、轨道交通、数据中心、充电等基础建设。目前碳化硅二极管、MOSFET已经开始商业化应用。
(2)半绝缘型碳化硅基射频器件
射频器件在无线通讯中扮演信号转换的角色,是无线通信设备的基础性零部件,主要包括功率放大器、滤波器、开关、低噪声放大器、双工器等。
半绝缘型碳化硅基射频器件是通过在半绝缘型碳化硅衬底上生长氮化镓外延层,制得碳化硅基氮化镓外延片后进一步制成,包括HEMT(高电子迁移率晶体管)等氮化镓射频器件,主要用于5G通信、车载通信、国防应用、数据传输、航空航天。碳化硅、氮化镓材料的饱和电子漂移速率分别是硅的2.0、2.5倍,因此碳化硅、氮化镓器件的工作频率大于传统的硅器件。然而,氮化镓材料存在耐热性能较差的缺点,而碳化硅的耐热性和导热性都较好,可以弥补氮化镓器件耐热性较差的缺点,因此业界采取半绝缘型碳化硅做衬底,在衬底上生长氮化镓外延层后制造射频器件。
03
行业现状及市场空间
1、全球碳化硅器件市场格局由海外巨头主导
海外企业由于占据先发优势,在技术进展与产能规模上具备一定垄断地位。根据数据,市场份额由海外巨头意法半导体、Wolfspeed、罗姆、英飞凌、三菱电机、安森美等厂商垄断,其中最大的碳化硅器件商为意法半导体,是特斯拉车载碳化硅器件的主要供应商,市占率达到40%,其次是英飞凌,市占率22%。全球TOP6占据95%以上的市场份额。
2、海外技术禁运
在宽禁带半导体领域,下游应用企业已在调整供应链,支持国内企业。数家国内宽禁带半导体企业的上中游产品陆续获得了下游用户验证机会,进入了多个关键厂商供应链,逐步开始了以销促产的良性发展。
3、下游需求不断扩大,百亿市场空间可期
未来随着碳化硅器件在新能源汽车、能源、工业、通讯等领域渗透率提升,碳化硅器件市场规模有望持续扩大,其中新能源车和光伏为重要领域。
(1)新能源汽车:SiC器件主要应用在PCU(动力控制单元,如车载DC/DC)和OBC(充电单元),相比于Si器件,SiC器件可减轻PCU设备的重量和体积,降低开关损耗,提高器件的工作温度和系统效率;OBC充电时,SiC器件可以提高单元功率等级,简化电路结构,提高功率密度,提高充电速度。
(2)光伏发电领域:SiC材料具有更低的导通电阻、栅极电荷和反向恢复电荷特性,使用SiC-Mosfet或SiC-Mosfet与SiC-SBD结合的光伏逆变器,可将转换效率从96%提升至99%+,能量损耗降低50%+,设备循环寿命提升50倍。
新能源汽车是未来第一大应用市场。2027年全球导电型SiC功率器件市场规模有望达63亿美元,2021-2027年CAGR达34%;2027年新能源汽车导电型SiC功率器件市场规模有望达50亿美元,占比高达79%。
全球已有多家车企的多款车型使用SiC。2018年特斯拉率先在Model3上搭载SiC,从此拉开了碳化硅大规模上车序幕,蔚来、比亚迪、吉利、现代汽车等车企纷纷跟进,特斯拉凭借先发优势以及Model3、ModelY等主力车型热销,一直是SiC装车的主力担当。随着比亚迪汉EV、蔚来ES6、理想L9等热门车型的陆续上市,SiC装车量得到进一步扩大。据Clean Technica,2023年1-5月SiC车型超100万辆。
从行业趋势看,SiC上车是大势所趋。特斯拉曾在2023年3月初的投资者大会上表示,将减少75%的SiC用量,一度引发SiC未来发展前景不明的猜测,但近期全球汽车市场却用实际行动表达了对SiC的支持,如全球第四大汽车集团Stellantis宣布,已与多家供应商签订包括SiC在内的半导体合作协议,总价值超80亿元;博格华纳向安森美SiC产品下定金额超72亿元;瑞萨电子也与Wolfspeed签署了一份为期10年的碳化硅晶圆供应协议等。
光伏第三代半导体功率器件市场前景广阔。光伏电站直流端电压等级逐渐从1000V提升至1500V,未来有望再提升至2000V。大电压环境下碳化硅功率器件的性能优势凸显。伴随光伏逆变器出货量的快速增长以及碳化硅功率器件渗透率的提升,光伏碳化硅功率器件市场将迅速成长。根据CASA数据,2021年中国光伏领域第三代功率半导体的渗透率超过13%,市场规模约4.78亿元,同比增长56%,预计2026年光伏用第三代半导体市场空间将接近20亿元,五年CAGR超过30%。
随着5G建设的加速,半绝缘型碳化硅器件市场有望持续增长。半绝缘型碳化硅器件主要用于5G基站、卫星通信、雷达等方向,随着5G建设的加速,尤其是MassiveMIMO技术的推广,半绝缘型碳化硅基氮化镓器件市场规模将不断扩大。根据YOLE的数据,2020年封装的氮化镓射频器件市场规模约为8.91亿美元,其中超过99%都是采用碳化硅衬底,到2026年,这部分市场规模有望增长至22.22亿美元,年复合增速17%。
产业链分析
从工艺流程上看,首先由碳化硅粉末通过长晶形成晶锭,然后经过切片、打磨、抛光得到碳化硅衬底;衬底经过外延生长得到外延片;外延片经过光刻、刻蚀、离子注入、沉积等步骤制造成器件。
