锂电池可以分为方形、圆柱、软包三种形态,从技术角度看,三种形态的电池各有千秋,且各有劣势。但事实上,通过技术及数据分析,大圆柱电池在经济性、安全性和回收利用价值等方面都更具明显优势。比如在降本方面,46系列电芯体积变大,需要的电池单体数量下降,焊接配件相应减少,提高电池成组效率,简化BMS管理难度;而在性能方面,较大尺寸使得金属外壳占比降低、正负极活性材料的比例上升,能量密度提高;此外全极耳技术的应用,亦可缩短电子路径,降低电池内阻,减小充放电过程中的损耗,提升放电效率。
在讲4680大圆柱之前,有必要介绍锂电池的三种封装形式:方形、圆柱、软包,顾名思义,可以直观的从外观上看出其中区别。而从性能的对比上看,三者又各有所长所短:
1) 方形电池:最大的优势就是成组效率最高(2020年1月数据,系统成组效率:方形70%>圆柱65%>软包60%);最大的劣势是安全性、一致性差。
2) 圆柱电池:最大的优势就是生产效率最高(主流型号每分钟在200左右,方形10-20,软包更低)、一致性高;相对劣势是成组效率比方形低、能量密度比软包低。
3) 软包电池:最大的优势就是能量密度和安全性最高;最大的劣势就是制造工艺要求高、一致性差,成本最高。
正是基于三种封装形式的各自性能差异,电池厂(包括整车厂)都有自己的路线选择,以电池厂为例:像国内的宁德、比亚迪、中航等主要是方形;亿纬方形、圆柱都有布局;孚能主打软包。国外的LG软包出身,目前也重点布局了圆柱;松下主打圆柱;三星SDI主要是方形。
目前从份额占比来看:方形占大头;而回溯历史份额来看:国内国外还有所不同,并且在各个阶段也有所差异。(1)2017年之前:我国与海外三种类型电池市场份额变化趋势相同,方形60%以上、软包10%左右,剩余的圆柱。(2)2017年之后:国内和海外就表现出完全不同的变化趋势。其中,国内:2017-2019年随着宁德和比亚迪的崛起,带动方形电池占比提升,2019年达到近85%;2020年随着国产特斯拉的放量,圆柱电池占比有所回升,反观软包则持续受到挤压。国外:2017-2019年松下伴随特斯拉全球崛起,圆柱占比从28%提升至51%;2020年欧洲电动车渗透率快速提升,LG软包放量(欧洲市场更青睐软包),但到了21年,出现电池安全召回事情,叠加大众开始选择方形电池,软包遇冷。
为什么看好大圆柱?——A:一是看好特斯拉们;二是大圆柱确实有一些突出的性能优势!
特斯拉是全球电动车的领导者,也一直是圆柱电池应用的领导者。
如今的特斯拉毋庸置疑是全球电动车的领导者,尤其在技术创新上更是全球新能源车的“风向标”,因此对其技术创新应尤为重视,从而把握其中确定性的产业趋势。
就电池而言,十年以前,市场上没有一款“十全十美”的动力电池,发展初期的特斯拉为其第一代车Roadster选择电池方案时,即是在比较中选择了“安全性、一致性好的18650圆柱电池”,从而正式开启了圆柱电池应用于纯电动车的时代。
2017年,特斯拉开始将其电池由18650切换至21700,率先应用于新车型M3中(后来的爆款车型)。21700相较于18650在单电芯和系统方面性能均有明显提高,在 2019-2020年也是迅速取代18650成为占比最高的圆柱电池。【注:18650中18指圆柱直径,65指高度,0指圆柱;21700、4680类同】
2020年底,特斯拉发布新一代电池4680。4680大圆柱相较于21700,在规格、成本、安全、使用寿命等方面又实现了全新的突破:续航里程提升16%,充放电功率提升6 倍、容量提升5倍,度电成本可以下降14%。
在特斯拉的极力推动下,随着46大圆柱的产能爬坡,预计也会在较短的年限内完成渗透(类比21700替代18650的速度)。
