研究背景
锂离子电池(LIBs)电池的应用激增,在可预见的未来电池寿命为8−10年后,最终将导致大量消耗。对这些废电池的处理不当可能会引起人们对安全和环境污染的严重担忧。此外,电动汽车市场的快速扩张需要越来越多的原材料和资源,如锂、钴、石墨、铜和铝,这也导致了材料短缺和价格上涨。因此,电池的回收对于减轻资源的限制和潜在的危害是至关重要的和必不可少的。除了这些最终使用寿命寿命外,电池电极碎片在电池制造过程中不断产生(~10%),这也不容忽视。
与废弃的锂电池不同,电极废料具有其独特的优势,如不需要拆卸电池、完整的活性材料和完全已知的化学成分,因此是一种价值更高的资产,需要高效回收利用。 目前,主要的回收方法包括商业上可获得的法法和湿法冶金方法和直接回收方法,主要是在实验室开发的方法。焦法冶金的重点是通过高温碳热还原(超过1400℃)回收高价值金属,其中钴、镍和铜作为合金收集,而石墨和其他材料通常以矿渣、燃料或还原剂的形式燃烧,并有严重的废气排放。在湿法冶金术中,废电池中有价值的金属被浸出并溶解到混合溶液中,然后通过复杂的化学过程沉淀并分离成纯金属盐。此外,从废过的LIB阳极中回收1公斤石墨的废水高达几吨,导致污染和危害增加。相比之下,直接回收的目的是收集活性材料,收集到的材料可以通过修复结构缺陷进行再生以供电池应用,或转化为其他高价值的功能材料。因此,直接回收是电池回收的一种理想途径,电池消耗少、耗时短,回收污染低、经济价值高的材料。
然而,在直接回收中,获得活性材料首先需要电极材料与集电器有效分离(即材料回收),这是由于强大的粘结剂和卷密致密电极而困难的。此外,回收材料的质量和以下所有处理(即材料再生)都强烈依赖于分离的有效性。粉碎电池或电极,然后进行筛分是一个成熟的材料回收过程;不幸的是,这种回收材料的收率总是很低,而且含有大量的金属杂质。7 wt%铜在石墨中。实验室开发了几种更好的分离方法,如管式炉退火、电化学分离、超声辅助酸洗涤、低温熔盐法等。它们通常获得含有较少杂质的可回收的活性物质。然而,由于效率、经济效益或可伸缩性有限,许多这些分离方法仍然不适合工业采用。
成果简介
近日,华中科技大学黄云辉教授&浙江大学陆俊教授在本文报告了通过冲击式加热(1500℃,1 s)或连续滚动加热(~ 5 m/min)对> 97%回收率和~100%完整金属箔的电池材料的瞬时回收,从而显示了极高的能量、时间和材料效率。此外,热模拟和原位质谱表明,电极的温度分布是空间均匀,粘结剂网络可以有效地分解为气体和非晶碳涂层。超短的煅烧时间对电池材料的影响最小,从而有利于简单和有效的再生。文章演示了来自不同公司的负极、各种正极的一般回收,特别是电池碎片,这些电池碎片可以在卷对卷设备中连续和自动地回收。与湿法冶金相比,EverBatt分析显示,瞬态电池回收显著降低能源和碳足迹(~50X减少),接近零废物产生,和更高的利润(甚至4.78$/公斤的负极),从而使其实用的直接回收电池材料具有杰出的效率、可持续性和可扩展性。
研究亮点
通过冲击式加热(1500℃,1 s)或连续滚动加热(~ 5 m/min)对> 97%回收率和~100%完整金属箔的电池材料的瞬时回收。
粘结剂网络可以有效地分解为气体和非晶碳涂层。超短的煅烧时间对电池材料的影响最小,从而有利于简单和有效的再生。
不同的负极、各种正极都可以进行回收,特别是电池碎片,这些电池碎片可以在卷对卷设备中连续和自动地回收。
瞬态电池回收显著降低能源和碳足迹(~50X减少),接近零废物产生,和更高的利润(甚至4.78$/公斤的负极),从而使其实用的直接回收电池材料具有杰出的效率、可持续性和可扩展性。