目前SiC MOSFET的应用受到成本高昂限制,据中科院数据,同一级别下SiC MOSFET的价格比Si基IGBT高4倍。碳化硅衬底、外延成本分别占整个器件的47%、23%,合计约70%,后道的器件设计、制造、封测环节仅占30%。这与硅基器件成本构成截然不同,硅基器件生产成本主要集中在后道的晶圆制造约50%(碳化硅器件制造也包含晶圆制造,但成本占比相对较小),衬底成本占比仅为7%。SiC产业链价值量倒挂的现象说明上游衬底厂商掌握着核心话语权,是国产化突破的关键。
1、衬底
衬底定义:沿特定的结晶方向将晶体切割、研磨、抛光,得到具有特定晶面和适当电学、光学和机械特性,用于生长外延层的洁净单晶圆薄片。
从电化学性质差异来看,碳化硅衬底材料可以分为导电型衬底(电阻率区间15~30mΩ•cm)和半绝缘型衬底(电阻率高于105Ω•cm)。这两类衬底经外延生长后分别用于制造功率器件、射频器件等分立器件。其中,半绝缘型碳化硅衬底主要应用于制造氮化镓射频器件、光电器件等。通过在半绝缘型碳化硅衬底上生长氮化镓外延层,制得碳化硅基氮化镓外延片,可进一步制成HEMT等氮化镓射频器件。导电型碳化硅衬底主要应用于制造功率器件。与传统硅功率器件制作工艺不同,碳化硅功率器件不能直接制作在碳化硅衬底上,需在导电型衬底上生长碳化硅外延层得到碳化硅外延片,并在外延层上制造肖特基二极管、MOSFET、IGBT等功率器件。
大尺寸衬底有效摊薄成本,成为行业趋势。目前碳化硅衬底主流尺寸是4/6寸,其中半绝缘型碳化硅衬底以4寸为主,导电型碳化硅衬底以6寸为主。大尺寸可以摊薄单位芯片的成本,当衬底从6寸扩大到8寸时,可切割出的碳化硅芯片(32mm2)数量有望从448颗增加到845颗,增加了75%。目前国际上龙头企业的碳化硅衬底正从6寸往8寸发展,国际龙头Wolfspeed、II-VI以及国内龙头天岳先进等都已成功研发8英寸衬底产品。
(1)衬底市场份额
海外龙头起步较早,长期垄断SiC衬底市场,CR3达80%。海外龙头企业在碳化硅领域起步较早,其中Wolfspeed和II-VI公司在研发和产业化方面领先国内数十年,例如Wolfspeed/II-VI的6寸半绝缘型碳化硅衬底量产时间早于国内天岳先进15/10年。根据Yole数据,2020年海外厂商的SiC衬底CR3达78%,其中Wolfspeed市占率45%,罗姆(收购SiCrystal)市占率20%,位居第二;国内龙头天科合达、天岳先进仅为3%、3%。
导电型衬底Wolfspeed一家独大,绝缘型衬底天岳先进入围前三。2020年全球导电型SiC衬底依旧被Wolfspeed、II-VI、罗姆垄断,CR3高达90%,其中Wolfspeed市占率高达62%,一家独大;半绝缘型衬底中天岳先进表现亮眼,市占率约30%,仅次于全球龙头II-VI、Wolfspeed的35%、33%。
(2)国内衬底企业技术水平明显落后于国外企业
海外企业已领先6寸碳化硅衬底供应,并开始供应8寸衬底。中国企业在单晶衬底方面以4英寸为主,国内企业已具备6寸SiC衬底量产能力,正积极布局8寸。
天科合达、天岳先进6寸衬底参数对标海外。国内企业的大尺寸碳化硅衬底的量产进度仍与海外龙头有较大差距,但在6寸衬底的技术参数上,国内龙头天科合达、天岳先进与海外Wolfspeed、II-VI不存在明显差距。
(3)碳化硅衬底市场规模预测
预计2027年全球导电型碳化硅衬底市场规模将增至21.6亿美元。受下游民用领域的持续景气,如新能源汽车与光伏,导电型SiC衬底市场规模不断扩容。根据Yole数据,2018年,全球导电型SiC衬底市场规模为1.7亿美元,2020年增长至2.8亿美元,复合增长率为26%。预计2027年全球导电型碳化硅衬底市场规模将增长至21.6亿美元。
预计2026年全球半绝缘型SiC衬底市场规模将增至4.33亿美元。受益于5G基建加快布局和全球地缘政治动荡,半绝缘型SiC衬底市场增长空间巨大。根据Yole数据,2021年全球半绝缘型SiC衬底市场规模约为2.1亿美元,预计2026年将增至4.33亿美元。
(4)碳化硅衬底的生产流程
碳化硅衬底的生产流程包括长晶、切片、研磨和抛光环节。
长晶:核心环节,通过物理气相传输法(PVT)在高温高压的条件下,将碳化硅原料气化并沉积在种子晶上,形成碳化硅单晶锭。需要精确控制各种参数,如温度、压力、气流、硅碳比等,以保证晶体的质量和纯度。
切片:将碳化硅单晶锭沿着一定的方向切割成薄片。由于碳化硅的高硬度和脆性,切割过程需要使用特殊的工具,如钻石线或多线切割机。切割过程会造成晶片表面的刀痕和损伤层,需要后续的研磨和抛光处理。
研磨:去除切割造成的表面缺陷和控制晶片厚度。根据研磨的目的和精度,可以分为粗磨和精磨两个阶段。研磨过程需要使用高硬度的磨料,如碳化硼或金刚石粉。
抛光:提高晶片表面光洁度和平整度。抛光也可以分为粗抛和精抛两个阶段。粗抛主要采用机械抛光方式,使用较小粒径的硬磨料,如B4C或金刚石等。精抛主要采用化学机械抛光(CMP)方式,利用化学腐蚀和机械磨损协同作用,实现晶片表面的全局平坦化。
1)长晶
碳化硅晶体生长的主流方法是物理气相传输(PVT)。碳化硅单晶炉的长晶方式(晶体制备方法)主要包括物理气相传输(Physical Vapor Transport,PVT)、高温化学气相积淀(HTCVD)及液相外延(LPE)。由于设备简单,操作易控制,运行成本低等优点,物理气相传输(PVT)是最成熟的制备方法。国外厂商Wolfspeed、II-VI、SiCrystal,国内厂商天岳先进、天科合达、晶盛机电均选择PVT法制备碳化硅晶体。
