【摘要】福世蓝修复技术是利用高分子金属修复材料,现场解决辊压机减速机空心轴及辊轴传动部位磨损,其最大优势就是现场修复,修复效率高,投入人力物力少,修复后设备使用寿命甚至超过新部件。
【关键词】辊压机轴磨损、行星齿轮减速机、减速机空心轴磨损修复、在线修复
辊压机减速机轴磨损现象的原因
1、由于胀紧套部位承受较大的扭矩,长期运转使用中轴与轴套配合面发生相对运动,因而造成轴套与轴头之间的磨损,胀紧套无法锁紧,造成停机;
2、设备在正常检修过程中,企业人员忽视了对胀紧套上预紧螺栓的紧固,长时间的设备运行造成螺栓断裂,使轴与轴套产生相对运动,造成轴与轴套之间的磨损;
3、一些老设备上的减速机会经常拆卸外出加工修复,部分拆卸工艺不科学,比如有些单位为了拆卸方便会在空心轴上面直接焊接工装,出现热应力不均匀导致轴套变形,拆卸后再次安装会出现预紧力不足,导致出现问题。
减速机空心轴磨损的现场修复
针对于空心轴的磨损,修复方案有以下几类:
1、电刷镀工艺
优点是可以实现在线修复,缺点是电刷镀工艺的刷镀涂层受到磨损量的限制,一般电刷镀涂层刷镀厚度小于0.2mm。当磨损量大于0.2mm时,其刷镀效率将成倍下降,且刷镀层过厚时,使用过程中刷镀层容易脱落,使用寿命短。
2、整体拆卸,然后补焊机加工修复
补焊机加工修复工艺是传统修复工艺中最常见的一种方式,其特点是修复精度高,缺点是对于小型轴类的修复过程中容易造成应力集中造成轴的弯曲变形,对于辊压机等大型轴类的修复无法进行在线修复,拆卸和运输将大大增加修复成本和修复周期。对于机加工设备的要求较高,综合性价比低,增加企业维修维护成本。同时补焊工艺无法避免热应力的问题,会造成轴使用过程中出现裂纹甚至断裂的危险,增加生产安全隐患。
3、更换新设备
对于空心轴部位的磨损,采用更换部件的方式不仅成本高,而且供货周期及拆卸运输成本高,不到万不得已企业一般不予采纳。
4、福世蓝高分子材料在线修复
福世蓝®在线修复技术是利用高分子复合材料既具有金属所要求的强度和硬度,又具有金属所不具备的退让性(变量关系),实现在线修复辊压机等大型轴孔以及轴类的磨损。修复过程中借助复合材料本身所具有的抗压、抗弯曲、延展率等综合优势,可以有效地吸收外力的冲击,极大化解和抵消轴与轴套径向冲击力,避免了间隙出现的可能性,也就避免了设备因间隙增大而造成相对运动的磨损,所以非常适合这种轴与轴套的静配合方式的修复。福世蓝高分子修复材料不是靠“硬度”来解决设备磨损的,而是靠改变力的关系来满足设备的运行要求。
