摘要:随着功率器件特别是第三代半导体的崛起与应用,半导体器件逐渐向大功率、小型化、集成化、多功能等方向发展,对封装基板性能也提出了更高要求。陶瓷基板(又称陶瓷电路板)具有热导率高、耐热性好、热膨胀系数低、机械强度高、绝缘性好、耐腐蚀、抗辐射等特点,在电子器件封装中得到广泛应用。本文分析了常用陶瓷基片材料(包括Al2O3、AlN、Si3N4、BeO、SiC和BN等)的物理特性,重点对各种陶瓷基板(包括薄膜陶瓷基板TFC、厚膜印刷陶瓷基板TPC、直接键合陶瓷基板DBC、直接电镀陶瓷基板DPC、活性金属焊接陶瓷基板AMB、激光活化金属陶瓷基板LAM以及各种三维陶瓷基板等)的制备原理、工艺流程、技术特点和具体应用等进行了论述,最后对电子封装陶瓷基板发展趋势进行了展望。
第一代半导体以硅 (Si)、锗 (Ge) 材料为代表,主要应用在数据运算领域,奠定了微电子产业基础。第二代半导体以砷化镓 (GaAs)、磷化铟 (InP) 为代表,主要应用于通信领域,用于制作高性能微波、毫米波及发光器件,奠定了信息产业基础。随着技术发展和应用需要的不断延伸,二者的局限性逐渐体现出来,难以满足高频、高温、高功率、高能效、耐恶劣环境以及轻便小型化等使用需求。
以碳化硅 (SiC) 和氮化镓 (GaN) 为代表的第三代半导体材料具有禁带宽度大、临界击穿电压高、热导率高、载流子饱和漂移速度大等特点,其制作的电子器件可在 300°C 甚至更高温度下稳定工作 (又称为功率半导体或高温半导体),是固态光源 (如 LED)、激光器 (LD)、电力电子 (如IGBT)、聚焦光伏 (CPV)、微波射频 (RF) 等器件的“核芯”,在半导体照明、汽车电子、新一代移动通信 (5G)、新能源与新能源汽车、高速轨道交通、消费类电子等领域具有广阔的应用前景,有望突破传统半导体技术瓶颈,与第一代、第二代半导体技术互补,在光电器件、电力电子、汽车电子、航空航天、深井钻探等领域具有重要应用价值,对节能减排、产业转型升级、催生新经济增长点将发挥重要作用。
伴随着功率器件 (包括 LED、LD、IGBT、CPV 等) 不断发展,散热成为影响器件性能与可靠性的关键技术。对于电子器件而言,通常温度每升高 10°C,器件有效寿命就降低 30% ~ 50%。因此,选用合适的封装材料与工艺、提高器件散热能力就成为发展功率器件的技术瓶颈。以大功率 LED 封装为例,由于输入功率的 70% ~ 80% 转变成为热量 (只有约 20% ~ 30% 转化为光能),且 LED 芯片面积小,器件功率密度很大 (大于 100 W/cm2),因此散热成为大功率 LED 封装必须解决的关键问题。如果不能及时将芯片发热导出并消散,大量热量将聚集在 LED 内部,芯片结温将逐步升高,一方面使 LED 性能降低 (如发光效率降低、波长红移等),另一方面将在 LED 器件内部产生热应力,引发一系列可靠性问题 (如使用寿命、色温变化等)。
封装基板主要利用材料本身具有的高热导率,将热量从芯片 (热源) 导出,实现与外界环境的热交换。对于功率半导体器件而言,封装基板必须满足以下要求:
(1) 高热导率。目前功率半导体器件均采用热电分离封装方式,器件产生的热量大部分经由封装基板传播出去,导热良好的基板可使芯片免受热破坏。
(2) 与芯片材料热膨胀系数匹配。功率器件芯片本身可承受较高温度,且电流、环境及工况的改变均会使其温度发生改变。由于芯片直接贴装于封装基板上,两者热膨胀系数匹配会降低芯片热应力,提高器件可靠性。
(3) 耐热性好,满足功率器件高温使用需求,具有良好的热稳定性。
(4) 绝缘性好,满足器件电互连与绝缘需求。
(5) 机械强度高,满足器件加工、封装与应用过程的强度要求。
(6) 价格适宜,适合大规模生产及应用。
目前常用电子封装基板主要可分为高分子基板、金属基板 (金属核线路板,MCPCB) 和陶瓷基板几类。对于功率器件封装而言,封装基板除具备基本的布线 (电互连) 功能外,还要求具有较高的导热、耐热、绝缘、强度与热匹配性能。因此,高分子基板 (如 PCB) 和金属基板 (如 MCPCB) 使用受到很大限制;而陶瓷材料本身具有热导率高、耐热性好、高绝缘、高强度、与芯片材料热匹配等性能,非常适合作为功率器件封装基板,目前已在半导体照明、激光与光通信、航空航天、汽车电子、深海钻探等领域得到广泛应用。
本文主要介绍几种常用陶瓷基板及其制备方法,并对陶瓷基板技术和发展趋势进行了展望。
01 陶瓷基片材料
作为封装基板,要求陶瓷基片材料具有如下性能:
(1) 热导率高,满足器件散热需求;
(2) 耐热性好,满足功率器件高温 (大于 200°C) 应用需求;
(3) 热膨胀系数匹配,与芯片材料热膨胀系数匹配,降低封装热应力;
(4) 介电常数小,高频特性好,降低器件信号传输时间,提高信号传输速率;
(5) 机械强度高,满足器件封装与应用过程中力学性能要求;
(6) 耐腐蚀性好,能够耐受强酸、强碱、沸水、有机溶液等侵蚀;
(7) 结构致密,满足电子器件气密封装需求;
(8) 其他性能要求,如对于光电器件应用,还对陶瓷基片材料颜色、反光率等提出了要求。
目前,常用电子封装陶瓷基片材料包括氧化铝 (Al2O3)、氮化铝 (AlN)、氮化硅 (Si3N4 )、氧化铍 (BeO)等。下面分别介绍其性能与技术特点。
1.1 氧化铝 (Al2O3)
氧化铝陶瓷呈白色,热导率为 20 W/(m·K) ~ 30 W/(m·K),25°C ~ 200°C 温度范围内热膨胀系数为 7.0×10-6/°C ~8.0×10-6/°C,弹性模量约为 300GPa,抗弯强度为 300MPa~400MPa,介电常数为10,其粉料与样品如图 1 所示。
图1 (a) Al2O3 陶瓷粉末和 (b) Al2O3 陶瓷基片
氧化铝陶瓷基片成型方法主要有轧膜法、流延法和凝胶注膜法等。其中后两种方法采用去离子水代替有机溶剂,既可降低成本,也有利于环保,是 Al2O3陶瓷片制备主要研究方向之一。
由于Al2O3 晶格能较大,离子键较强,因此烧结温度较高,95%Al2O3 陶瓷烧结温度为 1650°C~1700°C,99% Al2O3 陶瓷烧结温度则高达 1800°C。如此高的烧结温度不仅导致制作成本偏高,而且所得到的产品晶粒粗大,气孔难以排除,导致Al2O3 陶瓷气孔率增加,力学性能降低。
研究表明,在原料中加入适量添加剂可降低烧结温度,降低陶瓷气孔率,提高陶瓷材料致密性与热导率。常用添加剂有生成液相型燃烧助剂 (如 Si、CaO、SrO 和 BaO 等碱金属氧化物)、生成固溶体型烧结助剂 (如 TiO2、MnO2、Fe2O3和Cr2O3等) 以及稀土烧结助剂 (如 Y2O3、La2O3、Sm2O3 以及 Nd2O3 等稀土氧化物)。
