来源:机车电传动
摘要
碳化硅功率器件具有耐高压、开关速度快和导通损耗低等优点,因此正在逐渐成为电力变换系 统的核心器件,尤其在新能源汽车、可再生能源、储能、数据中心、轨道交通和智能电网等领域,器件的应 用越来越广泛。然而,碳化硅器件持续的小型化和快速增长的功率密度也给功率模块封装与热管理带来了新 的挑战。传统封装结构和散热装置热阻较大,难以满足碳化硅器件高热流密度冷却需求,同时,高功率密度 模块散热集成封装需求也日益增长。针对上述挑战,文章对国内外现有的典型功率模块封装结构进行了详细 介绍和分类对比;枚举比较了不同功率模块散热方式及其技术特点,如热扩散装置、对流换热和相变散热 等;最后,结合以往的碳化硅功率模块热封装研究,对下一代碳化硅模块封装与热管理技术面临的挑战和未 来的发展趋势进行了展望。
0 引言
碳化硅金属氧化物半导体场效应管(SiC MOSFET) 作为典型的宽禁带半导体器件,相较于硅基功率器件, 具有耐高压、耐高温、开关速度快、导热率高和导通电 阻低等优点,因此逐渐被用于新能源、光伏发电、轨道 交通和智能电网等重要领域的电力电子系统中,助力系 统能效与功率密度的不断提高。为充分发挥碳化硅功率 器件的上述优良电气特性,需通过封装结构实现电信号 的可靠连接与器件结温的稳定控制。传统封装和热管理 技术在碳化硅功率器件应用中面临着一些关键技术挑战。
目前已有的商用碳化硅功率模块大部分仍沿用硅基 器件的平面封装方式,其封装结构如图1所示。在该模 块结构中,多个功率芯片(包括SiC MOSFET和碳化硅 肖特基二极管SBD)被焊接或粘贴于同一绝缘衬板的金 属化表面,该衬板既承担模块的电气绝缘作用,同时又 是模块整体封装热阻的重要组成部分,而功率芯片正面 的电气连接则采用铝线/铜线键合方式来实现。
常见的功率器件失效方式如引线键合翘曲/脱落、 焊料层裂纹/剥离以及芯片过热损坏等均是由热封装结构 散热能力不足引起的。在额定电流和电压相同的前提 下,碳化硅器件的尺寸可以比硅器件更小,这对高功 率密度、高散热能力的模块设计与制造提出了要求。商 用1 200 V/150 A硅基IGBT和碳化硅基MOSFET器件尺 寸对比如图2所示,由图2可知后者的面积仅约为前者 的1/5。因此,虽然碳化硅器件导通和开关损耗显著降 低,但其衬底面积的收缩会导致模块热阻的显著增加。
针对上述问题,国内外学者分别从封装结构和散 热技术2个方面出发,通过减小封装导热热阻和外部散 热热阻来满足碳化硅高热流密度散热需求。本文聚焦 碳化硅功率模块热封装结构和高效散热方式 2 个关键 点,对现有的碳化硅功率器件封装和热管理技术进行 分类梳理和总结,并在此基础上讨论高功率密度碳化 硅封装在散热方面面临的挑战和重要发展趋势。
1 碳化硅器件低热阻封装技术
典型的碳化硅功率模块封装的热阻由芯片衬底、 芯片焊料层、覆铜陶瓷基板 (DBC)、基板焊料层、金 属散热基板、热界面材料 (TIM) 和散热器的热阻组 成。碳化硅具有良好的导热性能[270 ~ 450 W/(m·K)], 其主要热阻包括焊料层、DBC、金属基板、TIM 和散 热器。因此,双面冷却封装、压装封装和冷却集成封 装等先进封装技术被相继提出,以通过充分利用碳化 硅芯片底面及顶面的散热面积、缩短结至流体或环境 的热流传递路径来降低模块封装热阻。
1.1双面冷却封装技术
