PCB钻孔毛刺产生的原因及毛刺的危害
PCB(Printed Circuit Board)是一种非常重要的电子组件,被广泛应用于各种电子设备中。在PCB的生产过程中,钻孔是一个非常关键的步骤,用于连接不同层之间的导电通路。然而,钻孔过程中可能会产生毛刺,这对PCB的质量和性能会带来许多危害。本文将详尽、详实、细致地分析PCB钻孔毛刺产生的原因及毛刺的危害。
首先要了解的是,PCB钻孔的过程是通过机械钻头进行的。不同的钻头材料和设计、钻孔速度、钻孔深度、冷却液等因素都会对钻孔质量产生影响。以下是钻孔毛刺产生的主要原因:
1. 钻头磨损:钻头在长时间使用后会出现磨损,其尖端不再尖锐,变得钝,这样容易造成钻孔时的震动和振荡,进而导致毛刺的产生。
2. 钻头旋转速度过快:钻头旋转速度过快时,会产生较大的热量和摩擦力,使得被钻穿的位置周围的纤维和树脂软化、熔化,从而形成毛刺。
3. 钻孔深度过深:当钻孔深度超过合适范围时,底部的纤维和树脂会被剥离,造成毛刺的产生。
4. 冷却液不足:冷却液在钻孔过程中起到了冷却钻头和被钻穿的位置的作用,帮助减少磨损和摩擦。当冷却液不足时,钻头容易发热,同时钻孔位置周围的温度也会升高,从而增加了毛刺产生的可能性。
以上是主要的原因,钻孔毛刺的影响和危害主要体现在以下几个方面:
1. 电气连接不良:钻孔毛刺会导致PCB上的导线或跳线与钻孔周围的电路不良接触,从而影响电子元件之间的导电通路,甚至可能导致整个电路失效。
2. 信号干扰:钻孔毛刺可能导致PCB上信号线路的不稳定性,引起信号干扰和交叉干扰。这将导致电路性能下降,可能出现电压不稳定、信号失真等问题。
3. 电气击穿:钻孔毛刺产生的边缘锋利,容易形成电场集中,进而增加了PCB在高压条件下的电气击穿风险。这对高压电路来说尤为危险,可能导致短路、火灾等严重后果。
4. 焊接困难:毛刺的存在会增加PCB上焊接工艺的难度。由于毛刺的存在,焊接时通过电烙铁或其他焊接工具容易损坏电路,而且难以有效地焊接,影响焊接质量。
5. PCB表面的挤压变形:PCB表面的毛刺容易被压平或挤压变形,尤其在安装或运输过程中。这会导致PCB的形状变得不平整,进而影响PCB连接器的插拔性能和连接质量。
总之,PCB钻孔毛刺对PCB的电气性能和可靠性有着显著的影响和危害。为了保证PCB的质量和性能,我们必须在生产过程中采取相应的措施,如选用合适的钻头材料,合理控制钻孔速度和深度,充足使用冷却液等,以减少钻孔毛刺的产生。
此外,在后续的加工和使用过程中,也要避免对PCB进行过度挤压和损坏,以确保PCB的长期稳定运行。
-
连接器
+关注
关注
96文章
12655浏览量
133146 -
PCB钻孔
+关注
关注
1文章
16浏览量
9381 -
信号失真
+关注
关注
0文章
63浏览量
11247
发布评论请先 登录
相关推荐
无铅锡膏焊接后,边缘有毛刺和玷污的原因有哪些?
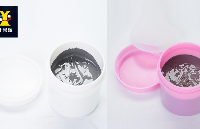
SPI从模式MISO会概率性出现毛刺的原因?
使用ADuC7020产生毛刺的原因?怎么解决?
怎么用示波器观察信号毛刺?
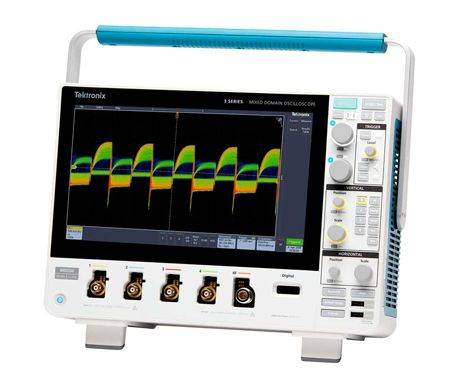
AD5764有毛刺是什么原因造成的?
什么是紧固件毛刺呢?紧固件毛刺是怎么样形成的呢?
如何最小化毛刺尺寸?如何控制毛刺方向?
什么是毛刺?毛刺的大小和方向 如何测量毛刺的尺寸?
FPGA | 竞争冒险和毛刺问题
无毛刺电压监控器的基础知识
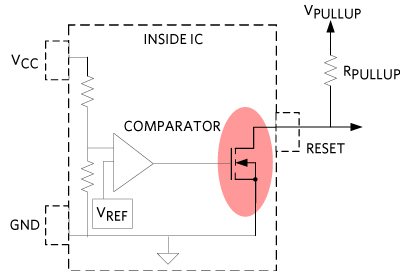
如何解决锡膏焊后的毛刺和玷污问题?
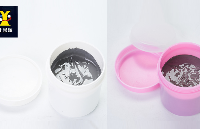
评论