根据 Al2O3 粉料与添加剂的不同含量,可将 Al2O3陶瓷分为 75 瓷、85 瓷、96 瓷、99 瓷等不同牌号。
氧化铝陶瓷具有原料来源丰富、价格低廉、绝缘性高、耐热冲击、抗化学腐蚀及机械强度高等优点,是一种综合性能较好的陶瓷基片材料,占陶瓷基片材料总量的 80% 以上。但由于其热导率相对较低 (99% 氧化铝热导率约为 30 W/(m·K),热膨胀系数较高,一般应用在汽车电子、半导体照明、电气设备等领域。
1.2 氮化铝 (AlN)
氮化铝材料呈灰白色 (如图 2 所示),属于六方晶系,是以 [AlN4] 四面体为结构单元的纤锌矿型共价键化合物。该结构决定了其具有优良的热学、电学和力学性能。AlN 陶瓷理论热导率可达320 W/(m·K),其商用产品热导率一般为 180 W/(m·K) ~260 W/(m·K),25°C~200°C 温度范围内热膨胀系数为 4×10-6/°C (与 Si 和 GaAs 等半导体芯片材料基本匹配),弹性模量为 310 GPa,抗弯强度为 300 MPa ~ 340 MPa,介电常数为 8~10。
图 2 (a) AlN 陶瓷粉末和 (b) AlN 陶瓷基片
AlN 陶瓷烧结同样需要烧结助剂来改善性能,提高质量。常用助烧剂有Y2O3、CaO、Li2O、BaO、MgO、SrO、La2O3 、HfO2和 CeO2 等 。
助烧剂的主要作用有两方面:一是形成低熔点物相,实现液相烧结进而降低烧结温度;二是与晶格中的杂质氧发生反应,使晶格完整化,进而提高陶瓷性能。一般而言,二元或多元烧结助剂往往可以获得更好的烧结效果。助烧剂加入方式有两种,一是直接添加,另一种是以可溶性硝酸盐形式制成前驱体原位生产烧结助剂。
传统 AlN 陶瓷成型方法有模压、等静压和热压等,但这些方法生产周期长、效率低、制品各方向受力不均匀,无法满足电子封装需求。近年来业界逐步开发了流延成型、注凝成型、注射成型等工艺。其中,流延法主要适用于制备片状产品,分为有机和无机体系。相对而言,有机流延体系具有溶剂选择范围广、干燥时间短、防止粉体水化等特点,但常用的醇、酮及苯等有机溶剂具有一定毒性,生产受到一定限制。
因此,目前行业内主要采用水基流延成型法,但也存在坯体干燥易起泡和变形、烧结易开裂以及制品表面不光滑等问题。氮化铝陶瓷热导率为氧化铝陶瓷的 6~8 倍,但热膨胀系数只有其 50%,此外还具有绝缘强度高、介电常数低、耐腐蚀性好等优势。除了成本较高外,氮化铝陶瓷综合性能均优于氧化铝陶瓷,是一种非常理想的电子封装基片材料,尤其适用于导热性能要求较高的领域。
1.3 氮化硅陶瓷 (Si3N4)
Si3N4 具有三种晶体结构,分别是 α 相、β 相和 γ 相 (其中 α 与 β 相是最常见形态),均为六方结构,其粉料与基片呈灰白色,如图 3 所示。Si3N4 陶瓷基片弹性模量为 320 GPa,抗弯强度为 920 MPa,热膨胀系数仅为 3.2 ×10-6/°C,介电常数为 9.4,具有硬度大、强度高、热膨胀系数小、耐腐蚀性高等优势。
由于 Si3N4陶瓷晶体结构复杂,对声子散射较大,因此早期研究认为其热导率低 ,如Si3N4轴承球、结构件等产品热导率只有 15 W/(m·K) ~ 30 W/(m·K)。1995 年,Haggerty 等人通过经典固体传输理论计算表明,Si3N4材料热导率低的主要原因与晶格内缺陷、杂质等有关,并预测其理论值最高可达 320 W/(m·K)。
之后,在提高Si3N4材料热导率方面出现了大量的研究,通过工艺优化,氮化硅陶瓷热导率不断提高,目前已突破 177 W/(m·K)。
图 3 (a) 氮化硅陶瓷粉末和 (b) 氮化硅陶瓷基片
陶瓷传热机制同样为声子传热。晶格中的杂质往往伴随着空位、位错等结构缺陷,降低了声子平均自由程,导致热导率降低,因此制备高纯粉体是制备高热导率 Si3N4 陶瓷的关键。
目前,市场上商用Si3N4粉料制备方法主要有两种,分别为硅粉直接氮化法及硅亚胺热解法。前者工艺较成熟,生产成本低,因此国内外大多数企业使用该法来生产 Si3N4粉料。但该方法所生产的 Si3N4粉料含有Fe、Ca、Al 等杂质,虽然可以通过酸洗去除,但大大增加了生产成本。后者可制备出具有较高烧结活性的Si3N4粉料,不含金属杂质元素,粒径分布在 0.2 μm~1 μm,且产量巨大,但技术难度较高。
Si3N4 陶瓷烧结助剂一般为金属氧化物、稀土氧化物或二者的混合物。Zhou 等人 采用Y2O3-MgO 烧结助剂制备出氮化硅热导率高达 177 W/(m·K),这是目前为止报道的 Si3N4 陶瓷最高热导率。
但是,氧化物烧结助剂会在 Si3N4 晶体中引入氧原子,导致热导率降低。采用非氧化物烧结助剂可减少氧含量,对于净化 Si3N4 晶格、减少晶界玻璃相、提高热导率及高温力学性能具有重要意义。
梁振华等人分别以MgSiN2 和MgSiN2 与Y2O3 混合物作为烧结助剂,在相同条件下制备 Si3N4 陶瓷,前者热导率为 90 W/(m·K),而后者仅为70 W/(m·K)。Hayashi 等人以 Yb2O3-MgSiN2 和Yb2O3-MgO作为烧结助剂,在相同条件下制备 Si3N4 陶瓷,结果发现前者热导率更高。
Si3N4 陶瓷烧结方法主要有反应烧结、常压烧结、热压烧结和放电等离子烧结等。反应烧结具有线收缩率低、成本低等优点,但其致密度低、力学性能差、热导率低。常压烧结与热压烧结制备的 Si3N4 陶瓷具有较好的机械性能,但热导率偏低,成本较高。气压烧结是指在烧结过程中施加压力约为 1 MPa ~ 10 MPa 的气体 (通常为 N2 ) 以抑制Si3N4 分解,促进粉料致密化,获得高密度产品。
放电等离子烧结是一种通过压力场、温度场和电流场等效应烧结制备陶瓷的新技术。在现有可作为基板材料使用的陶瓷材料中,Si3N4陶瓷抗弯强度高 (大于 800 MPa),耐磨性好,是综合机械性能最好的陶瓷材料,同时其热膨胀系数最小,因而被认为是一种很有潜力的功率器件封装基片材料。但是其制备工艺复杂,成本较高,热导率偏低,主要适合应用于强度要求较高但散热要求不高的领域。
1.4 氧化铍 (BeO)
BeO 材料密度低,具有纤锌矿型和强共价键结构,其粉末与基片均为白色,如图 4 所示。BeO相对分子量较低,导致材料热导率高,如纯度为 99% 的 BeO 陶瓷室温热导率可达 310 W/(m·K);其禁带宽度高达 10.6 eV,介电常数为 6.7,弹性模量为 350 GPa,抗弯强度为 200 MPa,具有良好的综合性能。
图 4 (a) BeO 陶瓷粉末和 (b) BeO 陶瓷基片