单独看4680是一项重大创新,而打包“4680+CTC+一体化压铸”更是一项“极限制造”的系统创新,1+1+1>3。在整车内卷加剧的情况下,成本将是车企竞争力的关键,而特斯拉通过“4680+CTC+一体化压铸”一套组合拳的技术创新,实现了极致降本。从这个层面去理解,就更不得感慨特斯拉的厉害,也不难理解特斯拉大力推4680大圆柱的必要性。
宝马是46大圆柱的积极推进者。宝马将从2025年起在“新世代”车型中使用46大圆柱电芯(包括4695和46120两种不同型号)。目前宝马已经给宁德、亿纬、远景各自定点40GWh的46大圆柱订单。通用汽车希望在未来的电动车型中从软包电池转向大圆形电池。蔚来汽车:23年2月,据消息人士称蔚来计划在合肥新建电池工厂,规划产能40GWh,将投产自研的46系列大圆柱电池。此外,包括保时捷、江淮、东风岚图等多家主流车企也在跟进大圆柱电池,对大圆柱上车表达了强烈的意愿。
国内外主流企业均在布局。国内有宁德、亿纬、远景动力、比克、国轩;国外有LG、松下、三星SDI等多家头部电池企业均已经规划布局、扩产46大圆柱。
7月18日,比亚迪采购官方微信号发布招募公告,拟对2023年大圆柱电池全自动烘烤线设备实行供应商公开招募。比亚迪此次招募的产品为全自动接触式高真空烘烤线,主要用于大圆柱电池注液前的电芯烘烤。电池的生产包含约21道工序,烘烤、注液处在整个生产程序的中间位置。工作群研究大圆柱电池”。如今的大圆柱电池生产设备采购消息,无疑是比亚迪即将生产大圆柱电池的“实锤”。
特斯拉们为什么大力发展46大圆柱?——本质:大圆柱具有一些突出的性能优势
①做圆柱电池的好处(圆柱电池相较于方形、软包的优势)
在文章的最开头部分,我们已经比较过圆柱、方形和软包3种封装形式的优劣,其中圆柱电池绝对优势就是生产效率和一致性最高,进而能带来产能的快速效应和成本的摊薄;其次,相对优势上,比方形更高的安全性,比软包更高的成组效率等,这些优势都是特斯拉们簇拥圆柱电池的理由。
②把圆柱电池做大的好处(46大圆柱相较于21/18圆柱的优势)
为什么是46?——这是特斯拉经过数据论证,得出46 mm 是续航提升和降本的最优解。而对于高度,目前业界并没有定论,像宝马46大圆柱有高度90和120的两个型号。
把电芯变大最直接的好处就是降低电池包BMS难度,单车带电量70多度的车18650需要7000+个、2170需要4000+个,庞大的数量对电池系统的连接和热管理提出极高要求,这也是之前较少有车企选择圆柱路线的主要原因之一,但如果是4680单体数量下降到1000个以下,BMS大大简化。
大电芯2大核心工艺创新:全极耳、干电极
全极耳→降低内阻、减小发热、提高快充速度。传统锂电池多单极耳,4680创新性提出全极耳,全极耳明显缩短电子流通路径(传统800-1000mm,4680只有80mm),进而降低内阻(传统>20mΩ,4680为2mΩ),降低发热量(传统上升60度,4680最多上升20度),能够适用更大电流快充;同时全极耳下电池内部温度分布更加均匀,热稳定性更好。
电极→降本增效、提升电池能量密度。目前正负极主要采用湿法涂覆工艺,而特斯拉提出的在4680运用的干电极能够降本10-20%+,生产速度提升至之前的7倍,能量密度提升5倍,寿命增加1倍。(难度大,第一代4680做了妥协)
大电芯材料体系创新
具体包括主材和辅材两个方面,以实现更高的能量密度、快充速度、安全性等:
主材聚焦于产品升级迭代:包括正极高镍化,负极硅基化,电解液新型锂盐LiFSi添加量上升,结构件强度要求提升等。
辅材聚焦于新材料导入:包括芳纶涂覆、碳管三代化+单壁化等。
最终,在上述这些系统性的选择和创新下,46大圆柱得以表现出突出的性能优势,4680相较于21700在性能上又实现了全新的突破:续航里程提升16%,充放电功率提升6 倍、容量提升5倍,度电成本可以下降14%。特斯拉2020年9月提出4680,彼时目标是2022年实现年产能100GWh,如今快三年过去,从后视镜看,4680实际量产情况是不及预期的。虽迟但到,2023年46大圆柱将真正迎来放量元年:特斯拉22年底加州工厂产线周产能已爬坡至86.8万颗,能配套1000辆Model Y,对应年产能约4GWh;此外,特斯拉也表示4680已经熬过了量产的最困难时期,并拟在内华达州扩产100GWh的4680年产能。