图文导读
在这里,文章报道了一种基于瞬态加热的干燥、可扩展和快速的直接循环利用废电极的方法,这可以通过冲击式加热(如1500℃,1 s)或连续滚筒加热(如1500℃,~5 m/min,图1a)来实现。以废旧负极为例,将电极片在高温下快速煅烧,以分解粘合剂(苯乙烯-丁二烯橡胶,SBR)。负极石墨颗粒可以很容易地与铜集电极分离,可以得到98.7%和~100%完整的Cu箔(图1b)。与湿法冶金方法相比,瞬态循环具有显著更高的能量和时间效率(减少50-900倍),并产生高纯度的材料(杂质减少10倍),以及最小的废物产生和碳足迹(图1c)。此外,瞬态回收方法一般适用于来自不同电池公司的各种负极、正极,特别是可以以滚动方式回收的电池废料,使其能够直接回收效率高、可扩展性和可持续性的电池材料。
图1.(a)通过翻转加热的铜箔瞬态回收示意图。(b)在分离前后的负极。(c)湿法冶金和瞬态回收方法中材料回收过程的能量输入和工艺时间,以及回收石墨中铜杂质的含量。
图2显示了石墨负极循环利用的冲击式加热过程。在整个过程中,使用碳化纸作为平台,通过电焦耳加热诱导高温冲击式加热。如图2a所示,温度曲线显示了一个尖峰状的加热过程,其中加热器的最高温度在一秒钟内接近1500℃。短时间加热方法的一个独特特点是促进粘合剂的快速分解和降解,同时避免可能的材料变质和元素扩散。用扫描电镜分析的方法研究了冲击型加热过程前后石墨的形貌。直接从废负极上刮取废石墨(SG)片,用于扫描电镜表征。如图2b所示,SG的表面很光滑,并涂有一层果冻层和颗粒,这应该是粘结剂和导电颗粒。
经过高温冲击式加热(1500℃,1 s)后,石墨层从铜收集器中剥离,我们得到的石墨颗粒(HTG)显示,颗粒之间没有果冻层连接,表明粘合剂的热解。为了研究瞬态加热过程中材料的物质演化,采用热解-气相色谱/质谱(Py-GC/MS)分析了SG的瞬态加热过程,具有相似的热解条件(加热速率为2000℃/s)。图2c中的总离子色谱显示了五种主要化合物:磷酰氟、异戊二烯、甲苯、苯乙烯和碳酸乙烯(EC)。磷化氟来自于LiPF6的热解。EC是电解质中的一种溶剂,在石墨颗粒表面被吸收。
其他三种物质(异戊二烯、甲苯和苯乙烯)是由含有苯环或烯烃键的SBR分解产生的。粘合剂的分解可以通过FT-IR测量来验证(图2d)。与废石墨(SG)在与有机官能团相关的400 ~ 2000 cm-1范围内包含多个吸附峰相比,这些峰在高温石墨(HTG)中消失,表明在快速处理过程中,尽管持续时间较短,但粘合剂完全分解。 瞬态加热的另一个优点是整个电极厚度的加热均匀性,这对于粘合剂的完全热解和所获得的材料的有效剥离非常重要。因此,我们进行了传热分析,并利用接近真实情况的参数模拟了热解过程中沿厚度方向的温度分布(图2e-g)。如图2e所示,电极的布局为夹心结构,石墨厚度为61 μm,铜箔厚度为10 μm,与我们的电极样品相同。
在加热器和电极之间设置了一个10 mm的间隙来模拟加热过程。热辐射、传导和自然对流都是考虑了从加热器到阳极电极的传热过程(详见实验部分)。图2f中所示的电极温度在整个电极材料中呈相当均匀的空间分布。在加热器瞬态加热到1500℃时,电极温度快速上升到最高温度1260℃,电极内的温度分布均匀(图2g)。温度分布的均匀性可以归因于铜和石墨的高导热系数,而薄电极的总厚度只有132 μm。
图2. 冲击式加热过程中的过程分析和结构演化。(a)冲击式加热的温度分布。(b)冲击型加热处理前后废石墨的(b)扫描电镜图像。(c)SG在Py-GC/MS中热解的总离子色谱,显示了粘合剂分解的成分。SG和HTG的(d) FTIR光谱。(e)热模拟模型的说明和模型的空间配置。(f)1s时的温度-距离曲线通过负极厚度的温度分布具有优越的均匀性。(g)在距离加热器不同距离下加热1500℃,1 s的模拟三维温度曲线。