但是,BeO 材料也存在一些不足,包括:(1) BeO 粉体具有毒性,人体大量吸入后将导致急性肺炎,长期吸入会引起慢性铍肺病,因此在生产过程中要采用特殊防护措施;(2) BeO 烧结温度高达1900°C 以上,生产成本高;(3) 热导率随着温度升高而降低,如在 0°C ~ 600°C 温度范围内,BeO陶瓷平均热导率为 206.67 W/(m·K),但当温度升高到 800°C 时,其热导率降低为十分之一,上述原因限制了氧化铍的推广应用。
但在某些大功率、高频半导体器件以及航空电子设备和卫星通讯中,为了追求高导热和理想高频特性,仍在采用 BeO 陶瓷基片。目前,美国是全球主要的 BeO 陶瓷基板生产和消费国,福特和通用等汽车公司在点火装置中大量使用 BeO 陶瓷基板。
1.5 其它陶瓷基片材料
除了上述陶瓷材料外,碳化硅 (SiC)、氮化硼 (BN) 等也都可作为陶瓷基片材料。其中,SiC 单晶材料室温热导率可达 490 W/(m·K),但 SiC 多晶体热导率仅为 67 W/(m·K)。此外,SiC 材料介电常数为 40,是 AlN 陶瓷的 4 倍,限制了其高频应用。BN 材料具有较好的综合性能,但作为基片材料,它没有突出优点,且价格昂贵,与半导体材料热膨胀系数也不匹配,目前仍处于研究中。SiC和 BN 陶瓷基板如图 5 所示。
图 5 (a) SiC 陶瓷基片和 (b) BN 陶瓷基片
表 1 对几种常用的陶瓷基片材料性能进行了对比。
表 1 常用陶瓷基片材料性能
02 陶瓷基板制备技术
陶瓷基板又称陶瓷电路板,包括陶瓷基片和金属线路层。对于电子封装而言,封装基板起着承上启下,连接内外散热通道的关键作用,同时兼有电互连和机械支撑等功能。陶瓷具有热导率高、耐热性好、机械强度高、热膨胀系数低等优势,是功率半导体器件封装常用的基板材料。根据封装结构和应用要求,陶瓷基板可分为平面陶瓷基板和三维陶瓷基板两大类。
2.1 平面陶瓷基板
根据制备原理与工艺不同,平面陶瓷基板可分为薄膜陶瓷基板 (Thin Film Ceramic Substrate,TFC)、厚膜印刷陶瓷基板 (Thick Printing Ceramic Substrate, TPC)、直接键合铜陶瓷基板 (Direct Bonded Copper Ceramic Substrate, DBC)、活性金属焊接陶瓷基板 (Active Metal Brazing Ceramic Substrate, AMB)、直接电镀铜陶瓷基板 (Direct Plated Copper Ceramic Substrate, DPC) 和激光活化金属陶瓷基板 (Laser Activated Metallization Ceramic Substrate, LAM) 等。
薄膜陶瓷基板 (TFC)
薄膜陶瓷基板一般采用溅射工艺直接在陶瓷基片表面沉积金属层。如果辅助光刻、显影、刻蚀等工艺,还可将金属层图形化制备成线路,如图 6 所示。由于溅射镀膜沉积速度低 (一般低于 1 μm/h),因此 TFC 基板表面金属层厚度较小 (一般小于 1 μm),可制备高图形精度 (线宽/线距小于 10 μm) 陶瓷基板,主要应用于激光与光通信领域小电流器件封装。
图 6 薄膜陶瓷基板 (TFC) 产品
厚膜印刷陶瓷基板 (TPC)
通过丝网印刷将金属浆料涂覆在陶瓷基片上,干燥后经高温烧结 (温度一般在 850°C ~ 900°C) 制备 TPC 基板,其工艺流程如图 7 所示。
图 7 TPC 基板制备工艺流程图
根据金属浆料粘度和丝网网孔尺寸不同,制备的金属线路层厚度一般为 10 μm~20 μm (提高金属层厚度可通过多次丝网印刷实现)。TFC 基板制备工艺简单,对加工设备和环境要求低,具有生产效率高、制造成本低等优点。但是,由于丝网印刷工艺限制,TFC 基板无法获得高精度线路 (最小线宽/线距一般大于 100 μm)。此外,为了降低烧结温度,提高金属层与陶瓷基片结合强度,通常在金属浆料中添加少量玻璃相,这将降低金属层电导率和热导率。因此 TPC 基板仅在对线路精度要求不高的电子器件 (如汽车电子) 封装中得到应用。TPC 基板样品及其截面图如图 8 所示。
图 8 (a) TPC 基板产品及其 (b) 截面图
目前 TPC 基板关键技术在于制备高性能金属浆料。金属浆料主要由金属粉末、有机载体和玻璃粉等组成。浆料中可供选择的导体金属有 Au、Ag、Ni、Cu 和 Al 等。银基导电浆料因其具有较高的导电、导热性能及相对低廉的价格而应用广泛 (占金属浆料市场 80% 以上份额 )。研究表明,银颗粒粒径、形貌等对导电层性能影响很大。如Park等人通过加入适量纳米银颗粒降低了银浆电阻率;Zhou等人指出金属层电阻率随着球状银颗粒尺寸减小而降低,片状银粉(尺寸 6 μm)制备的金属浆料电阻率远小于同样尺寸球状银粉制备的浆料。
金属浆料中有机载体决定了浆料的流动性、润湿性和粘接强度,从而直接影响丝网印刷质量以及后期烧结成膜的致密性和导电性。尹海鹏等人指出,当有机载体中纤维素含量为 1% ~ 4%时,加入少量氢化蓖麻油可降低有机载体剪切强度,有利于浆料印刷和流平。
加入玻璃料可降低金属浆料烧结温度,降低生产成本和基板应力。目前商用低温玻璃料几乎都含有铅元素,对环境和人体造成伤害。Chen 等人采用Bi2O3-SiO2-B2O3-Al2O3-ZnO系纳米玻璃粉制备金属银浆,用于太阳能电池电极制造,研究发现该浆料具有良好的润湿性和结合强度,光伏电池光电转换效率提高。
直接键合陶瓷基板 (DBC)
DBC 陶瓷基板制备首先在铜箔 (Cu) 和陶瓷基片 (Al2O3 或 AlN) 间引入氧元素,然后在 1065°C 形成 Cu/O 共晶相 (金属铜熔点为 1083°C),进而与陶瓷基片和铜箔发生反应生成 CuAlO2 或 Cu(AlO2)2,实现铜箔与陶瓷间共晶键合,其制备工艺和产品分别如图 9 和图 10 所示。由于陶瓷和铜具有良好的导热性,且铜箔与陶瓷间共晶键合强度高,因此 DBC 基板具有较高的热稳定性,已广泛应用于绝缘栅双极二极管 (IGBT)、激光器(LD)和聚焦光伏(CPV)等器件封装散热中。
图9 DBC陶瓷基板制备工艺流程
图10 DBC陶瓷基板产品
DBC 基板铜箔厚度较大 (一般为100 μm ~ 600μm),可满足高温、大电流等极端环境下器件封 装应用需求(为降低基板应力与翘曲,一般采用Cu-Al2O3-Cu 的三明治结构,且上下铜层厚度相同)。
虽然DBC基板在实际应用中有诸多优势,但在制备过程中要严格控制共晶温度及氧含量,对设备和工艺控制要求较高,生产成本也较高。此外,由于厚铜刻蚀限制,无法制备出高精度线路层。