PVT碳化硅单晶炉的晶体生长过程。a.将高纯碳化硅粉料置于单晶炉内的石墨坩埚底部,并将碳化硅籽晶粘结在坩埚盖内部。b.通过电磁感应加热或电阻加热的方式令坩埚内的温度升高至2000℃以上,并在坩埚内形成轴向温度梯度,使籽晶处的温度略低于粉料处。c.碳化硅粉料分解成硅原子、SiC2分子以及Si2C分子等气相物质,在温度梯度的驱动下从高温区(粉料)向低温区(籽晶)输送,在籽晶的碳面上按照籽晶的晶型进行有规律的原子排列,使晶体逐渐增厚,进而生长成碳化硅晶锭。
工艺难点在于温度控制,热场材料仍依赖进口。碳化硅晶体生长需在2,000℃以上的高温环境中进行,高于传统硅片制备所需的温度要求,生长条件非常苛刻,且生长过程不可见。为保证晶体生长品质需要通过热场精确调控生长温度和压力。热场是PVT碳化硅单晶炉中最关键的部分,热场设计决定了温度控制的精度。热场分为保温材料和坩埚,PVT生产工艺中热场材料主要采用细结构石墨。保温材料主要采用石墨软毡、硬毡,纯度要求<5ppm。坩埚主要采用高纯度石墨,纯度要求<5ppm。热场的加热方式分为感应加热法和电阻加热法。感应加热法是生长SiC晶体的主流工艺,电阻加热法是未来生长8英寸及以上大尺寸SiC晶体的主流工艺。目前热场主要的材料仍依赖进口(欧洲斯柯达、日本东洋碳素等)。保温材料和坩埚的更换周期分别为3~4个月和1~2个月,价格分别为3~4万和0.8~1万。
碳化硅生长速度缓慢,良率与国外龙头存在较大差距。碳化硅晶体结构类型众多,但仅少数几种晶体结构的碳化硅为衬底所需材料,杂质控制难度高。在晶体生长过程中,需精确控制硅碳比、生长温度梯度、晶体生长速度以及气流气压等参数,否则容易产生多晶型夹杂,降低产品良率。目前主流的使用PVT法约7天才能生长2cm左右厚度的碳化硅晶锭,碳化硅单晶与传统硅材的生长速度相差近800倍。并且随着碳化硅晶体尺寸扩大,生长工艺难度呈指数级增长。与硅基材料相比,碳化硅衬底工艺难度高,制备效率低,截至2023年7月,国内碳化硅衬底环节的综合良率仅在37%左右,与Wolfspeed等海外龙头85%的良率差距较大。
国内龙头碳化硅单晶炉CR2约80%,设备基本实现国产化。国内碳化硅单晶炉厂商包括晶升股份、北方华创等专业晶体生长设备供应商,以及采用自研/自产设备供应模式的碳化硅衬底材料厂商,基本实现了设备国产化率。
1)晶体生长设备供应商CR2约80%:北方华创、晶升股份碳化硅单晶炉分别占国内市场50%+、28%,CR2约80%,基本实现设备的国产化。其中北方华创2018年切入市场,2022年预计出货超500台,累计出货约千余台,晶升股份2015年切入市场,2022年预计出货200~240台,累计出货约500台。其他的二三梯队厂商,如恒普真空科技已实现小批量交付,连城数控、科友半导体等处于样机开发及验证阶段。
2)碳化硅衬底材料厂商自研/自产:天科合达、晶盛机电、露笑科技、河北同光、山西烁科等碳化硅厂商自研/自产晶体生长设备,主要用于其自身碳化硅衬底的生产制造,不对外大批量销售。
设备规格与国外齐平,部分晶体生长控制参数优于国外。碳化硅单晶炉技术指标主要包括设备规格参数、晶体生长控制参数。其中北方华创和晶升股份的设备规格参数与国外齐平,晶体生长控制参数中的控温精度(°C)以及极限真空(mbar)明显优于国外主流厂商。
北方华创及晶升股份为国内技术领先的碳化硅单晶炉主流厂商,设备规格、晶体生长控制指标基本处于同一技术水平,具有先进性,其产品在国内均应用于下游主流碳化硅厂商,具有较强的竞争优势。
2)切片
SiC衬底加工精度直接影响器件性能,要求SiC晶片表面超光滑、无缺陷、无损伤。SiC单晶的加工过程主要分为切片、研磨和抛光,其中切割是SiC衬底加工的第一道工序,对后续衬底外延以及晶圆制造至关重要。由于SiC的硬度仅次于金刚石,属于高硬脆材料,切割难度大。切片容易在晶片表面和亚表面产生裂纹损伤,影响后道工艺的开展,因此对WARP(翘曲)、BOW(弯曲)、TTV(总厚度偏差)等精度控制要求很高。
线锯切割是主流技术。切割技术主要包括传统锯切、线锯切割、激光切割、冷分离和电火花切片等,其中传统锯切(如内圆锯片、金刚石带锯)切缝大、材料损耗多,不适用于SiC晶体切割;激光切割通过激光在晶体内部形成改性层,从碳化硅晶体上剥离出晶片,断面质量好、切割效率高,产品处于下游验证阶段;冷分离将激光聚焦在材料内部形成改质层,通过冷冻胶使材料收缩从而分离晶片,几乎无材料损耗且加工效率高,但存在光束能量均匀性问题;线锯切割技术成熟,出片率较高,速度较快,成本便宜,是主流切割技术。
未来金刚线切割和激光切割有望替代砂浆线成为主流技术。线锯切割以钢线作为刃具,采用机械的方式进行切割,其中砂浆切割是普遍采用的方式;近年来,金刚线切割技术因其加工效率高、线耗成本低和环境友好等优势受到业界的广泛关注,此外,激光切割方法也形成了比较成熟的研究体系并逐渐兴起。