经过冲击型加热后,我们得到了HTG粒子。虽然瞬态循环过程对HTG颗粒的影响最小,但这些颗粒仍然含有电解质和分解的粘合剂中的杂质,有些颗粒表面损坏,会降低其电化学性能。因此,需要适当的再生来恢复其结构和性能。再生过程如图3a所示,这是从天然石墨生产的电池级石墨中获得的。HTG首先在室温下用2M硫酸纯化1小时,以去除表面杂质。用纯水洗涤干燥后,纯化的石墨涂上聚丙烯腈(PAN),在1100℃的Ar气体中热解,得到具有无定形碳涂层的再生石墨(RG)。使用这些商业的工艺可以在很大程度上确保我们的HT石墨颗粒可以被视为石墨生产的原材料,作为一个可持续的石墨供应。
除了废负极外,电池制造过程中产生的负极废料也很容易通过瞬态回收收集。负极废料的优点是石墨颗粒完整,不需要再生。通过电感耦合等离子体分析来测定元素的含量和杂质(图3b)。在SG中,Cu最初是由电极集流器引入的,而锂应该来自电解质(LiPF6)或反应副产物(如SEI,其他死lithium)在长时间的充放电循环过程中,少量的铝和铁可能来自正极。经过冲击型加热后,HTG的杂质保持相似,这表明虽然使用了高温,但持续时间很短,原子的扩散在很大程度上仅限于产生进一步的杂质。
相比之下,通过湿法冶金的机械破碎(机械破碎G)获得的石墨中的Cu杂质高达72100 ppm,10个HTG的量(7122 ppm)。由于硫酸可以溶解大部分杂质,包括SEI层(无机化合物如LiF/Li2CO3)和元素金属颗粒,经过硫酸纯化后,Li、Cu、Fe和Al的杂质含量急剧下降到几个ppm。回收的废石墨(废G)即使没有净化,也很少有杂质,注意HTG中的锂含量很少,但也可以在再生之前回收。 SG、HTG、RG和Scrap G样品的x射线衍射(XRD)如图3c所示。它们都具有六方石墨的特征峰,如(002)、(100)、(101)、(004)和(110)(JCPDS no. 00-012-0212)。我们还测量了HTG的粒径分布,它在3 ~ 20 μm的范围内,与新的商业石墨(CG)相当,表明了类似的制造兼容性。这些特征表明,SG在长期循环后仍保持层状结构(体相),直到电池报废,冲击式加热没有引起相的变质或石墨尺寸的变化。
此外,我们还测量了SG和HTG的拉曼光谱。HTG的平均ID/IG比值为0.4,略大于SG的0.34,说明HTG的结构更为无序,可能来自于粘合剂分解产生的表面附着的非定形碳。进一步的透射电镜图像显示,经过冲击式加热后,石墨表面出现了~尺寸为100nm的小颗粒,在电子束辐照下不稳定,逐渐消失。因此,表面纳米颗粒要么应该是粘合物中的热解碳,要么应该是电解质中的无机产物(如LiPF6和五氟化磷)。以上结果表明,虽然SG和HTG的体层状结构保持良好,但由于表面缺陷,其石墨化程度有所降低(图3d)。
在高分辨率透射电子显微镜下观察了SG、HTG和RG的晶体结构。SG和HTG表面周围的(002)晶面的石墨层间距离分别为0.361和0.337 nm。SG在表面的层间距离越大,说明长时间循环后结构破坏越小,而HT石墨层间距离的减小意味着冲击型加热后石墨结晶度的提高。这种紧凑的层间结构被继承下来,并在RG(0.335 nm)中略有下降,表明石墨结构的再生和恢复。为了进一步验证回收和再生过程的有效性,我们对不同石墨样品的电化学性能进行了评估,包括SG、HTG、RG和ScrapG(图3e-g)。