在DBC基板制备过程中,氧化时间和氧化温度是最重要的两个参数。铜箔经预氧化后,键合界面能形成足够CuxOy相润湿Al2O3陶瓷与铜箔,具有较高的结合强度;若铜箔未经过预氧化处理,CuxOy 润湿性较差,键合界面会残留大量空洞和缺陷,降低结合强度及热导率。对于采用AlN陶瓷制备DBC基板,还需对陶瓷基片进行预氧化,先生成Al2O3薄膜,再与铜箔发生共晶反应。谢建军等人用DBC技术制备Cu/Al2O3、Cu/AlN陶瓷基板,铜箔和AlN陶瓷间结合强度超过8N/mm,铜箔和AlN间存在厚度为2μm的过渡层,其成分主要为Al2O3、CuAlO2和Cu2O。
活性金属焊接陶瓷基板 (AMB)
AMB陶瓷基板利用含少量活性元素的活性金属焊料实现铜箔与陶瓷基片间的焊接,其工艺流程如图11所示。
图11 AMB陶瓷基板制备工艺流程
活性焊料通过在普通金属焊料中添加Ti、Zr、Hf、 V、Nb 或 Ta等稀土元素制备,由于稀土元素具有高活性,可提高焊料熔化后对陶瓷的润湿性,使 陶瓷表面无需金属化就可与金属实现焊接。AMB基板制备技术是DBC基板工艺的改进(DBC基板 制备中铜箔与陶瓷在高温下直接键合,而AMB基板采用活性焊料实现铜箔与陶瓷基片间键合),通过选用活性焊料可降低键合温度(低于800°C),进而降低陶瓷基板内部热应力。此外,AMB基板依靠活性焊料与陶瓷发生化学反应实现键合,因此结合强度高,可靠性好。但是该方法成本较高,合适的活性焊料较少,且焊料成分与工艺对焊接质量影响较大,目前只有少数国外企业掌握了AMB基板量产技术,其样品与截面结构如图12所示。
目前,制备活性焊料是AMB基板制备关键技术。活性焊料的最初报道是1947年Bondley采用TiH2活性金属法连接陶瓷与金属,在此基础上,Bender等人提出Ag-Cu-Ti活性焊接法。活性焊料主要分为高温活性焊料(活性金属为Ti、V和Mo等,焊接温度1000°C~1250°C)、中温活性焊料(活性金属为 Ag-Cu-Ti,焊接温度 700°C ~ 800°C,保护气体或真空下焊接) 和低温活性焊料(活性金属为Ce、Ga和Re,焊接温度200°C~300°C)。中高温活性焊料成分简单,操作容易,焊接界面 机械强度高,在金属-陶瓷焊接中得到广泛应用。Naka等人分别采用Cu60Ti34活性焊料焊接Si3N4 陶瓷和NiTi50活性焊料焊接SiC,前者室温下焊接界面剪切强度达到313.8MPa,而后者在室温、300°C和700°C时的焊接界面剪切强度分别为158MPa、316MPa和260MPa。
图 12 (a) AMB 陶瓷基板产品及其 (b)截面图
由于DBC陶瓷基板制备工艺温度高,金属-陶瓷界面应力大,因此AMB技术越来越受到业界 关注,特别是采用低温活性焊料。如Chang等人使用Sn3.5Ag4Ti(Ce,Ga)活性焊料在250°C下分别 实现了ZnS-SiO2、ITO陶瓷以及Al2O3陶瓷与Cu层焊接;Tsao等人使用Sn3.5Ag4Ti(Ce)活性焊 料实现了Al 与微亚弧氧化铝 (MAO-Al)间焊接。
直接电镀陶瓷基板 (DPC)
DPC 陶瓷基板制备工艺如图 13所示。首先利用激光在陶瓷基片上制备通孔(孔径一般为60μm~120μm),随后利用超声波清洗陶瓷基片;采用磁控溅射技术在陶瓷基片表面沉积金属种子层(Ti/Cu),接着通过光刻、显影完成线路层制作;采用电镀填孔和增厚金属线路层,并通过表面处理提高基板可焊性与抗氧化性,最后去干膜、刻蚀种子层完成基板制备。
图13 DPC陶瓷基板制备工艺流程
从图 13 可以看出,DPC 陶瓷基板制备前端采用了半导体微加工技术(溅射镀膜、光刻、显影等), 后端则采用了印刷线路板 (PCB) 制备技术 (图形电镀、填孔、表面研磨、刻蚀、表面处理等),技术优势明显。
具体特点包括:(1) 采用半导体微加工技术,陶瓷基板上金属线路更加精细 (线宽/线距可低至30μm~50μm,与线路层厚度相关),因此DPC基板非常适合对准精度要求较高的微电子器件封装;(2) 采用激光打孔与电镀填孔技术,实现了陶瓷基板上/下表面垂直互联,可实现电子器件三维封装与集成,降低器件体积,如图14(b) 所示;(3)采用电镀生长控制线路层厚度(一般为 10μm~100μm),并通过研磨降低线路层表面粗糙度,满足高温、大电流器件封装需求;(4)低温制备工艺 (300°C 以下)避免了高温对基片材料和金属线路层的不利影响,同时也降低了生产成本。综上所述,DPC基板具有图形精度高,可垂直互连等特性,是一种真正的陶瓷电路板。
图 14 (a) DPC 陶瓷基板产品及其 (b)截面图
但是,DPC 基板也存在一些不足:(1) 金属线路层采用电镀工艺制备,环境污染严重;(2)电镀生长速度低,线路层厚度有限(一般控制在10μm~100μm),难以满足大电流功率器件封装需求。目前DPC陶瓷基板主要应用于大功率LED封装,生产厂家主要集中在我国台湾地区,但从2015年开始大陆地区已开始实现量产。
金属线路层与陶瓷基片的结合强度是影响DPC陶瓷基板可靠性的关键。由于金属与陶瓷间热膨 胀系数差较大,为降低界面应力,需要在铜层与陶瓷间增加过渡层,从而提高界面结合强度。由于过渡层与陶瓷间的结合力主要以扩散附着及化学键为主,因此常选择Ti、Cr和Ni等活性较高、扩 散性好的金属作为过渡层(同时作为电镀种子层)。
Lim等人采用50W的Ar等离子束对Al2O3基片清洗10min,随后再溅射1μm±0.2μm的铜薄膜,二者粘结强度高于34MPa,而未进行等离子 清洗的基片与铜薄膜的粘结强度仅为7MPa。占玙娟在溅射Ti/Ni(其厚度分别为200nm与400nm) 薄膜之前,采用600eV、700mA的低能离子束对AlN陶瓷基片清洗15min,所得到的金属薄膜与 陶瓷基片的粘结强度大于30MPa。可以看出,对陶瓷基片进行等离子清洗可大大提高与金属薄膜间 的结合强度,这主要是因为:(1) 离子束去除了陶瓷基片表面的污染物;(2)陶瓷基片因受到离子束 的轰击而产生悬挂键,与金属原子结合更紧密。
电镀填孔也是DPC陶瓷基板制备的关键技术。目前DPC基板电镀填孔大多采用脉冲电源,其 技术优势包括:(1) 易于填充通孔,降低孔内镀层缺陷;(2) 表面镀层结构致密,厚度均匀;(3)可采用较高电流密度进行电镀,提高沉积效率。陈珍等人采用脉冲电源在1.5ASD电流密度下电镀2h,实现了深宽比为6.25的陶瓷通孔无缺陷电镀。但脉冲电镀成本高,因此近年来新型直流电镀又重新得到重视,通过优化电镀液配方(包括整平剂、抑制剂等),实现盲孔或通孔高效填充。如林金堵等人通过优化电镀添加剂、搅拌强度及方式和电流参数,实现了通孔与盲孔电镀。
激光活化金属陶瓷基板 (LAM)