为实现碳化硅功率器件的可靠双面散热,在传统 平面封装的基础上,引入如顶部铜引脚框架或铜带、 金属垫块等顶部互联方式,并采用银烧结来实现芯片 侧的低热阻互联,该类封装可承受220 °C以上的高温 (如图3所示)。由于芯片上下表面均采用DBC焊接散 热,热流路径在垂直方向上出现2条并联支路,相较于 传统的单面冷却模块,其热阻可降低 38%。此外, 该封装可完全消除功率回路的引线键合结构,借助高 可靠性界面实现互联,相较于传统封装可实现10倍以 上的可靠性提升。中国中车、重庆大学、天津大 学和美国弗吉尼亚理工学院等分别针对双面冷却模 块的封装结壳热阻、热应力和外部射流冷却集成等开 展了多物理场耦合优化研究。
压装封装则是另一种在高压直流输电和轨道交通 等领域广泛应用的双面冷却封装形式,具有无焊接点、 无引线、可靠性高、双面冷却和高功率密度等特性, 突破了传统器件键合点和焊料层失效的瓶颈问题。浙江大学[10] 设计提出的碳化硅双面冷却压装模块结构如 图4所示,该结构通过在薄膜中介层中采用微型柔性压 脚来实现器件顶部电热连接。值得注意的是,由于该 压装模块的散热器被涵盖在功率回路中,为避免引入 过大寄生电感,设计了基于低温共烧结陶瓷 (LTCC) 的超薄微通道结构,其结流热阻为0.7 K/W。
1.2 冷却集成封装技术
针对传统平面封装或上述双面冷却封装的研究大 多将散热器独立于模块封装以外,因此,需要引入低 导热系数[1~20 W/(m·K)]的热界面材料,以减小接触热 阻,而这会显著增加模块的结流热阻。因此,为应对 日益增长的碳化硅功率模块冷却需求,需要进一步减 少或消除热路径中的许多封装层,从而降低热阻。
1.2.1 散热基板液体冷却
2014年,美国橡树岭国家实验室率先开展了碳化硅 功率模块集成液冷研究,并指出冷却集成功率模块的结 流热阻比传统封装模块对应值低30%。散热基板的形 式也历经针翅阵列、波状带翅片、ShowerPower三维流道(流道结构如图5所示)和双层逆流流道等不同 拓扑演变,其中针翅阵列和三维流道由于其均温效果 好、安装简单等优点,已经成为主流散热方式,被广泛 应用在英飞凌和丹福斯等厂商的功率模块产品中。
1.2.2绝缘覆铜基板嵌入式冷却
为了进一步缩短热流传递路径,绝缘覆铜基板集 成式冷却技术也被提出。该技术通过激光刻蚀或干 法刻蚀等工艺在绝缘衬底中加工出宽度仅为百微米级 别的微流道结构,从而充分利用微通道的对流散热能 力,降低封装结流热阻。在此基础上,斯坦福大学提出了一种基于覆铜绝缘陶瓷基板激光刻蚀的多层歧 管微流道功率模块结构原型,其单位面积结流热阻为 0.2 cm2·K/W。北京大学则在绝缘碳化硅衬底中构建了 梯度嵌入式微型针翅,并利用晶圆键合和纳米银烧结工 艺,制备了碳化硅衬底覆铜绝缘基板,最终封装得到的 功率模块相比普通的基板液冷方案,其结至流体的热阻 下降了78.9%。上述绝缘基板嵌入式冷却方法可削弱陶 瓷基板导热热阻在结流热阻中的占比,显著提高冷却能 效,但由于微流道刻蚀工艺复杂、封装热力可靠性不 明,其具体封装工艺和拓扑结构有待进一步优化研究。
1.2.3无绝缘基板直接冷却封装
常用的绝缘陶瓷基板材料,如氧化铝、氮化铝和氮 化硅等,相较于常规的铜铝金属材料,具有相对较低的 导热系数,其热阻和可靠性会对功率模块的整体性能产 生重要影响。为消除其影响,美国相关机构于2017 年提出了采用电子冷却液直接冷却的无绝缘基板封装技 术,以突破传统封装的散热、可靠性和寄生电感挑战。该结构将功率器件直接堆叠在铜质散热器层之间,并通 过芯片顶部和底部的散热器实现直接接触式冷却,最终 的封装单位面积结流热阻为0.25 cm2·K/W。