此外,给特斯拉配套的松下、LG也即将出货,国内进展最快的亿纬预计下半年也会开始出货。从特斯拉以及电池厂的进度来看,23年46大圆柱产量将首次突破双位数,作为一种从0→1的新技术,兑现1即将迈入从1→10/100的快速增长阶段,产业趋势的确定性已是100%。23年开始放量,24年大规模放量,将突破100GWh,往后看23-25年整个46大圆柱电池出货量都将保持翻倍式的增长,在整个成长赛道都是屈指可数的高景气细分。
此外,46大圆柱电池除了用在市场认知的电动车、皮卡等动力领域,还有望应用于储能领域,且已有其他公司规划了储能大电芯,如此大圆柱的天花板不再局限于动力,而是动力+储能。
软包电池装配线是软包锂电池生产的中后段工序,主要是对接叠片机过来的裸电芯,对电芯进行极耳的焊接、铝塑膜的冲坑入壳以及电芯入壳后的封装等工序。组装线的设计原理主要是依据电池的生产工艺流程进行产线的大致布局,具体取决于电芯的尺寸大小、电芯极耳的单出或者双出以及电芯装配所需要的生产效率等。
软包组装线概述
1.1 组装线设计原理及原则
目前针对组装线的形式的选择主要取决于电芯的大小规格,对于长度在390mm以下的电池规格,极耳焊接机、包装机以及包装机后段一般采用凸轮分割器驱动的转盘结构方式,此种结构布局方式结构紧凑,占地面积小,局限于转盘精度,转盘越大,对于电芯的装配精度越差,同时负载的加大也制约了转盘的启停难度和效率。转盘式组装线布局如图1所示。
图1 转盘式组装线布局
对于长度在390mm以上的电池规格,极耳焊接机、包装机以及包装机后段一般采用直线结构方式,此种布局方式能够满足大电池工位切换的定位精度,工位切换效率高,有更好的生产效率提升空间。缺点在于占地面积比较狭长,工位切换的驱动机构较复杂,成本相对较高。直线式组装线布局如图2所示。
图2 直线式组装线布局
1.2 组装线节拍分配
在组装线的设计过程中,对于节拍的控制主要取决于各工位生产的瓶颈工位的限制,例如实际产能需求为8PPM,考虑到设备的综合稼动率问题,一般实际按照10PPM进行设计,针对瓶颈工位会采用多工位的方式进行,例如焊接机段的极耳预焊中的保护片上料机构、Tab焊接中的Tab上料机构、包装机中的顶底封封装时间、侧封封装时间等。在对比产能要求后,计算出每个工位所需要的工艺时间,在不满足的情况下就需要进行多工位设计。例如当设备效率要求12PPM时,每个电芯的工艺生产时间为5s,某些客户对封装的时间要求就达到了4~5s,加上电芯工位的切换时间以及封装机构的动作时间,是无法满足生产效率要求的,因而此工位需要设计双工位才能满足生产效率要求,其他工位在节拍分配上同理。在设计时,在理论上需要进行节拍的分配分析,图3为极耳焊接机段的时序图。
1.3 物流方式
电池在组装时,必然需要通过物流进行各工位上的流转和切换。因而需要对不同状态下的电芯进行合理的物流方式的选择。
①对于叠片机出料的裸电芯而言,为了保证电芯的输送效率以及保护电芯的安全性,常规以倍速链+电芯夹具的方式进行,倍速链具备输送效率高、适合长距离输送、负载大、维护简单等优点,且倍速链型材对于设置挡停以及其他辅助结构安装调节具有很大的灵活性。缺点在于倍速链容易摩擦产生粉尘,有个别厂家为了规避粉尘对电芯的影响,选用磁悬浮输送线进行裸电芯的输送,但是价格昂贵。
②电芯从叠片机输送过来进入焊接机,焊接机上的每个工位对电芯的定位精度有较高要求,电芯被装入焊接夹具内,采用步进式输送方式,为保证精度要求,驱动采用伺服电机+拨叉的循环结构。
③在电芯从焊接机下料后,一般采用伺服电机+同步带的输送方式,这样可保证电芯输送的等间距性,方便机械手的下料和上料抓取位置的准确性,同理,在包装机之后也采取同样的方式进行,经济且高效。