LAM基板制备利用特定波长的激光束选择性加热活化陶瓷基片表面,随后通过电镀/化学镀完成线路层制备,工艺流程如图 15(a) 所示。其技术优势包括:(1)无需采用光刻、显影、刻蚀等微加工工艺,通过激光直写制备线路层,且线宽由激光光斑决定,精度高 (可低至10 μm~20 μm),如图15(b) 所示;(2)可在三维结构陶瓷表面制备线路层,突破了传统 平面陶瓷基板金属化的限制,如图15(c) 所示;(3)金属层与陶瓷基片结合强度高,线路层表面平整,粗糙度在纳米级别。从上可以看出,虽然 LAM技术可在平面陶瓷基板或立体陶瓷结构上加工线路层,但其线路层由激光束“画”出来,难以大批量生产,导致价格极高,目前主要应用在航空航天领域异型陶瓷散热件加工。
图15 (a)LAM基板工艺流程;(b)LAM基板加工示意图;(c)LAM基板产品
表2对不同工艺制备的平面陶瓷基板性能进行了对比。
表2 平面陶瓷基板性能对比
2.2 三维陶瓷基板制备技术
许多微电子器件 (如加速度计、陀螺仪、深紫外LED 等)芯片对空气、湿气、灰尘等非常敏感。如LED芯片理论上可工作10万小时以上,但水汽侵蚀会大大缩短其寿命(甚至降低至几千小时)。为了提高这些微电子器件性能(特别是可靠性),必须将其芯片封装在真空或保护气体中,实现气密 封装 (芯片置于密闭腔体中,与外界氧气、湿气、灰尘等隔绝)。因此,必须首先制备含腔体(围坝) 结构的三维基板,满足封装应用需求。
目前,常见的三维陶瓷基板主要有:高/低温共烧陶瓷基板(High/LowTemperature Co-fired Ceramic Substrate,HTCC/LTCC)、多层烧结三维陶瓷基板(Multilayer Sintering Ceramic Substrate,MSC)、直接粘接三维陶瓷基板 (Direct Adhere Ceramic Substrate,DAC)、多层镀铜三维陶瓷基板(Multilayer Plated Ceramic Substrate,MPC)以及直接成型三维陶瓷基板(Direct Molding Ceramic Substrate,DMC)等。
高/低温共烧陶瓷基板(HTCC/LTCC)
HTCC 基板制备过程中先将陶瓷粉 (Al2O3 或 AlN)加入 有机黏结剂,混合均匀后成为膏状陶瓷浆料,接着利用刮刀将陶瓷浆料刮成片状,再通过干燥工艺使片状浆料形成生胚;然后根据线路层设计钻导通孔,采用丝网印刷金属浆料进行布线和填孔,最后将各生胚层叠加,置于高温炉(1600°C)中烧结而成,如图16所示。由于HTCC基板制备工艺温 度高,因此导电金属选择受限,只能采用熔点高但导电性较差的金属(如W、Mo及Mn等),制作 成本较高。此外,受到丝网印刷工艺限制,HTCC基板线路精度较差,难以满足高精度封装需求。但 HTCC 基板具有较高机械强度和热导率 [20 W/(m·K) ~ 200W/(m·K)],物化性能稳定,适合大功 率及高温环境下器件封装,如图17 (a) 所示。Cheah 等人将HTCC工艺应用于微型蒸汽推进器,制备的微型加热器比硅基推进器效率更高,能耗降低21%以上。
图 16 (a) HTCC 陶瓷基板制备工艺流程和 (b)结构示意图
图17 (a)HTCC陶瓷基板产品和(b)LTCC陶瓷基板产品
为了降低HTCC制备工艺温度,同时提高线路层导电性,业界开发了LTCC基板。与HTCC制 备工艺类似,只是 LTCC制备在陶瓷浆料中加入了一定量玻璃粉来降低烧结温度,同时使用导电性 良好的Cu、Ag和Au等制备金属浆料,如图17(b)所示。LTCC基板制备温度低,但生产效率高, 可适应高温、高湿及大电流应用要求,在军工及航天电子器件中得到广泛应用。
Yuan 等人选用CaO-BaO-Al2O3-B2O3-SiO2/AlN体系原料,当AlN组分含量为40%时,研制的LTCC基板热导率 为5.9W/(m·K),介电常数为6.3,介电损耗为4.9×10-3,弯曲强度高达178MPa。Qing等人采用 Li2O-Al2O3-SiO2/Al2O3体系原料,制备的LTCC基板抗弯强度为155MPa,介电损耗为2.49×10-3。
虽然LTCC 基板具有上述优势,但由于在陶瓷浆料中添加了玻璃粉,导致基板热导率偏低[一般仅为3W/(m·K)~7W/(m·K)]。此外,与HTCC一样,由于LTCC基板采用丝网印刷技术制作金属线路,有可能因张网问题造成对位误差,导致金属线路层精度低;而且多层陶瓷生胚叠压烧结时还存在收缩比例差异问题,影响成品率,一定程度上制约了LTCC基板技术发展。Yan等人经过表面处理将LTCC基板翘曲由150μm~250μm降低至80μm~110 μm;Sim等人通过改进LTCC 基板封装形式,去掉芯片与金属基底间绝缘层,模拟和实验结果显示其热阻降低为7.3W/(m·K),满足大功率LED封装需求。
多层烧结三维陶瓷基板(MSC)
与HTCC/LTCC基板一次成型制备三维陶瓷基板不同,台湾阳升公司采用多次烧结法制备了MSC 基板。其工艺流程如图18 所示,首先制备厚膜印刷陶瓷基板(TPC),随后通过多次丝网印刷将陶瓷浆料印刷于平面 TPC基板上,形成腔体结构,再经高温烧结而成,得到的MSC基板样品如图19所示。
图18 MSC陶瓷基板制备工艺流程
图19 MSC三维陶瓷基板产品
由于陶瓷浆料烧结温度一般在800°C左右,因此要求 下部的TPC基板线路层必须能耐受如此高温,防止在烧结过程中出现脱层或氧化等缺陷。由上文可知,TPC 基板线路层由金属浆料高温烧结 (一般温度为850°C ~ 900°C)制备,具有较好的耐高温性 能,适合后续采用烧结法制备陶瓷腔体。
MSC基板技术生产设备和工艺简单,平面基板与腔体结构 独立烧结成型,且由于腔体结构与平面基板均为无机陶瓷材料,热膨胀系数匹配,制备过程中不会出现脱层、翘曲等现象。其缺点在于,下部 TPC基板线路层与上部腔体结构均采用丝网印刷布线,图形精度较低;同时,因受丝网印刷工艺限制,所制备的MSC基板腔体厚度(深度)有限。因此MSC三维基板仅适用于体积较小、精度要求不高的电子器件封装。
直接粘接三维陶瓷基板 (DAC)
上述HTCC、LTCC及MSC 基板线路层都采用丝网印刷制备,精度较低,难以满足高精度、高集成度封装要求,因此业界提出在高精度DPC陶瓷基板上成型腔体制备三维陶瓷基板。由于DPC基板金属线路层在高温(超过300°C)下会出现氧化、起泡甚至脱层等现象,因此基于DPC技术的三维陶瓷基板制备必须在低温下进行。
台湾瑷司柏公司(ICP)提出采用胶粘法制备三维陶瓷基板,样品如图20所示。首先加工金属环和DPC陶瓷基板,然后采用有机粘胶将金属环与DPC基板对准后粘接、加热固化,如图21所示。由于胶液流动性好,因此涂胶工艺简单,成本低,易于实现批量生产,且所有制备工艺均在低温下进行,不会对DPC基板线路层造成损伤。但是,由于有机粘胶耐热性差,固化体与金属、陶瓷间热膨胀系数差较大,且为非气密性材料,目前DAC陶瓷基板主要应用于线路精度要求较高,但对耐热性、气密性、可靠性等要求较低的电子器件封装。