金刚线切割效率高、污染少,正逐渐代替砂浆切割。20世纪90年代中期,游离磨料砂浆切割取代传统锯切工艺,并随着光伏行业兴起而爆发,逐渐广泛应用于半导体行业。游离磨料砂浆切割利用线锯快速运动,将砂浆中的磨料颗粒带入锯缝达到“滚动-压痕”机制以去除材料,实现了多片同时切割,产率高且耗损率低,已广泛用于单晶和多晶硅切割,缺点是存在切割速度低、精度差、晶片厚度不均匀、砂浆回收难造成环境污染等问题。固结磨料金刚线切割通过电镀、树脂粘结、钎焊或机械镶嵌等方式将金刚石磨粒固结在切割线上,借助金刚线高速运动完成切割,根据金刚线运动方式不同可分为单向式、往复式和环形式,往复式切割单位长度有效利用度高、速度快,目前砂浆切割正逐渐被金刚线切割所替代。但金刚线在切割SiC这样的硬脆性材料时仍存在切割效率低、晶片表面损伤层深、线锯磨损快等缺点。
激光切割有望替代金刚线成为新一代主流切割技术。激光切割是通过激光处理,在晶体内部形成改性层从碳化硅晶体上剥离出晶片,属于非接触无材料损失加工,无机械应力损伤,加工方式灵活,不存在刀具损耗和水污染,设备使用维护成本低。理论上,激光波长越短、脉宽越短,加工热效应越小,有利于微细精密加工,但成本相对较高。
激光切割区域易受热损坏,且在切割口容易产生大量的残渣堆积。短波长激光加工热效应小,但未完全气化的熔渣在切割道内粘连堆积,使得切割断面不光滑,附着的熔渣在后续工艺环节容易脱落,影响器件性能。长波长激光器采用较大的功率,划切效率高,材料去除充分,断面均匀一致,但加工热效应太大,芯片设计中需要预留更宽的划切道。
过去激光工艺无法达到切片要求,激光半划用于SiC晶圆划线工艺。激光半划适用于解理性较好的材料加工,激光划切至一定深度,然后采用裂片方式,沿切割道产生纵向延伸的应力使芯片分离。这种加工方式效率高,无需贴膜去膜工序,加工成本低。但碳化硅晶圆的解理性差,不易裂片,裂开的一面容易崩边,划过的部分仍然存在熔渣粘连现象。
随着激光切割技术逐步应用于SiC领域,材料损耗小、加工时间短、产出良率高等综合优势明显。激光切割技术成熟后有望成为替代金刚线切片的主流SiC衬底切割技术。
a.激光切片的损耗较少。以20mm晶锭为例,在考虑良率、晶锭材质均匀的情况下,金刚线切割大概22片,激光切割大概30片。金刚线通过震荡的方式来切割晶锭,切割后边缘较为粗糙,后续需要进行研磨抛,带来较多损耗;激光切割的切面较为光滑,研磨抛带来的损耗非常少。一片SiC晶圆大约几千元,对于客户的原材料节省非常可观。
b.激光切片效率远高于金刚线。金刚线是多线程切割,平均一个晶锭需要几天时间。激光切片效率非常高,大约20分钟切一片,大概8小时切完一个晶锭,切割效率提升显著。
c.激光切片设备综合成本具有一定竞争优势。由于SiC激光切片设备能给客户带来效率和良率较大提升、材料较大节省,市场单价约为500-1000万元/台。金刚线切片单价200-300万元/台,后续加上各种耗材费用,激光切片设备的价格具有一定竞争优势。
SiC晶体砂浆切割设备厂家的主要代表为日本高鸟(Takatori)以及欧系的梅耶伯格(Meyer Buger)。日本高鸟的多线切割机是行业内最成熟的也是市场占有率最大的品牌,其蓝宝石多线切片机是国际上起步最早、市占率最高的机台,公司的SiC切割将充分受益于在蓝宝石领域的丰富经验。高鸟的SiC砂浆切片机型号包括MWS-34SN、610SD等,可覆盖对3-8英寸SiC的切片,最高线速可达700m/min(812SD和612SD型号)。国内主要设备厂家包括中国电子科技集团公司第四十五研究所、唐山晶玉和湖南宇晶等。国产设备在切割效率、加工精度、可靠性和工艺成套性等方面与国外设备仍有一定差距。
因对衬底的需求增大,国际上自20年开始推行金刚线切割。目前日本安永已有成熟的SiC金刚线切割设备,其中HW-810机型可满足6-8英寸SiC、GaN等多种高硬度材料的线切加工需求。
国外激光切割工艺主要设备供应商DISCO。DISCO深耕切、磨、抛,牢牢掌握龙头地位。DISCO研发出的KABRA技术,适用激光针对SiC晶锭切片,显著提升加工效率,单片6寸SiC晶圆的切割时间由3.1小时大幅缩短至10分钟,且不再需要后续研磨,单位材料损耗降低56%。
国内激光切割工艺主要设备供应商为大族激光、德龙激光。大族激光作为国内激光厂商龙头,SiC晶锭激光切片机已交付验证。德龙激光专注于高端激光设备和精细微加工,是国内唯二SiC切片设备供应厂商。大族激光为德龙激光唯一竞争对手,市占份额各占约50%。由于半导体加工高要求壁垒限制普通激光厂商参与晶圆段工艺,短期内暂无其他明显竞争对手。
3)研磨抛光清洗
切割片存在损伤层,需要通过磨削、研磨、抛光和清洗环节提高表面质量和精度。切割片通常采用砂轮磨削和研磨相结合来去除刀痕及表面损伤层,超声振动辅助磨削和在线电解修整辅助磨削可以提高磨削质量。研磨分为粗磨和精磨,粗磨使用粒径较大磨粒,可有效去除刀痕和变质层;精磨使用粒径较小磨粒,可改善表面光洁度和平整度。抛光进一步消除表面划痕、降低粗糙度和消除加工应力,化学机械抛光工艺(CMP)是实现SiC单晶片全局平坦化最有效的方法,是实现加工表面超光滑、无缺陷损伤的关键工艺。抛光后需借助X射线衍射仪、原子力显微镜、表面平整度检测仪、表面缺陷综合测试仪等设备检测各项参数指标来判定晶片等级。随后需在百级超净间内,使用清洗药剂和纯水清洗,去除微尘、金属离子、残留抛光液等沾污物,再借助超高纯氮气和甩干机吹干、甩干,并封装在洁净片盒内。