1.4 电芯定位方式及原则
在电芯组装线上,电池厂家在工艺上对电芯有一定的尺寸精度要求,因而在电池进组装线之前需要对电芯进行定位,以同一个基准进行电芯的定位,后面各工位的调整也以此为基准,以确保电芯组装的一致性。
电芯本体的形状为矩形,因而在定位形式上通常采用两边为定位基准,另外两边以推的方式进行电芯的定位。也可以采用电芯本体中心定位方式,前后左右同时进行推电芯本体,在定位方式的选择上一般取决于电芯的工艺尺寸要求,以及在结构设计上的便利性,只要保证基准一致即可。
1.5 粉尘控制
在电池生产过程中,最致命的危害莫过于金属粉尘进入电芯本体内,引发一系列的问题,如电池的短路起火等。为了避免这种情况的发生,需要对组装线段的粉尘产生源进行严格控制和尽可能清除,控制粉尘,首先得找出粉尘的产生源,然后进行针对性措施。
①叠片机输送线(倍速链)。由于在输送过程中,倍速链条会与倍速链型材摩擦产生较多粉尘,针对这类粉尘需要对倍速链线体加装防尘板,防止粉尘掉落到电芯上,同时电芯夹具尽可能采用上下包夹的方式进行输送,对于回流线体上的空夹具进行定点除尘,除尘方式采用吹+吸的方式进行,由于线体比较长,需要增大人工清洁频率,以防止粉尘堆积等。
②组装线。电池在组装线中进行流转时,有一些工位本身就能产生粉尘,比如极耳的预焊、裁切、Tab焊接、焊印压平等工位,只要存在裁切或者焊接的工位都会设置专门的除尘机构进行不间断的吸尘处理。
1.6 质量监控
为了电池生产质量的稳定性和一致性,在电池生产的各个环节都会有相应的检测传感器来进行质量控制。对于组装线来说,具体体现如下:
①通过颜色传感器对电芯来料的极性进行检测,主要是为了防止人工干预后的电池放反。
②电芯的扫码,保证电芯信息及时上传到MES系统中,便于电池生产的信息跟踪。
③电芯的X射线检测,用来检测电芯的对齐度,防止错位严重的电池往后接着生产。
④Tab片的极性检测以及正反检测,避免焊接错误。
⑤Tab焊接后的贴胶检测,避免后面封装时焊印直接接触铝塑膜。
⑥Tab焊接后的CCD尺寸检测,保证电芯生产的尺寸一致性。
⑦焊接后电芯的Hi-pot测试,确保焊接后的电芯两极无导通。
⑧铝塑膜纠偏控制,保证铝塑膜的冲坑良品率。
⑨封装后电池的CCD尺寸检测,保证电池外观尺寸的一致性。
⑩封装后电池的Hi-pot测试,确保封装后的电芯两极无导通。
⑪封装后电池的绝缘测试,确保封装后的电芯两极与铝塑膜之间无导通。
⑫封装后电池的封印厚度检测,确保封装后电池封印的一致性。
通过上述的一系列控制方式和点位,可以对电池在整个组装线上的质量进行有效控制。
设备主要功能及描述
锂电池是一类由锂金属或锂合金为负极材料,使用非水电解质溶液的电池。锂电池的主要构成为正负极、电解质、隔膜以及外壳。而软包锂电池是在液态锂离子电池上套上一层聚合物外壳的电池,采用铝塑复合膜包装。相比于圆柱电池和铝壳电池来说,电池的组成成分是一样的,只是包装形式和电池的物理结构形式不一样,从而导致了软包电池的装配形式以及生产工艺不一样,软包电池结构如图5所示。
图5 软包电池结构
软包电池装配线的生产工艺可以分为三大部分:第一部分为极耳焊接部分,第二部分为包装机部分,第三部分为冲坑机部分。软包电池主要工艺路线如图6所示。
图6 软包电池主要工艺路线
软包电池装配线主要技术指标如下:
①产品的合格率:≥99%。
②全线生产效率:依据产线要求而定。
③生产线需要操作人员:2人。
④整线设备稼动率:≥98%[计算公式(24h-故障时间-报警时间)/24×100%]。
⑤封装设备合格率:≥98.8%。
设备组成及关键结构
软包电池装配线主要由极耳焊接机、包装机、包装机后段等组成。
3.1 极耳焊接机