图20 有机胶接法制备DAC陶瓷基板产品
图21 DAC三维陶瓷基板制备工艺流程
为了解决上述不足,业界进一步提出采用无机胶替代有机胶的粘接技术方案,大大提高了DAC三维陶瓷基板的耐热性和可靠性。其技术关键是选用无机胶,要求其能在低温(低于 200°C)下固化;固化体耐热性好(能长期耐受300°C高温),与金属、陶瓷材料粘接性好(剪切强度大于10MPa),同时与金属环 (围坝) 和陶瓷基片材料热膨胀系数匹配 (降低界面热应力)。美国科锐公司(Cree)XRE 系列产品封装基板既采用了该技术方案,如图22。
图 22 无机胶粘结制备 DAC 三维陶瓷基板:(a) 产品图;(b)结构图
多层电镀三维陶瓷基板 (MPC)
为了发挥 DPC 陶瓷基板技术优势(高图形精度、垂直互连等), 吴朝晖等人提出采用多次/层电镀增厚技术,在DPC陶瓷基板上直接制备具有厚铜围坝结构的三维陶瓷基板,如图23(a)所示。其制备工艺与DPC基板类似,只是在完成平面DPC基板线路层加 工后,再通过多次光刻、显影和图形电镀完成围坝制备(厚度一般为500μm~700μm),如图24所示。需要指出的是,由于干膜厚度有限(一般为50μm~80μm),需要反复进行光刻、显影、图形电 镀等工艺;同时为了提高生产效率,需要在电镀增厚围坝时提高电流密度,导致镀层表面粗糙,需要不断进行研磨,保持镀层表面平整与光滑。
图 23 多层电镀三维陶瓷基板 MPC:(a)产品;(b)结构示意图
图24 多层电镀三维陶瓷基板(MPC)工艺流程图
MPC 基板采用图形电镀工艺制备线路层,避免了HTCC/LTCC与TPC基板线路粗糙问题,满足高精度封装要求。陶瓷基板与金属围坝一体化成型为密封腔体,结构紧凑,无中间粘结层,气密性高。
MPC基板整体为全无机材料,具有良好的耐热性,抗腐蚀、抗辐射等。金属围坝结构形状可以任意设计,围坝顶部可制备出定位台阶,便于放置玻璃透镜或盖板,目前已成功应用于深紫外LED封装和VCSEL激光器封装,已部分取代LTCC基板。其缺点在于:由于干膜厚度限制,制备过程需要反复进行光刻、显影、图形电镀与表面研磨,耗时长(厚度为600 μm围坝需要电镀10h以上),生产成本高;此外,由于电镀围坝铜层较厚,内部应力大,MPC基板容易翘曲变形,影响后续的芯片封装质量与效率。
直接成型三维陶瓷基板(DMC)
为了提高三维陶瓷基板生产效率,同时保证基板线路精度与可 靠性,陈明祥等人提出制备含免烧陶瓷围坝的三维陶瓷基板,其样品如图25所示。为了制备具有高结合强度、高耐热性的陶瓷围坝,实验采用碱激发铝硅酸盐浆料(alkali-activated aluminosilicate cement paste, ACP)作为围坝结构材料。围坝由偏高岭土在碱性溶液中脱水缩合而成,具有低温固化、耐热性好(可长期耐受500°C高温)、与金属/陶瓷粘接强度高、抗腐蚀,物化性能稳定等优点,满足电子封装应用需求。
图25 采用免烧陶瓷浆料制备的DMC三维陶瓷基板样品及其结构示意图
DMC基板制备工艺流程如图26所示,首先制备平面DPC陶瓷基板,同时制备带孔橡胶模具;将橡胶模具与DPC陶瓷基板对准合模后,向模具腔内填充牺牲模材料;待牺牲模材料固化后,取下橡胶模具,牺牲模粘接于DPC陶瓷基板上,并精确复制橡胶模具孔结构特征,作为铝硅酸盐浆料成型模具;随后将铝硅酸盐浆料涂覆于DPC陶瓷基板上并刮平,加热固化,最后将牺牲模材料腐蚀,得到含铝硅酸盐免烧陶瓷围坝的三维陶瓷基板。
图26 浆料直接成型法制备三维基板流程
铝硅酸盐浆料固化温度低,对DPC陶瓷基板线路层影响极小,并与DPC基板制备工艺兼容。橡胶具有易加工、易脱模以及价格低廉等特点,能精确复制围坝结构(腔体)形状与尺寸,保证围坝加工精度。实验结果表明,腔体深度、直径加工误差均小于30μm,说明该工艺制备的三维陶瓷基板精度高,重复性好,适合量产。铝硅酸盐浆料加热后脱水缩合,主要产物为无机聚合物,其耐热性好,热膨胀系数与陶瓷基片匹配,具有良好的热稳定性;固化体与陶瓷、金属粘接强度高,制备的三维陶瓷基板可靠性高。围坝厚度(腔体高度)取决于模具厚度,理论上不受限制,可满足不同结构和尺寸的电子器件封装要求。
表3比较了上述不同三维陶瓷基板性能的一些基本性能。与表2重复或类似的数据不再列入。
表3三维陶瓷基板性能对比
03
陶瓷基板性能与检测
目前,陶瓷基板性能检测尚无国家或行业标准。其主要性能包括基板外观、力学性能、热学性 能、电学性能、封装性能 (工作性能)和可靠性等。
外观检测:陶瓷基板外观检测一般采用肉眼或显微镜,检测基板表面是否有裂缝、孔洞,金属 层表面是否有气泡、脱层、划痕或污渍等质量缺陷。此外,陶瓷基板尺寸、基板平整度(翘曲)、金属线路层厚度与表面粗糙度、线宽与间距等都是需要重点检测的内容。
力学性能:平面陶瓷基板力学性能主要指金属线路层结合强度,表示金属层与陶瓷基片间的粘 接强度,直接决定了后续器件封装质量(固晶强度与可靠性等)。不同方法制备的陶瓷基板结合强度 差别较大,通常采用高温工艺制备的平面陶瓷基板(如TPC、DBC等),其金属层与陶瓷基片间通过 化学键连接,结合强度较高;而低温工艺制备的陶瓷基板 (如 DPC基板),金属层与陶瓷基片间主要 以范德华力及机械咬合力为主,结合强度偏低。
常用结合强度测试方法包括:
(1) 胶带法:将3M 胶带紧贴金属层表面,用橡皮滚筒在上面滚压,以去除粘接面内气泡。10s后用垂直于金属层的拉力使胶带剥离,检测金属层是否从基片上剥离,属于一种定性测试方法。
(2) 焊线法:选用直径为0.5 mm或1.0mm的金属线,通过焊料熔化直接焊接在基板金属层上, 随后用拉力计沿垂直方向测量金属线抗拉力。
(3) 剥离强度法:将陶瓷基板表面金属层蚀刻(划切) 成 5 mm ´ 10 mm长条,然后在剥离强度 测试机上沿垂直方向撕下,测试其剥离强度。要求剥离速度为50mm/min,测量频率为10次/s。
对于三维陶瓷基板而言,力学性能还包括围坝与平面陶瓷基板间的结合强度,不同方法制备的三维陶瓷基板围坝结合强度差别很大。由于HTCC/LTCC、MSC基板采用高温烧结工艺制备,围坝与基板界面以化学键为主,结合强度较高;而以粘接、电镀、浆料固化技术成型的围坝,其结合强度相对较低。常用测试方法包括剪切强度测试和拉伸强度测试,测试构型如图27所示。
图 27 (a) 剪切强度测试示意图;(b)拉伸强度测试示意图
热学性能:陶瓷基板热学性能主要包括热导率、耐热性、热膨胀系数和热阻等。陶瓷基板在器 件封装中主要起散热作用,因此其热导率是重要的技术指标;耐热性主要测试陶瓷基板在高温下是否翘曲、变形,表面金属线路层是否氧化变色、起泡或脱层,内部通孔是否失效等。由于陶瓷基板一般为多层结构,其导热特性不仅与陶瓷基片材料热导率有关 (体热阻),还与材料界面结合情况密 切相关(界面接触热阻)。因此,采用热阻测试仪(可测量多层结构的体热阻和界面热阻)能有效评价陶瓷基板导热性能。