SiC行业中所使用的磨抛设备均由蓝宝石、硅晶等行业中的单一设备所改造延伸而来,因此厂商众多。国外厂商包括日本的秀和工业、Disco和东京精密,法国的Soitec,瑞士的梅耶博格,美国的Applied Materials和Speedfam等;国内厂商包括迈为、特思迪、扬帆半导体等。为满足产业化需求,切磨抛的全自动量产化正在逐步开展。
2、外延
外延工艺必不可少。与传统硅器件不同,碳化硅器件不能直接制作在衬底上,需要在衬底上生长一层晶相同、质量更高的单晶薄膜(外延层)。外延可分为1)同质外延:在导电型SiC衬底生长SiC,常用于低功率器件/射频器件/光电器件;2)异质外延:在半绝缘Sic衬底生长GaN,常用于高功率器件。
外延晶体更优质可控,层厚越大,耐压越高。碳化硅晶体生长的过程中会不可避免地产生缺陷、引入杂质,导致质量和性能不足,而外延层的生长可以消除衬底中的某些缺陷,使晶格排列整齐。外延厚度越大(难度越大),能承受的电压越高,一般100V电压需要1μm厚度外延,600V需要6μm,1200-1700V需要10-15μm,15000V则需要上百微米(约150μm)。
SiC外延需严格控制缺陷,工艺难度大。SiC外延会复制衬底的晶体结构,因此外延层缺陷包括来自衬底的缺陷(如微管、贯穿螺型位错TSD、贯穿刃型位错TED、基平面位错BPD),以及生长过程的位错以及宏观缺陷(如掉落物、三角形缺陷、胡萝卜缺陷/彗星型缺陷、浅坑、生长的堆垛层错)。
掉落物、三角形缺陷等属于致命性缺陷。衬底缺陷的TSD和TED基本不影响碳化硅器件性能,只有BPD会引发器件性能的退化。而生长过程的掉落物、三角形缺陷等是致命性缺陷,一旦出现,会导致器件测试失败(击穿电压VB降低20%~90%),良率大幅降低。
低缺陷、厚外延是主要趋势。随着器件耐压等级的提高,外延厚度从过去几微米发展到几十甚至上百微米。Wolfspeed(Cree)的N/P型碳化硅外延厚度均可达到200μm,国内存在一定差距,瀚天天成N型碳化硅外延厚度达40μm,东莞天域N型碳化硅外延厚度做到30μm。
(1)外延片制作方法
1)CVD成本适中、质量好、生长速度快,是主流外延技术
CVD是主流外延技术。外延是一种常用的单晶薄膜制备技术,和Si器件工艺有所区别,几乎所有的SiC电力电子器件工艺均在4H-SiC同质外延层上实现,衬底只是起到支撑和导电的作用。现阶段SiC薄膜外延的方法主要包括:化学气相淀积(CVD)、分子束外延(MBE)、液相外延法(LPE)、脉冲激光淀积和升华法(PLD)等。目前化学气相沉积(CVD)是最为普及的4H-SiC外延方法。其优势在于生长过程中气体源流量、反应室温度以及压力均可以有效控制,大幅降低了外延过程中的随机因素,工艺稳定性好;外延过程中通过调整各种气体的流量可以精准控制外延层的厚度、掺杂浓度以及掺杂类型,工艺可控性强,同时CVD还兼备成本适中+外延质量好+生长速度快的优势。
其中CVD工艺流程:1)利用载气(H2)将反应源气体(如SiH4/C3H8)输送到生长室内的热区;2)气体达到被加热的SiC衬底,反应沉积单晶薄膜(外延片)。目前常用SiH4、CH4、C2H4作为反应前驱气体,N2和TMA作为杂质源,使用4°斜切的4H-SiC衬底在1500-1650℃下生长外延。
MOCVD是新型CVD,沉积温度更低,沉积层多样。MOCVD反应源是金属有机化合物,传统CVD是无机化合物,一般有机物熔点比无机物低,且种类远大于无机物。因此MOCVD沉积温度(500-1200℃)显著低于传统CVD(900-2000℃),且能在不同衬底上沉积超薄层甚至原子层的特殊结构表面。
2)水平/垂直式多技术并行,多腔、多片有效提高产能
CVD分为冷壁和热壁,热壁是主流。冷壁的壁温基片温度,在反应室外对器壁+原料区+基片加热。冷壁CVD结构简单,但热辐射损失大,导致加热效率很低,且温场/流场不均匀,晶体表面温度梯度很大(>100K/mm),容易翘曲;热壁CVD克服了这些缺点,改变加热方式、增加绝热材料(如石墨),温场/流场更均匀,温度梯度显著降低(<10K/mm),外延质量好,是量产CVD的主流。
SiC-CVD按照气流方向可分为垂直/水平式。水平式难度较低,是新进入者首选。水平式/行星式CVD技术难度、成本相对较低,是新进入者的首选,但水平式气体迁移路径长,膜厚和掺杂浓度不稳定,同时气体入口距衬底近,流场和温场不均匀,容易形成SiC颗粒掉落,造成缺陷;垂直式的气体入口距衬底较远,流场和温场更均匀,不易生成SiC颗粒,但技术难度大、设备昂贵,使用垂直式的主要是Nuflare。
SiC-CVD按照技术路线可分为单机单腔/单机多腔,单腔单片/单腔多片:
单机多腔VS单机单腔。单腔室中的多步工艺可以转变为多腔室中的单步工艺,这种设计有利于简化腔室内的设计,提升工艺的效率和重复性。当某个腔室发生故障时,可以单独维修,而不影响其他腔室的工艺,提高设备稼动率与整线的产出,但双腔室技术难度远高于单腔室。Nuflare的双腔*单片6寸产能约1500-1800片/月(全自动),而原先的单腔*单片产能约600片/月,产能实现翻番。