福世蓝在线修复施工过程
1、用量具测量磨损的轴与套的磨损量,如果单边磨损量在0.4mm之内可以采用打麻点修复工艺,如果有完好基准面可以涂抹材料直接装配工艺;
2、用磨光机将修复的轴表面打磨粗糙;
3、在修复轴表面敲打密密麻麻的麻点(磨损量<0.4mm),起支撑及进一步找中作用;
4、空心轴套对称开槽,起进一步加强预紧作用(如果有开槽可以省略);
5、空试空心轴套,判断敲打麻点的高度是否合适;
6、空心轴套用无水乙醇擦拭干净后,内表面涂抹803脱模剂,至少晾晒5-10分钟,起到未来拆卸方便的作用;
7、修复的轴表面也要用无水乙醇擦拭干净,确保表面无油污及灰尘;
8、按照2:1比例调和福世蓝®高分子材料2211F涂抹在修复修复轴上,以及晾晒好后的空心轴套上,涂抹时第一层一定用力涂抹保证与基体的粘接,涂抹厚度要大于修复尺寸;
9、开槽的空心轴记得插入2张硬纸壳或是空出一段距离不涂抹材料,以防挤出的多余材料从开槽溢出;
10、装配空心轴套,夏天情况下尽可能1个小时装配到位,确保材料未固化前,具有流动性之前装配到位;
11、碘钨灯加热固化6小时(24℃下自然状态固化24小时);
12、抽调纸壳检查是否有多余材料及杂物,如若有清理其异物;
13、按照规定要求装配胀紧套;
14、打表找水平度,确保安装到位;
15、材料固化后再次预紧螺栓;
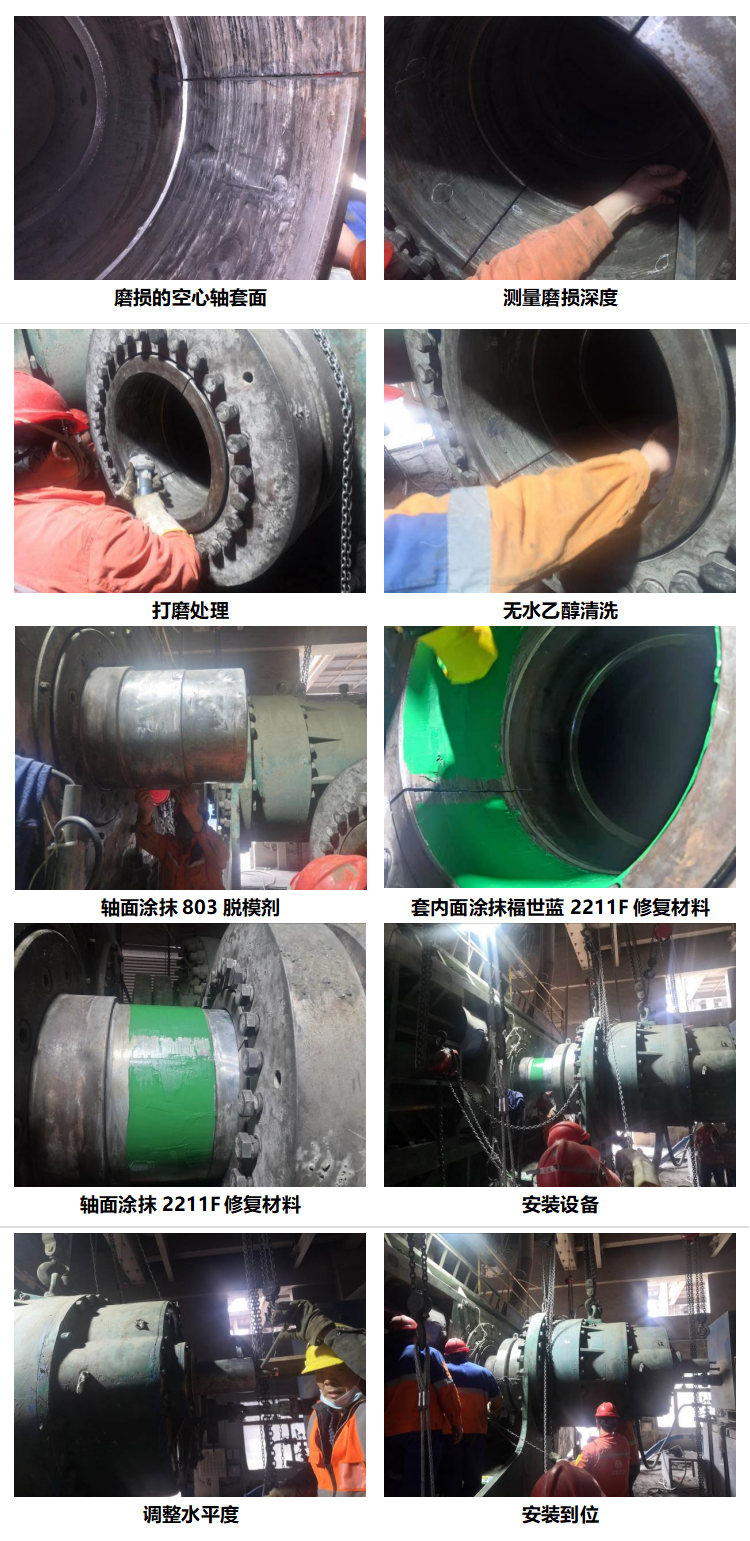
辊压机是水泥生产中重要环节,传统的堆焊修复,以及外协机加工修复,制约了企业宝贵的开机时间,而且修复质量参差不齐。福世蓝在线修复工艺修复周期快、修复效率高,且可以在线修复,减轻了企业设备管理人员及检修人员的劳动量,更重要的是给企业节省了费用及争取了更多的开机时间。
发布评论请先 登录
相关推荐
aduc834可以下载程序,但是程序都无法运行是什么原因造成的,如何解决?
AD7173工作几个小时就损坏是什么原因造成的?
电机哆嗦是什么原因 电机振动是什么原因
造成辊压机轴磨损的主要原因
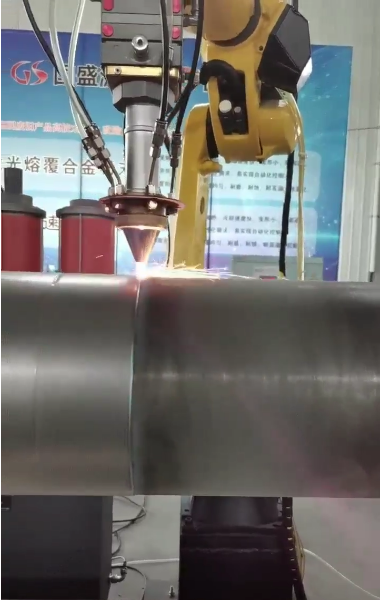
过滤机轴头磨损该用啥技术修复
如何进行球磨机空心轴磨损修复
免拆卸、快速维修辊压机空心轴轴颈磨损,让维修变得简单高效
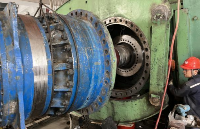
评论