极耳焊接机是对接叠片机物流过来的裸电芯的铜箔、铝箔极耳进行收拢的超声波预焊,在对其进行导电柄的超声波终焊、焊印压平、除尘、贴胶等工序,为下一步入铝塑膜坑做封装准备。极耳焊接机的关键结构主要包含电芯极耳预焊、极耳裁切、电芯Tab片终焊、焊印整平及除尘、焊印贴胶等。
极耳焊接机是将叠片机过来的裸电芯进行极耳的预焊以及终焊,其关键结构有极耳裁切、极耳预焊、极耳Tab焊接、焊印除尘等。
极耳预焊主要是将电芯铜箔和铝箔极耳进行聚拢焊接,为终焊做准备工作。其机构组成部分为预焊机、焊机底座、聚拢机构、吸尘机构,极耳预焊结构如图7所示。
图7 极耳预焊结构图
1)极耳预焊
该结构的功能与动作用于实现极耳的超声波预焊接,焊机下焊头采用固定方式(焊头、焊座、底座的设计需要与客户沟通),电芯极耳到位后,气缸下压托盘夹具达到预焊工作高度,焊接同时进行吸尘处理;并在焊接时对极耳聚拢。在焊接的电芯有防护装置,防止焊渣掉入电芯。下焊头有吸尘罩,尘罩内有粉尘吸附装置,包括吹风装置和吸附粉尘装置,保证焊接粉尘能吸附干净;吸尘风速要求≥15m/s。
对于极耳预焊焊接位置精度,要求上下方向上偏差≤±0.2mm,左右方向偏差≤±0.2mm。
备注:焊接封装线需要根据焊机进行数据对接,能够采集焊接关键性参数(焊接参数包括能量、功率、时间、压力等),并能接收相关焊接异常信息,进行异常报警及电芯NG排出。
2)极耳裁切
图8 极耳裁切结构图
极耳裁切机构主要是将预焊后铜箔和铝箔极耳进切整齐。其主要由上下切刀、上下切刀导向机构、除尘机构、废料导槽、上气缸、下气缸等组成,极耳裁切结构如图8所示。
该结构用于实现正极耳预焊后的自动裁切。刀具采用SKD11镀类金刚砂膜防止粘刀,在设计时会采用一备一用的方式,根据客户要求也会对SKD11进行镶钨钢的处理。裁切位置调整处有数显千分尺,方便人工调节,裁切刀裁切到预焊焊印上。裁切后极耳长度可调范围:0~10mm;裁切精度:±0.1mm;裁切寿命要求:切刀单次使用次数≥30万次(20万次寿命提醒修磨),可反复修磨10次以上。切刀处有防尘罩,裁切时将裁切机构与外部环境隔离,防尘罩内有粉尘吸附装置,保证裁切废料与粉尘能吸附干净;吸尘风速要求≥15m/s;裁切机构内有接料盒,对裁切下的箔材进行收集。裁切压板有凸台设计,弹簧力可调,裁切前对保护片两侧进行压制,防止裁切后保护片翘曲对后段工序有影响。
3)极耳Tab终焊
极耳Tab终焊分为正/负极Tab上料机构和正/负极极耳主焊两部分。
①正/负极Tab上料机构。正/负极Tab上料机构的组成:由Tab弹匣式送料机构、伺服提升装置、Tab吸取机构、二次定位机构、弹匣机构检测传感器等组成,用于实现正负极Tab的自动上料。
正/负极Tab上料机构的主要功能是将Tab片导电柄与预焊裁切整齐的正负极耳焊接到一起的关键工序,在实际生产中,Tab片需要不断地进行上料,为了保证可以不停机换料,因而需要在机构设计上设计一个Tab片缓存机构。Tab片取料机械手需要具备旋转功能,可对Tab片的正反进行防呆处理。Tab片的极性检测,是为了检测正负极的极性,防止人工将正负极片放错。Tab片的定位机构,由于进行焊接时,电芯极耳与Tab片有相对的位置精度要求,根据客户要求对Tab进行定位,定位基准为Tab片两侧和PP胶或者Tab片四周。Tab片的送料机构,将定位好的Tab片夹持住送到终焊预定位置进行焊接,由于也有位置精度要求,驱动为伺服电机和滚珠丝杆的结构组合,从而保证精度要求。正/负极Tab上料机构如图9所示。
图9 正/负极Tab上料机构
正/负极Tab上料机构功能与动作如下:
a.弹匣机构上共有5个弹匣,正负极弹夹有颜色与标识区分,一个弹匣一次可装200片Tab,一次上料可连续工作2h以上。
b.Tab来料的尺寸精度:来料时人工将Tab放入弹夹内;电池采用毛刷、吹气以及电气抖动程序防止多片,合格率100%;采用检测导电柄位置来识别正反;正负极料夹用颜色区别。6个弹匣的转位由伺服完成,弹匣上料位有检测物料有无的感应器。采用伺服旋转,避免定位偏移太多引起极耳翘曲。