这种设计可消除单一功能组件,使得散热器同时 承担电气连接与冷却2种功能,大幅减少封装热阻,但 是,由于电气绝缘冷却液的导热率低、散热面积有限, 其冷却效率受限。受此启发,西安交通大学设计制 备了三维垂直堆叠无绝缘基板功率模块,模块结构如 图6所示,其中的一个散热器被直接嵌入到输出功率端 子中,相较于外侧双面液冷方案,该内嵌散热器可将 芯片最大结温降低33.8%。
三维垂直堆叠功率模块封装对多层键合或焊接时 的垂直高度有精确要求,这也使得其制备过程较为复 杂,增加了广泛应用的难度。美国国家可再生能源实验室则基于电子冷却液冷却提出了一种无基板紧凑 型功率模块冷却集成封装结构,如图7所示,该结构通 过将芯片直接焊接到铜质翅片散热器上,在直流输入 和交流输出2个电位上采用不同的散热器,并在散热器 背面使用优化设计得到的分流层,引导流体直接冲击 翅片表面,实现了低至 0.19 cm2·K/W 的热阻。与同等 条件下的常规液体基板冷却方案相比,该方案的热阻 下降约56%,泵功率下降约90%。
无绝缘基板冷却集成封装方案是近年来针对功率芯片高热流密度散热需求提出的一种全新的封装结构, 其可充分利用功率芯片的正面与背面的热传导扩散作 用,同时消除了导热热阻较大的绝缘基板,是超高功 率密度碳化硅模块封装的重要发展方向。
2 碳化硅功率模块热管理技术
相较于直接改变功率模块的整体封装结构或减少封 装层数的方案,通过引入热扩散装置、对流换热技术和 相变散热技术等先进热管理方法,可在尽可能保持现存 封装结构的基础上,为高热流密度碳化硅功率芯片提供 可靠冷却。因此,先进的外部热管理技术在冷却集成封 装和封装外部热管理方面均有着广阔的应用前景。
2.1 热扩散装置
热扩散装置可利用工质气液相变的均温性和热质 传递能力,将局部集聚的高密度热流快速扩散至更大 表面积。热管就是一种理想的热扩散装置,其内部工 质始终工作于饱和温度,饱和蒸汽从蒸发端流动至冷 凝端的压降较小,因此热管两端具有较小的温差。利 用热管或其变形结构 (如环路热管、脉动热管、重力 热管和均温板等) 可显著提升电力电子设备冷却效果。值得注意的是,热管这类热扩散装置的主要作用只是 将蒸发侧局部集中热流相对均匀地扩散到冷凝侧,而 热量的散发最终仍需依靠冷凝侧外部散热器,这种装 置工作可靠、无须外部冷却介质,因此常与空气冷却 相结合使用,提升空气冷却能力。
2.1.1 环路热管、脉动热管和重力热管
环路热管由毛细泵、冷凝流道、储液器和蒸发流 道组成,它们依次串联形成循环回路。其中毛细结构 的芯吸作用作为驱动力,将功率器件产生的废热通过 工质的气液相变从蒸发器传递至冷凝侧。文献[20]和文 献[21]分别对环路热管在IGBT功率模块和汽车电子上 的应用进行了试验探索,制备得到的环路热管样机可 实现 1.5 m 的长距离热量传输,且在热源温度不超过 100 °C时,传输热量功率超过了900 W。相较于环路热管,脉动热管的结构简单紧凑,但 其脉动具有很大的偶然性,微通道内部气液两相脉动 流动导致工质的温度、压力和速度难以通过计算确定。美国相关机构将脉动热管应用于全桥功率模块的冷 却,发现相较于传统的空气冷却和冷板冷却,其冷却 温度均匀性和散热能力均更好。然而脉动热管由大量 的微小脉动通道组成,难以完全覆盖大尺寸和大功率 的功率模块冷却需求。因此,文献[23]基于由三维U型 回转毛细管阵列组成的脉动热管开展功率器件冷却研 究,发现在最高负荷(400 W)下,脉动热管蒸发侧到 空气的热阻低至0.13 K/W。然而,脉动热管毛细管束 阵列在运行中易出现振动噪声,这会影响其与底板及 功率模块的界面连接可靠性。