电学性能:陶瓷基板电学性能主要指基板正反面金属层是否导通(内部通孔质量是否良好)。由 于DPC 陶瓷基板通孔直径较小,在电镀填孔时会出现未填实、气孔等缺陷,一般可采用X射线测试 仪 (定性,快速) 和飞针测试机 (定量,便宜)评价陶瓷基板通孔质量。
封装性能:陶瓷基板封装性能主要指可焊性与气密性(限三维陶瓷基板)。
可焊性是指芯片或金属引线能否顺利与基板金属层焊接(键合) 在一起,同时具有一定键合强度。为提高陶瓷基板可焊性,一般需在基板金属层进行表面处理(如化学镀银,化学镀Ni/Au、Ni/Pd/Au等),可防止金属层氧化,同时提高金属层可焊性。表面处理层成分与厚度对可焊性影响较大,通常可采用引线键合机和剪切强度测试仪进行评估。
将芯片贴装于三维陶瓷基板腔体内,用盖板 (金属或玻璃) 将腔体密封便可实现器件气密封装。围坝材料与焊接材料气密性直接决定了器件封装气密性,不同方法制备的三维陶瓷基板气密性存在一定差异。对三维陶瓷基板主要测试围坝材料与结构的气密性,主要有氟油气泡法和氦质谱仪法。
可靠性测试与分析
可靠性主要测试陶瓷基板在特定环境下 (高温、低温、高湿、辐射、腐蚀、高频振动等)的性能 变化,主要内容包括耐热性、高温存储、高低温循环、热冲击、耐腐蚀、抗腐蚀、高频振动等。对于失效样品,可采用扫描电镜 (SEM) 和 X 射线衍射仪 (XRD)分别进行微观和成分分析;采用扫 描声显微镜 (SAM) 和 X射线检测仪进行焊接界面和缺陷分析。
04
陶瓷基板应用
随着功率器件技术的不断发展,特别是随着第三代半导体技术的兴起,陶瓷基板因其良好的导热、耐热、高强度与高可靠性等,应用领域与需求量不断扩展。下面简要介绍陶瓷基板在不同电子封装领域的应用。
4.1 电力电子器件封装
自上世纪50年代以来,电力电子器件从晶闸管过渡到GTR/GTO/MOSFET,再逐渐发展到绝缘 栅双极晶体管 (Insulate-Gate Bipolar Transistor, IGBT)。与前两代相比,第三代电力电子器件(如 IGBT)具有频率高、功率大和开关速度快等优势,在国防军事、航天航空、电动牵引、轨道交通、新能源汽车以及家用电子器件领域得到广泛应用。由于 IGBT输出功率高,发热量大,散热不良将损坏 IGBT 芯片,因此对于 IGBT封装而言,散热是其技术关键,必须采用陶瓷基板强化散热, 如图28。目前,IGBT封装主要采用DBC陶瓷基板,原因在于DBC基板金属线路层较厚(一般为 100 μm ~ 600μm),具有载流能力大、耐高温性好及可靠性高等特点。
图28 (a)IGBT模块及(b)采用DBC基板封装IGBT模块
4.2 激光器 (LD)封装
LD是受激辐射的半导体器件,广泛应用于工业、军事、医疗和3D打印等领域,如图29(a)所示。目前国际上90μm~ 100 μm单管9××nm器件商用产品输出功率在12W~ 18 W 之间,实验室水 平可达20W ~25W。由于LD 电光转换效率约为50%~ 60%,工作时大量热量集中在有源区, 导致结温升高,引发腔面灾变性光学损伤或饱和现象,严重限制LD输出功率和使用寿命。此外,热膨胀系数不匹配导致器件内部产生热应力,输出光在快轴方向呈非线性分布,给光束准直、整形及光纤耦合带来极大挑战,是阻碍高功率激光器广泛应用的主要因素之一。
因此,在 LD封装中必 须采用导热性能良好、热膨胀系数匹配的陶瓷基板。由于AlN陶瓷具有热导率高、热膨胀系数低等 优点,因此LD封装普遍使用AlN陶瓷基板,如图29(b)所示。倪羽茜等人采用AlN和SiC两 种陶瓷制成三明治型热沉实现了大功率LD单管高功率输出,模拟分析和实验结果显示,SiC和AlN材料制备的陶瓷基板热阻分别为1.19K/W和1.30K/W,二者在15A时输出功率分别为13.1W和16.3 W,峰值电光转换效率分别为 63.9% 和68.3%。
图29 (a)蓝光LD器件及(b)采用DBC基板封装LD结构示意图
4.3 发光二极管 (LED)封装
同 LD 一样,发光二极管 (LED)也是一种基于电光转换的半导体功率器件,具有电光转换效率 高、响应快、寿命长和节能环保等优势,目前已广泛应用于通用照明、信号指示、汽车灯具和背光显示等领域。随着LED技术发展,芯片尺寸和驱动电流不断提高,LED模组功率密度也不断提高, 散热问题越来越严重。
大功率LED封装基板先后经历了三个阶段:金属支架、金属基板和陶瓷基 板。由于陶瓷基板具有高绝缘、高导热和耐热、低膨胀等特性,特别是采用垂直通孔技术的DPC陶 瓷基板,可有效满足倒装共晶、COB(板上芯片封装)、CSP(芯片尺寸封装)等技术白光LED 封装需求,如图30所示。对于紫外LED模组,采用三维陶瓷基板,可满足其高效散热与气密封装需求,如图31所示。
图30 白光LED模组及其陶瓷封装示意图
图31 紫外LED模组及其封装结构图
4.4 热电制冷器 (TEC)封装
热电制冷片(ThermoelectricCooler, TEC)是一种常用的半导体制冷器件,其工作原理为帕尔贴效应,其样品如图32(a) 所示,结构示意图如图32 (b)所示。热电制冷技术优势明显,主要表现在:(1)无运动部件,无噪声,无磨损、寿命长,易于调控,可靠性高;(2)不使用制冷剂,无泄漏,对环境无污染;(3)制冷器尺寸小,重量轻,适合小容积、小尺寸等特殊环境电子器件散热。由于热电制冷效率与半导体粒子数量呈正相关,单位面积粒子数量越多,热电制冷效率越高。DPC陶瓷基板图形精度高,可提高粒子布置密度,从而有效提高热电制冷效率。
图 32(a) 热电制冷片样品;(b)热电制冷片封装示意图
4.5 高温电子器件 (HTE)封装
航空航天、深海钻探、汽车等领域电子器件需要能够在极端环境(如高温、高湿、高压、高腐蚀、高辐射、高频振动等) 下工作,因此封装材料必须具有高耐热性和抗湿性,同时器件芯片必须密封于腔体中,避免外界环境的侵蚀和破坏。前述三维陶瓷基板(如HTCC、LTCC、MPC和DMC等) 具有高强度腔体结构,气密性良好,可满足恶劣环境下器件封装要求,如图 33所示。
图33 采用LTCC气密封装的晶振及其封装结构图
4.6 其他功率器件封装
因具有良好的导热性、耐热性和可靠性,陶瓷基板也同样应用在很多其他功率或高温器件封装 中。如聚焦光伏器件封装,由于聚焦作用导致太阳光密度增加,芯片温度升高,必须采用陶瓷基板强化散热,如图 34 所示。此外,在微波射频领域,为了降低损耗,需采用高频特性良好的HTCC 或LTCC基板来提高速度,如图35所示。