c.Tab定位,采用机械定位,定位导电夹短边与极耳胶。
d.夹取上料,采用手指气缸,最大面积夹持导电柄,避免导电柄滑动,伺服移载的方式实现精确送料,Tab定位精度为±0.2mm。
②正/负极极耳主焊。正/负极极耳主焊主要组成部分为超声波焊机、定位机构、检测系统、吸尘系统等。正/负极极耳主焊如图10所示。
图10 正/负极极耳主焊
正/负极极耳主焊用于实现正负极Tab的超声波焊接,该机构下焊头采用固定方式,Tab在电芯极耳上方焊接,焊机整体可水平调整,适应工艺要求。
正/负极极耳主焊技术特点如下:
a.焊头/底模单次使用寿命≥5万次,单面可反复修磨5次以上,极耳焊接层数兼容≤50层;焊头/底模以及底座的设计需与甲方沟通。
b.焊接后有检测极耳是否焊接导电柄装置,系统报警与电池NG装置。
c.焊接关键性参数(焊接参数包括能量、功率、时间、压力等)都可以设定上下限数值,具有在线检测、异常报警、电芯NG排除、预留导电柄上下焊接功能。
d.吸尘处理:在焊接的电芯侧有防护装置,防止焊渣掉入电芯。制作吸尘罩随焊头动作,在超声波焊接打开吸尘,吸尘风速20m/s,可以有效吸走金属粉屑。
e.精度:极耳定位精度±0.2mm;焊接位置精度为上下偏差±0.2mm,左右偏差±0.2mm。
f.焊接参数具有本地存储,具备与MES对接的接口功能。增加手动除尘口,焊接工位有焊接极耳有无检查、焊接后极耳检测功能。
4)极耳焊印除尘
极耳焊印的除尘对电芯的良品率以及电芯安全性能至关重要,主要原因在于超声波焊接过程属于机械摩擦焊,会产生很多金属粉尘,以及在焊印上很多尖锐毛刺在掉落的时候也会成为金属粉尘的一个来源。这些金属粉尘在进入电芯本体后会刺破正负极片中间的隔膜,导致电池短路引起起火等危险事故。
极耳除尘分为焊印压平机构和焊印二次除尘机构两个部分。
①焊印压平机构。焊印压平为在Tab片终焊接之后对焊印处进行冲压压平,其主要目的在于将超声波焊接后的极耳表面的焊印毛刺压平或者压掉,为焊印的二次除尘做好准备工作,在此机构上也有除尘吸口,对直接压掉下来易于吸走的焊渣进行除尘。
焊印压平机构由上气缸移动机构、下顶升机构、压块、吸尘罩等组成。主要用于实现极耳焊接后的整形,整形压力≥500N,压板材质PEEK。整形后无翘曲,整形位置可调,焊印压平机构如图11所示。
图11 焊印压平机构
②焊印二次除尘机构。焊印二次除尘的目的是对焊印处进行独立的除尘,将压平机构未清理掉的金属粉尘进行较为彻底的清除。
二次除尘机构主要由气缸移动机构、密封腔体、毛刷机构等组成。功能与动作:用清洁装置对焊接部位进行清洁,清洁后无大于50μm异物,并且有粉尘吸附装置,保证粉尘能清洁干净,吸尘风速≥20m/s,清洁过程不能二次污染电芯,且不损伤极耳。焊印二次除尘机构如图12所示。
图12 焊印二次除尘机构
焊印压平机构和二次除尘机构对焊印的处理,保证了后续工序的贴胶和封装时的平稳性以及热风融合性等。
5)极耳焊印贴胶及检测
极耳焊印贴胶是通过胶带将焊印进行贴住,保证后面进行封装时,避免焊印的凹凸不平直接接触铝塑膜,有刺破铝塑膜表面PP胶与铝层直接接触的风险。
极耳焊印贴胶及检测分为极耳焊印贴胶机构和极耳焊印贴胶检测机构两部分。
①极耳焊印贴胶机构。极耳焊印贴胶机构由胶纸送料机构、张紧机构、导向机构、自动裁切机构、吸取贴胶机构等组成。贴胶方式为上下分开贴,本贴胶机构分为上贴胶机构和下贴胶机构,上下贴胶的工作方式相同。胶带长度兼容≤100mm,宽度≤25mm。保证蓝胶完全遮住焊印、极耳底部边缘,贴胶整齐,不压住导电柄的PP胶。贴胶机构中蓝胶拉胶过程中由弹簧张力控制,保证贴胶完成后蓝胶不回弹、不折皱,贴合完整,吸胶头材质为硬质氧化处理过的A6061,不损伤极耳。可实现贴胶位置精度在±0.2mm,上下对齐度±0.2mm内,裁切精度±0.2mm。极耳焊印贴胶机构图如图13所示。