重力热管由于其无须毛细芯、价格低廉,也逐渐 应用于功率模块的热管理中。以往研究表明,传统的 重力热管可对热损耗功率为6 kW的IGBT功率模块有 效冷却,同时还能解决IGBT模块的局部高温问题。南 京理工大学提出的一种自然冷却型重力热管散热器的方案如图8所示,该散热器采用蒸发器取代传统功率 模块封装中的金属基板,可消除传统重力热管嵌入基 板所形成的接触热阻,大幅改善热管的冷却性能。
2.1.2 毛细芯热管和均温板
毛细芯热管和均温板的蒸发侧和冷凝侧换热面均 有毛细芯吸结构,可促进蒸发表面的薄膜蒸发以及凝 结液的快速回流。典型毛细芯结构包括微沟槽、金属 丝网和烧结粉末等,因其稳定散热能力而被广泛应用 于处理器芯片和移动电子设备的热管理中,在功率模 块的热管理方面也得到越来越多关注。
在毛细芯热管方面,长沙理工大学设计了一种 面向功率模块冷却的三维异形平板热管,其蒸发侧采 用平板块状设计,而冷凝侧则沿用传统管状阵列结构, 对比发现该异形结构可将热源面温度降低6.7~13.7 °C, 其最大等效导热系数可达 10 000 W/(m·K)以上。类似 地,西安交通大学针对多电平变换器中功率模块的 冷却需求,基于功率模块的三维热力仿真,通过匹配热管与芯片排布位置实现热扩散最大化,设计得到如 图9所示的O型热管散热器,该散热器最高可将局部热点温度降低20%。
与热管不同,均温板具有轻薄紧凑的结构和出色 的面内横向热扩散能力,可集成在功率模块内,显著 降低结壳热阻。中车株洲电力机车研究所有限公司在功率模块与散热器之间直接添加均温板开展散热测 试,测试结果表明均温板可将散热器温升降低12.7 K, 且使得功率器件的温度不均匀性指数下降超过 55%。诺丁汉大学和丹尼克斯公司则采用均温板直接替代 功率模块的金属基板,使得结温、温度不均匀性和总 热阻相较于传统封装分别下降34.6%、76.6%和41.6%, 可见均温板的高效热扩散能力可为功率模块紧凑封装 设计提供新的解决方案;同时他们还通过三维有限元 仿真验证了均温板对热应力、蠕变、塑性应变的能量 耗散及热疲劳寿命等的改善作用。
在碳化硅模块应用方面,西安交通大学则采用 类似方案,针对多电平变流器中非均匀热流功率芯片 的冷却需求,评估了均温板对芯片温度均匀性和温度 波动特性的影响,试验发现嵌入均温板后模块最高温 度以及温度极值差分别下降了 11.1% 和 18.7%。此外, 他们还探索了将均温板嵌入到碳化硅功率芯片与覆铜 陶瓷基板之间的封装结构(如图10所示),结果发现 该模块可在芯片热流密度高达 632 W/cm2的条件下运 行,且芯片结温仍在允许范围内。但需要注意的是, 受目前均温板的热质传递能力限制,直接嵌入在芯片 底部的均温板体积较大,可能会带来寄生电感、键合 线可靠性等问题。
2.2 对流换热技术