此外,还以CG作为对照样品。由于去除杂质和通过表面涂层修复结构,在RG中恢复了电化学性能。图3e总结了不同样品的初始库仑效率(ICE),RG和Scrap G比SG有更高的ICE,由于SEI的形成,略低于CG的90%。图3f中也列出了1、50和100个循环的比容量,其中RG显示出与CG相当的容量,并表现出良好的循环稳定性(额外180个循环后>保留98%)(图3g)。此外,RG的速率性能(图S13b和c)和电化学阻抗谱与CG相当,优于SG。上述电化学性能表明,RG的性能与CG相当,因此,回收的HTG可直接用于再生后的电池生产,或作为电池级石墨生产的原料,以延长石墨的使用寿命。更重要的是,电池废料具有完整的材料,而且性能最高,不需要再生。
图3. 再生和电化学性能。(a)从废负极和负极废料中提取石墨颗粒的工艺流程。(b)机械破碎G、SG、HTG、RG和废料G中不同元素的含量SG、HTG、RG和废G的(c) XRD模式HTG和RG的(d) SEM图像。(e)初始库仑效率,以及(f)CG、SG、HTG、RG和废料G在不同循环数下的比容量。(g)CG、SG、HTG、RG和废料G的循环性能.
石墨的生产是高度能耗和耗时的,特别是石墨化过程(需要在2800℃加热几天)。考虑到对石墨负极的巨大需求(~180,000吨/年),负极回收可以成为石墨供应的一个好场所,并显著减少石墨生产中的碳足迹。然而,与正极材料回收的蓬勃发展相比,负极石墨的回收往往被忽视。由于石墨还没有像锂或钴那么昂贵,它对于通过传统的热法冶金或湿法冶金方法回收石墨是一个亏损的业务。因此,为了揭示能源、环境和经济影响,我们在能源消耗、废物排放、成本和潜在效益方面比较了废石墨的瞬态回收方法。 这些过程如图4a所示。
在火法冶金中,石墨燃烧有大量的二氧化碳排放,没有石墨回收,回收后只能获得合金和矿渣。另一方面,虽然湿法冶金可以获得石墨产品,但它有多种化学过程,涉及大量的废水。此外,铜箔多次浸入Cu2+离子或压成碎片,与铝和钢混合,这不仅需要大量的化学品和能源,而且需要进一步的能源和工艺来重新制造铜箔。在我们的瞬态回收中,活性材料和完整的金属箔可以通过瞬态加热(< 1s)获得,显示出显著更高的能量、时间和材料效率,同时也将废物转化为价值,大大减少碳足迹。
为了量化环境和经济优势,我们使用了阿贡国家实验室开发的EverBatt模型来评估我们的瞬时循环利用的整个循环流程,并将其与火法冶金和湿法冶金方法进行了比较。能源消耗由直接的能量输入和材料输入组成(图4b)。具体而言,瞬态循环工艺的能耗为2.48 MJ/kg电池(只有电能),远低于火法工艺(18.23 MJ/kg电池,材料7.72,能量10.51 MJ/kg电池)和湿法工艺(102.19 MJ/kg,材料17.45,能量84.74 MJ/kg电池)。此外,热法冶金和湿法冶金需要许多化学药剂,如盐酸、过氧化氢、氢氧化钠、氢氧化钠、石灰石、沙子、硫酸。相比之下,对于我们的瞬态回收方法,不需要添加额外的材料来辅助回收。
由固体、液体和气体废物组成的废物排放也出现了同样的趋势(图4c)。瞬态循环工艺的排放量最低(0.26 kg/kg电池),仅为热法冶金和湿法冶金的7.7%和1.8%。需要注意的是,在废气排放中,大多数(>95%)是二氧化碳排放,这表明瞬态循环过程的碳足迹要低得多。 文章还仔细比较了三种回收方法的成本和潜在利润(4d)。成本包括电池费用、电池拆卸、公用事业、材料、人工、其他直接成本、折旧和其他固定成本。湿法冶金回收成本最高,达到4.00 $/kg电池,高温法和瞬态循环过程的成本分别为2.63 $/kg电池和2.95 $/kg电池,其中大部分成本来自电池费用(2.0 $/kg电池)。