图13 极耳焊印贴胶机构
②极耳焊印贴胶检测机构。极耳焊印贴胶检测机构主要目的是检测电芯极耳焊印处的胶带有无以及对胶带进行压平。
贴胶检测机构主要由气缸、压块、探针等组成。焊印贴胶检测机构如图14所示。
图14 焊印贴胶检测机构
经过极耳焊印贴胶机构和贴胶检测机构对焊印的处理,有效规避了焊印对铝塑膜封装的影响。
(2)铝塑膜冲坑机
铝塑膜冲坑机是铝塑膜卷料进行主动放卷,并有序地在铝塑膜上进行冲出满足电池尺寸的铝塑膜坑。铝塑膜冲坑机的关键结构主要包含放卷纠偏机构、切缝机构、冲坑机构、裁切机构等。
①放卷纠偏机构。放卷纠偏机构是铝塑膜冲坑机的最前段机构,承担设备铝塑膜的上料、换料、放卷铝塑膜以及在正常工作过程中对铝塑膜进行实时的纠偏处理。
放卷纠偏机构由气胀轴、卷料铝塑膜定位机构、主动开卷机构(含电机、减速机等)、张力控制系统、接料平台、纠偏系统等组成。功能与动作:通过人工上料,料卷气缸定位,光电传感器检测料有无;具有人工接带平台,人工接料平台包括铝塑膜裁切刀、接带压板等,接带平台下方具有负压吸尘装置;铝塑膜通过张力控制器+磁粉制动器进行铝塑膜张力调节,保持铝塑膜张力和导入方向的恒定;具有双放卷结构,实现短时间停机作业,保证整条线体的时效性。放卷纠偏机构如图15所示。
图15 放卷纠偏机构
放卷纠偏机构的相关精度参数如下:
张力范围:0~100N;
张力控制精度:±3N;
卷径检测:检测范围≥400mm,检测精度要求±0.1mm。
为了保证铝塑膜在转运的过程中避免损伤,对过辊进行了特殊处理和加工。过辊材质:黑色硬质氧化的铝合金A6061,其镀层厚度大于4μm,过辊表面粗糙度为Ra0.8,使用寿命可达3年以上(保证设备使用效率、稼动率和产品合格率的前提下),辊轴轴承使用摩擦系数低的轴承,尽量减小转动阻力。
②切缝机构。切缝机构主要由直线轴承、立柱、气缸、裁刀、裁刀固定板等组成。其主要的功能与动作如下:冲坑前,用于对两张铝塑膜中间切缝释放应力,裁刀采用美工刀片,便于采购与备料,拉料到位,平台吸真空打开,上气缸驱动裁切机构切缝,裁切机构有吸尘罩,裁切过程中吸尘罩将裁切部位切口的粉尘进行负压吸附,保证裁切废料与粉尘可以吸附干净;吸尘风速要求≥15m/s;预裁位置精度0.3mm;裁切长度调整范围可根据需要进行选择。切缝机构如图16所示。
图16 切缝机构
切缝机构通过在铝塑膜上进行划缝之后,为铝塑膜冲坑做准备。
③冲坑机构。冲坑机构主要由冲壳模具、伺服电机、减速机、滚珠丝杆、气缸、导向轴等组成。
冲坑机构采用多个气缸进行压紧铝塑膜的动作,由伺服电机驱动滚珠丝杆进行冲坑,深度可自由通过软件设定,设定范围2~12mm。铝塑膜的压紧力通过伺服调节,模具有冲裁定位孔功能,采用双坑冲壳的方式,冲壳尺寸精度可控制在±0.1mm内,定位销孔采用气缸冲孔,冲孔精度±0.1mm,销孔废料从下模具板两边排出,设备冲壳模具两侧配备光栅(垂直于走带方向),检测到异物报警并停机,维护设置有安全防护的功能,防止维修人员被模具伤害。
对冲坑机构具有换模需求,因而每台冲坑机会配做一台模具小车以方便换模具。
冲坑机构使用次数多,因此材料选择很关键,主要有以下几种材料类型:底板45#调质+镀镍,顶板45#调质+镀镍,主立柱45#调质+镀铬,上模板SKD11+淬火+氮化,凹模SKD11+淬火+氮化,凸模KD11+淬火+氮化,凸模固定板45#+镀镍。冲坑机构如图17所示。
图17 冲坑机构
④裁切机构。裁切机构主要由导杆、切刀、切刀固定座、上气缸、下气缸、除尘机构等组成。其功能与动作是用于对铝塑膜定长分切,裁切时设有除尘装置。裁切刀一般使用寿命可达30万~50万次(同时具备寿命提醒报警),可修磨10次以上。在裁切时对刃口进行吸尘处理。吸尘风速要求≥20m/s,铝塑壳裁切精度为±0.2mm。裁切机构如图18所示。
图18 裁切机构
(3)包装机