对于高热流密度碳化硅功率器件,对流换热相较 于辐射冷却等散热方式而言,能够提供相对较强的冷 却能力,是将热量传递至环境中所必须的热管理手段。对流冷却技术按冷却工质分类,可分为空气冷却和液 体冷却2类,其中空气冷却由于技术成熟、结构简单和 易于获取等优势,已成为各类电力电子器件冷却的首 选方案。然而功率器件热流密度的不断增长也使得先 进液体冷却技术成为高功率密度碳化硅模块热管理的 发展趋势之一,微射流冲击和微通道单相对流等高效 液冷技术受到日益广泛的关注。
2.2.1 射流冲击冷却
由于流体的直接冲击作用,射流冲击可提供远优 于常规对流换热方式的换热性能,然而剧烈的流体冲 击和方向转折往往会带来较大的流体压降,因此,合 理的流体分配是提高冷却能效的关键。佐治亚理工学 院提出了一种DBC嵌入式针翅射流冷却方案如图11 所示,并结合仿真与试验得出,相较于基板直接针翅 结构,该方法可将结至流体的总热阻减小37.3%(逆变 器冷却总流量为 10 L/min)。欧洲微电子研究中心设计制备了喷嘴直径为500 μm的4 × 4射流阵列冷却装 置,其热阻低至0.25 K/W (0.16 cm2·K/W),该装置在 热源区域内呈现出良好的温度均匀性。在应用方面, Teledyne科技公司设计制备了射流冷却高温碳化硅功 率模块,试验结果表明在 151 W 的热功耗下,射流冲 击可将器件温升下降 74%,其性能要优于商用微通道 散热器。亚琛工业大学则提出了针对单个电力电子 芯片的独立射流腔室冷却方案,削弱器件间的热耦合 作用,从而提升温度分布均匀性。
射流冷却结构可紧凑嵌入到器件封装结构中来实 现复杂电热耦合,而其中的关键点在于根据电热系统 参数间的相互影响来构建并优化电热结构[37] 。因此, 如何结合各类优化方法 (如遗传算法、神经网络等) 来开展面向优化目标 (冷却温度均匀性、冷却能效和 热阻等) 的电热协同设计,是先进射流冲击方法在碳 化硅模块封装热管理中应用的关键科学问题。
2.2.2 微通道单相对流冷却
微通道因其较大的表面积体积比而成为高功率密 度电子器件高效冷却最有前景的技术方向之一。微通道一般指水力直径在几十或几百微米量级的微小通道, 常以微通道阵列的方式出现以满足大面积冷却需求。
格勒诺波尔电气工程实验室提出了一种基于集 成微通道冷却器的高效冷却功率器件概念,微通道阵 列直接由多个相互平行且垂直穿过晶圆的流体过孔组成,流体将直接进入垂直功率器件的漂移区并垂直于 器件的 PN 结,从而实现极致紧凑散热。试验结果表 明,该结构存在电气和热管理上的理论可行性,但其 测试热阻和理论值偏差较大,且热阻值较大。
虽然随着微通道水力直径的减小,其换热性能会 随之改善,但由此带来的压降上升将导致冷却系统效 率降低,因此需要采用包括歧管微通道和双层逆流 微通道在内的结构来实现液体的高效利用。西安交通大学[提出了面向功率模块的基板逆流微通道冷却集 成设计方案,并发现短流程微通道冷却方案的冷却能 效系数可达长流程方案的 6 倍以上。洛桑联邦理工学院则采用了多个微流体冷却器,并提出一种高效冷 却的氮化镓DC-DC变换器方案,其装置如图12所示, 装置引入了2个歧管分流层来实现对20个氮化镓晶体管的均匀液体冷却,结果表明在 60 K温升下该方案可 实现对高达600 W热量的可靠冷却。