瞬态回收可以进一步节省成本,因为使用的材料和公用设施要少得多。基于成本分析和回收材料的价格,我们可以通过不同的方法评估电池回收的潜在利润(图4d),其中利润是通过材料收入减去成本计算的。瞬态回收的最高利润为15.55 $/kg电池,因为(1)它获得了所有有价值的材料,具有非常高的材料回收率(即更有价值的材料效益)和(2)回收的能源和材料成本最低(即成本最低),因此利润至少是热冶金法和湿法冶金法的2倍。特别是,为了展示负极回收的利润,我们将石墨阳极的成本效益分析分开,如图4e所示。
在许多情况下,石墨负极的回收成本高和材料成本低导致利润刺激较少,因此石墨负极的回收利用较少。这在图4e中可以体现,热法和湿法冶金法石墨阳极回收的利润为2.39(不回收石墨)和2.73 $/kg负极,以及巨大的环境牺牲:大量的废物和二氧化碳排放。相比之下,瞬态回收的利润增加了307%(4.78$/kg阳极),但产生的废物最少或可忽略不计。
图4. 不同回收方法的经济和环境分析。(a)对不同回收工艺的简要比较。EverBatt分析了(b)的总能源消耗(能量和材料输入),(c)的废物排放(水和固体)(气体、水和固体),以及(d)电池回收和(e)石墨负极回收,通过比较热法、湿法冶金和瞬态回收方法的利润。
为了验证瞬态回收方法的通用性,我们从Sumwoda、ATL、索尼和CALB等不同制造商生产的故障智能手机和车载电池中回收了SG。如图5a所示,Sumwoda、ATL、Sony和CALB的材料回收效率分别为99.7%、95.9%、98.7%和99.4%,铜箔回收率为100%,具有优越的材料回收效率。值得注意的是,所有消耗过的负极都是在不知道它们的充电状态、健康状态或任何其他处理前直接拆卸的,如DMC清洗去除电解质、预烘烤溶剂蒸发,从而显示出优越的处理效率。考虑到这些因素,高回收效率表明我们的方法足够适合各种废电池的复杂负极的变化。
重要的是,正极的活性材料也可以很容易地从铝(Al)箔中分离出来。需要注意的是,我们使用了较低的冲击温度(例如,1200℃,相比Cu(1083℃),因为Al(660℃,1s)。我们演示了各种废正极(表示为S-LCO、S-LFP、S-NCM)的有效回收,获得了回收的活性材料(即HT-LCO、HT-LFP、HT-NCM)。它们的回收效率高达98.8%(LFP)、99.5%(LCO)和98.7%(NCM),显示了冲击式加热的通用性,能够实现高效的回收(图5b)。因此,考虑到我们的加热温度(如负极1500℃,正极1200℃)远远高于各种粘合剂的分解温度,如CMC(250℃)、SBR(350℃)、PVDF(320℃)等,我们的方法一般适用于各种电池系统。
同时,我们还用ICP-MS法测定了上述样品的Al杂质。如图5c所示,我们的冲击式加热方法回收的材料与废弃的正极材料(手工刮取的电极)相似,说明我们的方法在材料回收后没有很大程度上引入铝杂质。相比之下,通过机器粉碎获得的黑色质量显示铝杂质含量高出40倍。回收活性材料的结构表征也如图5d所示。从XRD模式来看,废正极材料和通过冲击型加热的回收材料之间没有明显的差异。我们的冲击式加热方法对材料结构的影响很小,将减少下一次再生的难度。
例如,我们使用水热法,通过补充Li和结构恢复来再生HT-LCO样品。RLCO和S-LCO的电化学性能评价如图S22所示。虽然S-LCO的比容量极低,但R-LCO在1C(1 mA 4.1g−1.1.1C),表现出优异的循环性能,在100次额外循环后容量保留87.8%,速率性能从0.1 C恢复到10 C。这些结果表明,由于无损结构和低杂质含量,通过冲击式加热使回收材料高效再生的可行性和优势。 在这里,我们演示了通过使用自制的卷对卷设备来实现的瞬态回收方法在阳极废料上的应用(图5e)。负极废带以5 m/min的速度释放,通过加热器和机械应力部分,石墨可以自发地连续落入集电器中。