包装机是将极耳焊接机焊接好的电芯与冲坑机冲压好的铝塑膜组装成一个初步的电池形态。包装机的关键结构主要包含包装机夹具、对折机构、裁切机构、顶/侧封机构等。
①包装机夹具。包装机夹具是铝塑膜与电芯组装在一起完成各工序的重要载体,由齿轮齿条、角轴承、上形腔、下型腔、吸盘、定位块等组成。其工作原理为下型腔固定在支架上,并合理分布真空吸盘;上型腔由夹具翻转机构通过齿轮齿条翻转,可实现开、合、保持三位置要求,并合理分布真空吸盘;铝膜放入型腔后,真空吸盘工作,铝膜位置确定,在各工位流转中铝膜位置不变。由于铝塑膜是软体,为了保证铝塑膜坑很好地与电芯之间的相对尺寸位置,对于上、下型腔采用仿形电芯外形尺寸的方式进行加工,加工精度可以达到±0.2mm,为了使夹具尽量轻量化且能够保证强度要求,材质一般选用A6061并做表面氧化处理,经久耐用,对折后铝膜边缘对齐度±0.2mm。包装机夹具如图19所示。
图19 包装机夹具
通常夹具机构配有三位置检测磁性开关,实时检测上型腔位置。
②对折机构。对折机构主要由升降气缸、进退气缸、直线导轨、对折板等组成。其主要功能与动作为升降气缸保持在顶部位置,进退伺服将对折板推入铝膜折线正上方,升降气缸下行压紧铝膜,此时对折板边线与铝膜折线重合;转盘夹具闭合,进退气缸将对折板拉出,铝膜完全对折,转至下一工位;此时,铝塑膜内没有电芯,对折机构的整体精度可达到±0.2mm。对折机构如图20所示。
图20 对折机构
③裁切机构。裁切机构主要是用于对包装机上的铝塑膜进行裁切,主要由上切刀驱动气缸、下切刀驱动气缸、上切刀、下切刀、压紧机构、直线导轨、除尘机构、调压阀等组成,裁切位置有千分尺,方便人工调节。功能与动作为转盘转一工位,下气缸动作,下刀顶升,上气缸动作,弹簧压板接触铝塑膜后裁切铝塑膜,气缸同时复位。裁切机构如图21所示。
图21 裁切机构
裁切机构的下裁切机构内有接料盒,对裁切下的铝塑膜进行收集,裁切机构有防尘罩,裁切过程中防尘罩将裁切部位与外部环境隔离,防尘罩内有粉尘废料吸附装置,包括吹风装置与负压除尘装置,保证裁切废料与粉尘可以吸附干净;吸尘风速要求≥20m/s;顶边裁切精度≤0.2mm;裁切后顶边对齐度≤0.2mm;切刀寿命为单次寿命30万~50万次(系统具备寿命提醒磨刀),可修模次数≥10次;使用数显千分尺,保证调节精度0.01mm。
④顶/侧封机构。顶/侧封机构主要是用于电池的顶封或者侧封,主要由伺服电机、滚珠丝杆、直线导轨、缓冲机构、极耳定位机构、微调机构、NAK80封头、温控器、发热管、热电偶等组成。功能与动作为封头采用电加热方式升温,封头温度为室温至250℃可调,设备运行时封头整体温度偏差小于±3℃,发热管功率为1500W,发热管使用寿命为1年,温控调节精度为≤5℃;从室温升温至200℃所需时间小于10min;封头加热座采用隔热板密封温度补偿的设计,保证高速封印过程中温度在要求范围内,电芯旋转至本工位后,上、下伺服电机同时驱动滚珠丝杆带动上、下封头闭合,进行热封,封印压力调节范围为0~20kgf/cm2;封头预留有极耳槽;电池主体与封头的间隙可调,调节处有数显千分尺。封装时间为0~8s可调,调整精度0.1s;极耳区封印精度±20μm,非极耳区封印精度±15μm。顶/侧封机构如图22所示。
图22 顶/侧封机构
-
锂电池
+关注
关注
256文章
7684浏览量
163394 -
制程
+关注
关注
1文章
87浏览量
16169 -
电芯
+关注
关注
14文章
675浏览量
25290
发布评论请先 登录
相关推荐
扩展模块驱动分布式I/O在新能源锂电池自动化生产中的发展
4680汽车锂电池溯源:晨控大圆柱RFID电池托杯的功能与优点
大圆柱电芯在PACK应用中的轻量化解决方案
锂电池制程工艺及磷酸铁锂(LFP)三元(NCM)锂电池的区别及发展趋势
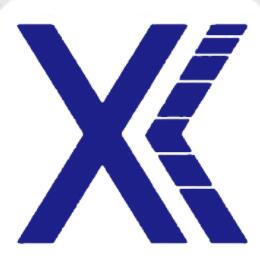
评论