目前微通道单相冷却技术已经可以满足热流密度 高达1 000 W/cm2的单芯片可靠冷却,但在功率模块多 芯片冷却应用中还存在通道过小易于堵塞、各芯片 冷却不均等问题,因此如何通过优化封装工艺来实 现可靠流体分配与均匀冷却是技术应用的关键问题。微通道液体冷却装置常采用的工质包括水、防冻液 和电子冷却液等,这些工质相对较低的流体导热系数导 致其冷却能效较低。液态金属作为一种高导热流体,近 年来也逐渐被用于微通道冷却装置。以往试验研究表明 ,在相同的微通道结构条件下,采用铟稼锡合金材料作为冷却工质时其对流热阻仅为水的60%。此外,液 态金属可通过电磁泵流量主动控制和液滴主动热开关等方式集成在热管理系统中来帮助实现芯片结温的 主动调控,减小芯片间温差和温度波动幅度。
2.3 相变散热技术
受限于工质有限的热容和导热系数,单相对流换 热技术的换热系数往往较低;相变散热技术充分利用了工质的相变潜热,因此其冷却效率和均温性均显著 优于单相对流换热,因此,相变冷却技术是高功率密 度碳化硅功率模块冷却的重要发展方向。
2.3.1 相变材料
由于碳化硅功率芯片的尺寸大幅减小,其对应的热 容显著下降,因此在相同工况下,碳化硅功率器件面临 更加严峻的由温度波动带来的热可靠性问题。不同于热 扩散装置,相变材料(PCM)主要利用固液相变潜热来 实现功率器件瞬态热量的“削峰填谷”(材料融化可吸 收瞬态尖峰热流,材料凝固可释放热量),因此可将其 作为一种减小器件温度瞬态波动的有效热管理手段。
重庆大学开展了面向平面封装IGBT模块 、压装封装模块 、晶闸管和整流器等多种传统功率器件 的PCM热缓冲特性研究,在封装结构中嵌入低熔点合 金相变材料,并通过试验验证了固液相变材料对瞬态 过电流工况或周期性波动热流工况的结温钳制作用, PCM材料可减小功率模块的最高结温以及结温波动值, 提高功率模块可靠性。在碳化硅功率模块应用方面, 浙江大学基于数值仿真开展了嵌入PCM的碳化硅功率 模块封装结构优化研究,封装结构如图13所示,并 提出一种枝干状的相变材料容器及其对应封装结构, 能够降低碳化硅器件结温波动极值差12 K以上。
目前,相变材料展现出优异的瞬态热管理潜力, 理想的相变材料应具备储热密度高、体积热膨胀率小、 物化性质稳定和热导率高等特点,如何进一步提高相 变材料的瞬态响应速度、储热密度和长期稳定性是该 技术发展的重要方向。在碳化硅器件应用方面,目前 针对碳化硅功率模块的PCM封装工艺和PCM瞬态热作 用机理的研究都存在较大不足。
2.3.2 气液两相冷却
气液两相对流冷却可充分利用冷却工质的气液相 变潜热,同时气液相界面温度被恒定在饱和温度,因 此其冷却能效要显著优于单相对流。根据流动形式差 异,气液两相冷却可细分为池沸腾和流动沸腾。
其中池沸腾即大空间浸没式相变冷却,待冷却器 件被直接放置在电子冷却液中,通过表面的液体气化 吸热来实现冷却。3M 公司开展了 IGBT 模组的浸没相变冷却原型试验,结果表明被动式两相浸没冷却性 能与双面微通道水冷的功率模块性能相当,且其封装 结构可显著简化,无须外部泵、冷板以及DBC绝缘基板等。西安交通大学则将浸没式相变冷却技术应用 于高压高速脉冲发生器冷却中,结果表明使用该冷却 方法可在不改变原有电路排布的前提下降低壳至环境 的热阻。作为一种被动的高效冷却方法,目前针对碳 化硅功率模块的浸没式冷却研究仍较少,存在池沸腾 换热性能不足、微纳多孔相变换热表面耐久性差、浸没式冷却系统密封要求较高以及工质兼容性等问题。