我们证实了卷卷回收石墨中粘合剂的完全分解。与此同时,铜箔被收集在辊上,有一个干净的表面。通过结合我们的瞬态回收来分离正极和负极活性材料,可以有效地收集绕组电池中的所有固体组件。此外,通过瞬态加热(用于快速粘结剂分解)结合商业分离技术(用于物理分离),也可以有效地回收废堆叠或破碎电极的活性材料。 电池拆卸是目前电池直接回收领域的一个普遍挑战,特别是考虑到LIB电池和各种电池形式的坚固密封。如果电池拆卸能够以高效和可扩展的方式处理消耗的电池,直接回收过程的可行性和影响将得到很大的提高。到目前为止,在方便拆卸电池方面已经做了很多努力。在学术界,许多著名的专家都呼吁建立一个细胞组装的统一标准。
在行业方面,许多公司正在努力开发通用的电池拆卸机,其中一些已经实现了对方形软包装电池的大批量拆卸。可以预见的是,在未来的未来,当电池自动拆卸成熟时,直接回收方法(如本研究中报道的)可以使可持续的回收电池产生更经济、社会和环境的影响。
图5.瞬态循环利用方法的可扩展性演示。通过冲击型加热方法对各种(a)负极和(b)正极活性材料的回收效率。(c)各种正极样品中铝杂质的含量(ppm)。冲击式加热处理前后各种正极材料的(d) XRD模式。(e)负极废料及卷对卷回收示意图及图片。
总结与展望
综上所述,在这项工作中,文章报道了一种干燥、绿色和可扩展的电池回收方法,通过瞬态加热(处理时间< 1 s)方法,显示了优越的材料回收效率98.7%(石墨)和~100%完整的铜箔。超短的煅烧时间也对活性材料的影响最小,从而有利于有效的再生。石墨可以很容易地再生,具有良好的性能(在0.5 C下340mAh/g,额外180次循环后容量保留>98%),可与商业新鲜石墨相媲美。这种瞬态循环工艺一般适用于不同电池公司的各种负极,也适用于不同类型的负极(如LCO、NCM、LFP),材料回收效率>为97%。
作者还证明了这种方法完全与卷对卷过程兼容,特别有利于连续和自动回收电池碎片(~5 m/min)。Everbatt分析表明,与传统的热炼法和湿法冶金回收方法相比,瞬态回收方法需要最少的能量输入,产生最少的废物,并具有最高的潜在利润。重要的是,与以前燃烧或废弃的石墨负极相比,瞬态回收使石墨回收经济且有利可图(4.78 $/kg阳极)。因此,瞬时电池回收显示了前所未有的能源和时间效率,显著减少了废物和碳足迹,以及在可持续电池回收和再制造方面的卓越的可扩展性和自动化性。
审核编辑:刘清
-
锂离子电池
+关注
关注
85文章
3092浏览量
76506 -
锂电池
+关注
关注
256文章
7701浏览量
163476 -
车载电池
+关注
关注
0文章
15浏览量
8200 -
电解质
+关注
关注
6文章
756浏览量
19686
原文标题:华中科技大学黄云辉教授&浙江大学陆俊教授EES:高效、低碳、卷对卷电池材料回收!
文章出处:【微信号:清新电源,微信公众号:清新电源】欢迎添加关注!文章转载请注明出处。
发布评论请先 登录
相关推荐
嵌入式会越来越卷吗?
8万吨废旧锂电池及锂电池废料的综合回收利用项目落户湖南
宏工科技推电池回收预处理段解决方案,让电池实现绿色循环
行业寡头入局电池回收,首个项目受阻
10亿元!又一电池回收利用项目落户湖南
高效环保低成本!回收废锂离子电池活性材料新策略
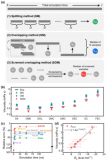
评论