单腔单片VS单腔多片。单腔多片通过片数的增加提高单位时间产能,但单腔多片的难点在于控制多片外延的厚度均一性、掺杂均一性。例如国外爱思强曾采用单腔8片式,产能600-1200片/月,但气体浓度控制难度大,外延不均匀且缺陷比较多,不受市场认可。国内晶盛机电成功推出了6寸单腔双片式,产能达到600-650片/月,比单腔单片产能增加70%,单片运营成本降幅可达30%以上。
3)外延设备基本被海外企业垄断,国内企业具备替代空间
国内外延设备由国外厂商主导,主要由意大利LPE公司、德国Aixtron公司、日本Nuflare公司垄断,占据全球87%左右市场空间。
(2)外延产能布局
国外双寡头垄断全球市场,CR2超90%。2020年Wolfspeed与昭和电工分别占据全球碳化硅导电型外延片市场52%和43%的市场份额,合计高达95%,形成双寡头垄断。由于进口外延炉供货短缺+国内外延炉仍需验证+外延工艺难度大,国内SiC外延厂商较少,市占率较低。
瀚天天成和东莞天域国内CR2超80%。
1)技术方面:6寸外延均较为成熟和稳定,8寸均有储备,其中瀚天天成已实现8寸外延技术的突破,且具有量产能力;东莞天域正攻克关键技术,预计2025年首条8寸外延产线投产。
2)产能方面:瀚天天成2022年6寸产能达12万片,2023年计划产能40万片(包括6/8寸),至2025年产能目标约140万片;东莞天域2022年6寸产能达8万片,并且启动年产100万片的6/8寸外延项目,预计2025年竣工并投产。
(3)外延成本与价格
外延片的成本结构,原材料成本占比是52%,设备折旧成本是15%,剩下的劳动力、洁净室和研发成本的占比分别是14%、12%和7%。
伴随衬底价格降低,未来外延价格有下降趋势。基于SiC衬底,外延环节普遍采用化学气相沉积技术(CVD)获得高质量外延层,随后在外延层上进行功率器件的制造。伴随SiC衬底价格的降低,预计未来外延价格也将呈现下降趋势,据CASA,2020年SiC外延片价格约为128元/平方厘米,预计到2025年,价格将会出现明显下降,至2045年SiC外延片价格将降至71元/平方厘米。
3、划片
(1)激光开槽有效降低SiC晶圆机械划切崩边带来的不良影响
在外延完成后,SiC需要激光划片进行晶圆的切割再制作器件。SiC晶圆硬度高、脆性大、韧性低,传统晶圆机械切割容易造成较多缺陷。传统机械切割(砂轮)方法是最常见的晶圆划片方法,刀片可根据产品选择。而SiC晶圆莫氏硬度分布在9.2-9.6,高硬度、高脆性、低断裂韧性使得其磨削加工过程中易引起材料的脆性断裂,切割槽的背面容易出现崩刃,裂纹,崩边大,层状剥离等缺陷。严重影响良品率,降低了产能效益,增加生产成本。
通过激光开槽工艺,先行在切划道内开2条细槽,再采用机械刀片划片,有效减小崩边等因素带来的缺陷。日本DISCO针对SiC晶圆难以使用普通金刚石刀片进行划切加工的问题,开发了一种激光开槽加工工艺。先在切割道内切开2条细槽(开槽),然后再使用磨轮刀片在2条细槽的中间区域实施全切割加工。通过采用该项加工工艺,能够提高生产效率,减少甚至解决因崩裂、分层(薄膜剥离)等不良因素造成的加工质量问题。
(2)隐形激光切割技术为高硬脆SiC晶圆提供成熟解决方案
激光划片有效解决砂轮划片崩刃、刀具磨损等问题,但是热效应和熔渣仍是不可忽视的问题。激光划片是指将激光能量于极短的时间内集中在微小区域,使固体升华、蒸发的全切割加工,开槽加工方式,属于激光烧蚀加工技术。激光划片属于非接触式加工,加工效率跟晶圆厚度有密切关系,厚度越厚,划片速度越慢,吞吐量就越低。
采用隐形激光切割技术,有效减小切割道损耗,是主流的激光划片技术路线。激光隐形切割通过将脉冲激光的单个脉冲通过光学整形,让其透过材料表面在材料内部聚焦,在焦点区域能量密度较高,形成多光子吸收非线性吸收效应,使得材料改性形成裂纹。每一个激光脉冲等距作用,形成等距的损伤即可在材料内部形成一个改质层。在改质层位置材料的分子键被破坏,材料的连接变的脆弱而易于分开。切割完成后通过拉伸承载膜的方式,将产品充分分开,并使得芯片与芯片之间产生间隙。
4、器件制造
(1)碳化硅器件设计
SiC二极管商业化逐步完善,SiC MOS仍存众多难点。目前国内多家厂商已设计出SiC SBD产品,中高压SiC SBD产品稳定性较好,在车载OBC中,多采用SiC SBD+SI IGBT实现稳定的电流密度。目前国内在SiC SBD产品上在专利设计方面没有障碍,派恩杰已经开始六代SiC SBD的研发,与国外差距较小。
SiC MOS仍与海外厂商存在差距,相关制造平台仍在搭建中。目前ST、英飞凌、Rohm等600-1700V SiC MOS已实现量产并和多制造业达成签单出货,而国内目前SiC MOS设计已基本完成,多家设计厂商正与晶圆厂流片阶段,后期客户验证仍需部分时间,因此距离大规模商业化仍有较长时间。
目前平面型结构为主流选择,未来沟槽型在高压领域应用广泛。平面结构SiCMOS厂商众多,平面结构相比沟槽不容易产生局部击穿问题,影响工作稳定性,在1200V以下市场具备广泛应用价值,并且平面结构在制造端相对简单,满足可制造性和成本可控两方面。沟槽型器件寄生电感极低,开关速度快,损耗低,器件性能相对高效。