通过结合微通道高效对流换热和相变换热,流动沸 腾可实现高热流密度的高效冷却。代尔夫特理工大学采用制冷剂R1234yf和热测试芯片,对通道截面为0.5 mm×6 mm的微通道阵列开展了两相冷却性能测试,结 果表明该装置可满足高达526 W/cm2的芯片热流密度的冷却需求,且结温低于120 °C;他们还指出平行微通道 在流程方向上存在显著的冷却不均。巴斯克大学结合试验与数值模拟研究发现,相较于单相水冷却,采用制 冷剂R134a的流动沸腾冷却可将IGBT器件的结温降低 39 °C,且两相冷却时各芯片间的温度均匀性显著提高。
流动沸腾有着更高的冷却性能,但面临着气液两 相流动存在不稳定性、工质循环系统密封要求高、两 相流体分配不均以及相间复杂作用难以准确建模等挑 战,目前仍需更多相关研究以填补上述空白。
3 结论
碳化硅功率模块的冷却系统设计已经逐渐成为其 应用的关键组成部分,为满足日益增长的功率密度和模块可靠性需求,先进热管理技术必须与其封装紧密结合,才能获得最大收益。本文对现有的主要碳化硅 功率模块封装冷却形式以及热管理技术进行了较全面的综述总结。
在封装层面,双面冷却和冷却集成是高功率密度碳 化硅模块封装的发展趋势,在未来的功率模块封装中, 减少芯片散热路径上的导热热阻是先进封装热管理的关键,其主要措施包括充分利用芯片顶部散热(采用更大 面积的顶部接头)、采用散热基板集成冷却、DBC集成 冷却或直接液冷封装等。需结合碳化硅功率模块封装工艺和应用场景,开发兼容的热管理集成技术,评估其对 模块热学和电学性能的影响,研究冷却工质和封装结构 对电气绝缘以及模块可靠性的影响机制。
在热管理技术方面,采用热扩散装置尤其是热管 和均温板是有效提升现有碳化硅功率模块空气或液体 冷却性能的重要手段,需要对瞬态工况下装置的启动 性能以及功率模块的可靠性开展进一步研究。相变材 料作为一种特殊的储热元件,有望作为碳化硅模块热容的补充,减小结温的波动幅度从而提升模块可靠性。射流、微通道单相对流和气液两相冷却等方式可满足超高功率密度模块的冷却需求,需要结合流体分配和器件排布,形成碳化硅模块电热协同设计方法,以指导具体应用的定制化热管理设计,满足结温控制、均温性和封装结构等多方面的限制。
由于技术迭代或变化的渐进性,目前碳化硅模块 封装供应商仍倾向于沿用硅基功率模块封装的技术路线,因而正在研究的新型封装和先进热管理技术仍需 更充分地验证与进一步完善才能实现广泛应用。
审核编辑:汤梓红
-
MOSFET
+关注
关注
141文章
6575浏览量
210148 -
功率器件
+关注
关注
40文章
1538浏览量
89490 -
功率模块
+关注
关注
10文章
401浏览量
44699 -
热管理
+关注
关注
11文章
376浏览量
21425 -
碳化硅
+关注
关注
24文章
2437浏览量
47543
原文标题:碳化硅功率模块封装及热管理关键技术
文章出处:【微信号:today_semicon,微信公众号:今日半导体】欢迎添加关注!文章转载请注明出处。
发布评论请先 登录
相关推荐
碳化硅压敏电阻 - 氧化锌 MOV
新型电子封装热管理材料铝碳化硅
碳化硅深层的特性
电动汽车的全新碳化硅功率模块
国产碳化硅MOS基于车载OBC与充电桩新技术
功率模块中的完整碳化硅性能怎么样?
应用于新能源汽车的碳化硅半桥MOSFET模块
浅谈硅IGBT与碳化硅MOSFET驱动的区别
碳化硅肖特基二极管技术演进解析
碳化硅功率器件:革命性的封装技术揭秘
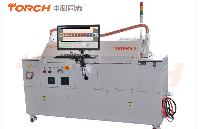
评论