目前选择平面MOSFET结构厂商有Wolfspeed、意法半导体、Microsemi,国内厂商包括斯达半导、新洁能、APS、瞻芯、瀚芯等Fabless厂商。
目前市场中,能够量产沟槽型SiC MOSFET的企业为罗姆的双沟槽节、英飞凌的半包沟槽和日本住友的接地双掩埋结构。目前国内市场,时代电气子公司时代半导体宣布投资4.62亿元扩产6英寸沟槽型SiC芯片。
对于沟槽型碳化硅器件来说,未来的技术演进方向是减小沟槽底部氧化层工作电场强度,避免专利侵权(英飞凌、意法、罗姆均有相关专利)和可控的制造成本。
(2)碳化硅器件制造
SiC器件制造的工艺环节与硅基器件基本类似,包括涂胶、显影、光刻、减薄、退火、掺杂、刻蚀、氧化、清洗等前道工艺。但由于碳化硅材料特性的不同,厂商在晶圆制造过程中需要特定的设备以及开发特定的工艺,无法与过去的硅制程设备、工艺完全通用,因此当前SiC晶圆制造产能紧缺。SiC晶圆制造特定工艺与Si工艺的一些差异点主要在于:
1)光刻对准:由于SiC晶圆是透明的,因此CD-SEM和计量测量变得复杂,光刻对准、设备传送取片等难度较大。
2)蚀刻工艺:由于SiC在化学溶剂中呈现惰性,因此同光使用干法蚀刻。则掩膜材料、掩膜蚀刻的选择、混合气体、侧壁斜率的控制、蚀刻速率、侧壁粗糙度等都需要重新开发。3)高温大剂量高能离子注入工艺:由于SiC器件的特性,SiC扩散温度远高于硅,传统的热扩散在碳化硅中并不实用,掺杂时只能采用高温离子注入的方式。4)超高温退火工艺:高温离子注入会破坏材料本身的晶格结构,因此需要在惰性气体中高温退火来恢复结构,通常退火温度高达1600-1700度,使SiC表面再结晶并电激活掺杂剂。
5)高质量栅极氧化层生长:较差的SiC/氧化硅界面质量会降低MOSFET反转层的迁移率,导致阈值电压不稳定,因此需要开发钝化技术,以提高SiC/氧化硅界面质量。
SiC晶圆制造特定工艺带来特定设备的需求,主要包括高温离子注入机、高温退火炉、SiC减薄设备、背面金属沉积设备、背面激光退火设备、SiC衬底和外延片表面缺陷检测和计量。其中,是否具备高温离子注入机是衡量碳化硅产线的重要标准之一。
(3)碳化硅器件封测
陶瓷基板按照工艺主要分为DBC、AMB、DPC、HTCC、LTCC等基板,国内常用陶瓷基板材料主要为氧化铝、氮化铝和氮化硅,其中氧化铝陶瓷基板最常用,主要采用DBC工艺;氮化铝陶瓷基板导热率较高,主要采用DBC和AMB工艺;氮化硅可靠性较为优秀,主要采用AMB工艺。AMB工艺生产的陶瓷衬板主要运用在功率半导体模块上作为硅基、碳化基功率芯片的基底。
DBC衬板应用场景受限,AMB衬板性能优势明显。由于AMB氮化硅基板有较高热导率(>90W/mK),可将非常厚的铜金属(厚度可达0.8mm)焊接到相对薄的氮化硅陶瓷上,载流能力较高;且氮化硅陶瓷基板的热膨胀系数与第3代半导体衬底SiC晶体接近,使其能够与SiC晶体材料匹配更稳定,因此成为SiC半导体导热基板材料首选,特别在800V以上高端新能源汽车中应用中不可或缺。另外,目前以硅基材料为主的IGBT模块在具有高导热性、高可靠性、高功率等要求的轨道交通、工业级、车规级领域正逐渐采用AMB陶瓷衬板替代原有的DBC陶瓷衬板。
5、总结
在高电压、大功率的电力系统升级的大背景下,碳化硅器件逐步替代部分硅基功率器件是较为明确的趋势,关键痛点在于供应稳定性和价格,这需要整个产业链从衬底、外延、器件到模块封装各个环节实现良率提升、产能扩大、产线稳定等的优化和改进。从当前产业状况而言,需求远大于产业链供给能力,对于上下游的合作需求更为迫切。从海内外核心玩家的布局情况和订单情况来看,具备(1)稳定衬底供应来源(2)较强器件设计与制造能力(3)较强资金能力,等三个条件的企业更容易获得客户的信任和青睐,因此全产业链整合、原材料+IDM等模式的企业具备优势。
06
未来展望
1、预计SiC器件在高电压场景中先具备替代优势
从安森美的功率器件原厂价格对比来看,目前其650V SiC MOSFET价格比同电压的硅基IGBT单管要贵3.2倍,而1200V SiC MOSFET比同电压的IGBT单管价格差距就缩小至2.2倍。这反映在高电压等级下,SiC器件的价格与硅基的差距更小。预计在高电压场景下,SiC已出现替换硅基器件的优势。华为预计2025年前SiC价格逐渐于硅持平。华为在《数字能源2030》中指出,以SiC为代表的第三代半导体功率芯片和器件能够大幅提升各类电力电子设备的能量密度,提高电能转换效率,降低损耗,渗透率将在未来全面提升;SiC的瓶颈当前主要在于衬底成本高,预计未来2025年前,其价格会逐渐降为硅持平。
-
半导体
+关注
关注
328文章
24506浏览量
202122 -
检测
+关注
关注
5文章
4083浏览量
90745 -
SiC
+关注
关注
27文章
2435浏览量
61404 -
碳化硅
+关注
关注
24文章
2432浏览量
47532
发布评论请先 登录
相关推荐
SIC 碳化硅认识
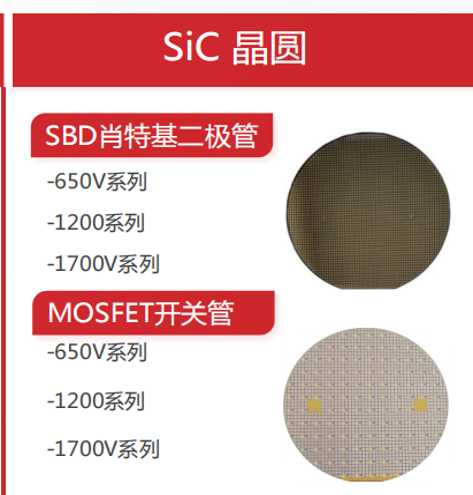
深圳市萨科微半导体有限公司,技术骨干来自清华大学和韩国延世大学...
并购、扩产、合作——盘点2023年全球第三代半导体行业十大事件
推动SiCMOSFET国产化,华秋-电子发烧友获“芯塔电子”优秀媒体合作伙伴奖
推动SiCMOSFET国产化,华秋获“芯塔电子”优秀媒体合作伙伴奖
2023年第三代半导体融资超62起,碳化硅器件及材料成投资焦点
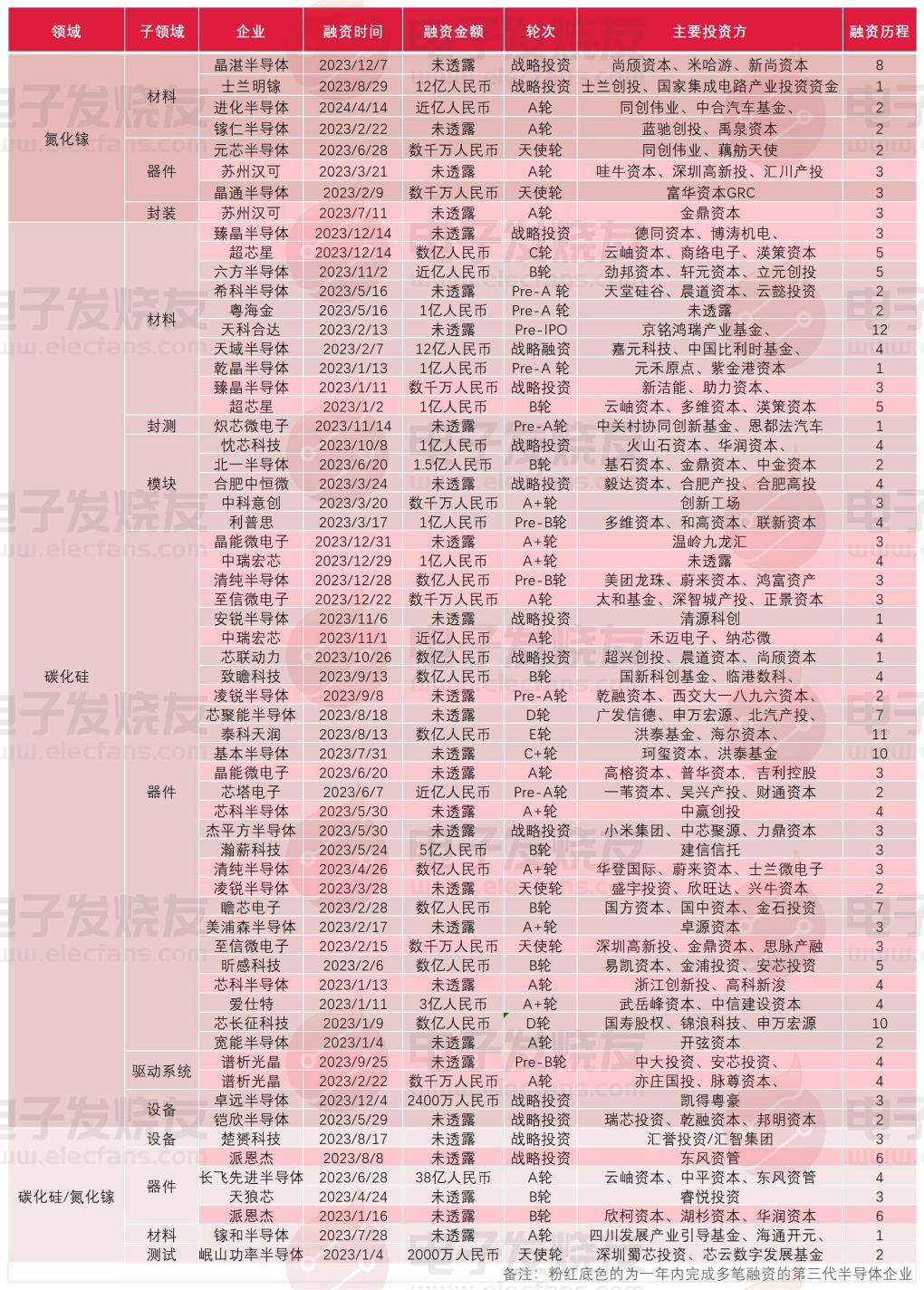
第三代半导体之碳化硅行业分析报告
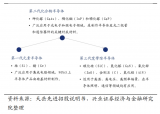
第三代宽禁带半导体碳化硅功率器件的应用
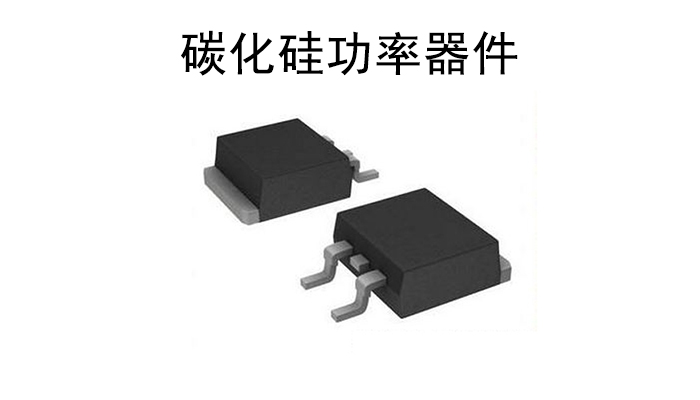
第三代半导体功率器件在汽车行业的应用
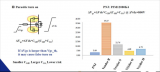
什么是第三代半导体技术 碳化硅的产业结构分析
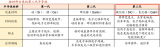
评论