图 34 聚焦光伏模组 (CPV)及其封装示意图
图35汽车传感器及射频器件
05
陶瓷基板发展趋势分析
陶瓷基板具有高导热、高耐热、高绝缘、高强度、低热胀、耐腐蚀及抗辐射等特点,在功率器件及高温电子器件封装中得到广泛应用。随着半导体技术不断发展,功率器件也将逐渐向大功率、小型化、集成化、多功能等方向发展,对封装用陶瓷基板性能也提出了更高要求,具体表现在以下几个方面。
陶瓷基片材料多样化
氧化铝 (Al2O3)材料热导率低,热膨胀系数较高,但因其技术成熟,成 本低,综合性价比高,将在今后很长时间内占据陶瓷基板主导地位。氮化铝(AlN)材料热导率高,热膨胀系数低,但价格高,目前仅限于导热性能要求较高的功率器件(如LD)封装。氮化硅(Si3N4)材料热导率适中,热膨胀系数小,抗弯强度高(大于800MPa),是一种很有潜力的功率器件封装基 板材料,特别是在大功率、大温变、高可靠的电力电子器件 (如 IGBT)封装。
但总体而言,目前陶瓷基片价格偏高,原因在于国内陶瓷基片厂家大多依赖进口陶瓷粉料。因此今后陶瓷基片主要研究方向包括超细、超纯粉料制备,多元助烧剂 (主要为碱金属氧化物和稀土元素)组合,无害、高效、 高精度成型技术及先进烧结技术研发,从而不断降低陶瓷基片成本。
陶瓷基板高精度与小型化
为了满足器件小型化发展要求,必须不断提高陶瓷基板线路层加工精度(线宽/线距)。对于TPC、HTCC/LTCC和MSC陶瓷基板,其线路层采用丝网印刷金属浆料制备,图形精度较 低(一般大于100μm)。对于DBC和AMB陶瓷基板,其线路层通过湿法腐蚀金属铜层得到,由于 铜层较厚,其图形精度也较低(一般大于200μm)。而对于DPC、MPC和DMC陶瓷基板,其线路 层通过图形电镀生长制备,图形精度高 (一般可控制在小于 50μm,取决于线路层厚度)。因此,对 于集成度较高和小型化功率器件封装,开始逐渐采用图形精度较高的DPC陶瓷基板(如图36)。
图 36 高精度DPC 基板及其封装的小型热电制冷器(TEC) 陶瓷基板集成化
一般而言,TPC、DBC 和AMB陶瓷基板只适合制备单面线路层(或双面线路层,但上下层不导通)。如果要实现上下层导通,需要先激光打孔(孔径一般大于200μm),然后孔内填充金属浆料后烧结而成,孔内金属层导电、导热性差,基板可靠性低。HTCC/LTCC基板采用多层生胚片叠加(金属通孔对准)后烧结制备,因此可实现基板内垂直互连,提高封装集成度,但HTCC/LTCC基板电阻率大,电流通载能力低。
DPC 陶瓷基板采用激光打孔(孔径一般为60 μm ~120 μm)和电镀填孔技术制备金属通孔,由于孔内电镀填充致密铜柱,导电导热性能优良,因而可实现陶瓷基板上下线路层垂直互连。在此基础上,通过电镀增厚等技术制备围坝,可得到含围坝结构的三维陶瓷基板;如果采用焊接/粘接技术实现多片DPC基板垂直集成,则可以进一步得到多层陶瓷基板 (Multilayer Ceramic Substrate, MLC,如图37),满足功率器件三维封装和异质集成需求。
图 37 多层陶瓷基板及其封装集成 面向具体应用的陶瓷基板技术研发
一方面,随着第三代半导体 (包括 GaN、SiC、AlN 等)技 术发展,功率器件开始在半导体照明、电力电子、微波射频、5G 通信、新能源及新能源汽车等领域飞速发展,对陶瓷基板需求激增。目前由于陶瓷基板制备技术和标准缺失,国内企业主要跟踪美国、日本等技术先进国家进行研发与生产,高端产品(特别是图形精度高、电流通载能力强等)完全依赖进口;另一方面,航空航天、武器装备、深海钻探、汽车电子等领域恶劣环境(高温、超低温、大温变、高湿、强腐蚀、高辐射、高频振动等) 对封装陶瓷基板也提出了新要求(解决陶瓷基板体积 和重量大、耐热性差、可靠性差等问题)。
总体而言,陶瓷基板在功率器件封装中占据举足轻重的作用,是各国重点研发的关键电子材料。因此迫切需要加强陶瓷基板核心技术研发 (包括陶瓷粉料、基片及基板制备技术等),满足国内飞速 发展的市场需求。
06
结束语
鉴于陶瓷具有良好的导热性、耐热性、高绝缘、高强度、低热胀、耐腐蚀和抗辐射等优点,陶瓷基板在功率器件和高温电子器件封装中得到广泛应用。目前,陶瓷基片材料主要有Al2O3、AlN、Si3N4、SiC、BeO 和BN。由于Al2O3和AlN具有较好的综合性能,两者分别在低端和高端陶瓷基板市场占据主流,而Si3N4基板由于抗弯强度高,今后有望在高功率、大温变电力电子器件(如IGBT)封装领域发挥重要作用。
平面陶瓷基板主要包括薄膜陶瓷基板 (TFC)、厚膜印刷陶瓷基板(TPC)、直接键合陶瓷基板(DBC)、活性金属焊接陶瓷基板 (AMB)、直接电镀陶瓷基板 (DPC) 和激光活化金属陶瓷基板(LAM)等。其中,TFC 基板图形精度高,但金属层较薄,主要应用于小电流光电器件封装;TPC基板耐热 性好,成本低,但线路层精度差,主要应用于汽车传感器等领域;DBC和AMB基板线路层较厚, 耐热性较好,主要应用于高功率、大温变的 IGBT 封装;DPC基板具有图形精度高、可垂直互连等优点,主要应用于大功率LED 封装;而LAM基板则满足了航空航天领域异型陶瓷结构件散热需求。
为了实现器件气密封装,业界开发了多种三维陶瓷基板制备技术,主要包括高温/低温共烧陶瓷基板 (HTCC/LTCC)、多层烧结三维陶瓷基板 (MSC)、直接粘结三维陶瓷基板(DAC)、多层镀铜三 维陶瓷基板 (MPC) 和直接成型三维陶瓷基板 (DMC) 等。
其中,HTCC/LTCC、MSC基板均采用丝 网印刷与高温烧结工艺制备,腔体可靠性高,但金属线路层精度较差;MPC、DAC和DMC基板通过在DPC基板上电镀、粘接和固化成型围坝,具有金属线路层精度高,围坝与基板结合强度高等优 点,有望在今后的功率器件气密封装、三维封装与集成领域发挥重要作用。后期陶瓷基板将主要沿着高精度、小型化、集成化方向发展。
审核编辑 :李倩
-
半导体
+关注
关注
328文章
24506浏览量
202126 -
封装
+关注
关注
123文章
7278浏览量
141096 -
功率器件
+关注
关注
40文章
1529浏览量
89486
原文标题:电子封装陶瓷基板
文章出处:【微信号:中科聚智,微信公众号:中科聚智】欢迎添加关注!文章转载请注明出处。
发布评论请先 登录
相关推荐
在IGBT模块中氮化铝陶瓷基板的应用如何?
万物互联时代,智能汽车需要陶瓷基板
陶瓷封装基板——电子封装的未来导向
封装热潮带来芯片荒,陶瓷基板一片难求
先进陶瓷材料应用——氧化铝陶瓷基板
芯片荒半导体封装需求激增,斯利通陶瓷封装基板供不应求
电子封装陶瓷基板-之陶瓷基片材料
电子封装-低温共烧陶瓷基板
氮化硅与氮化铝陶瓷基板究竟有何区别?
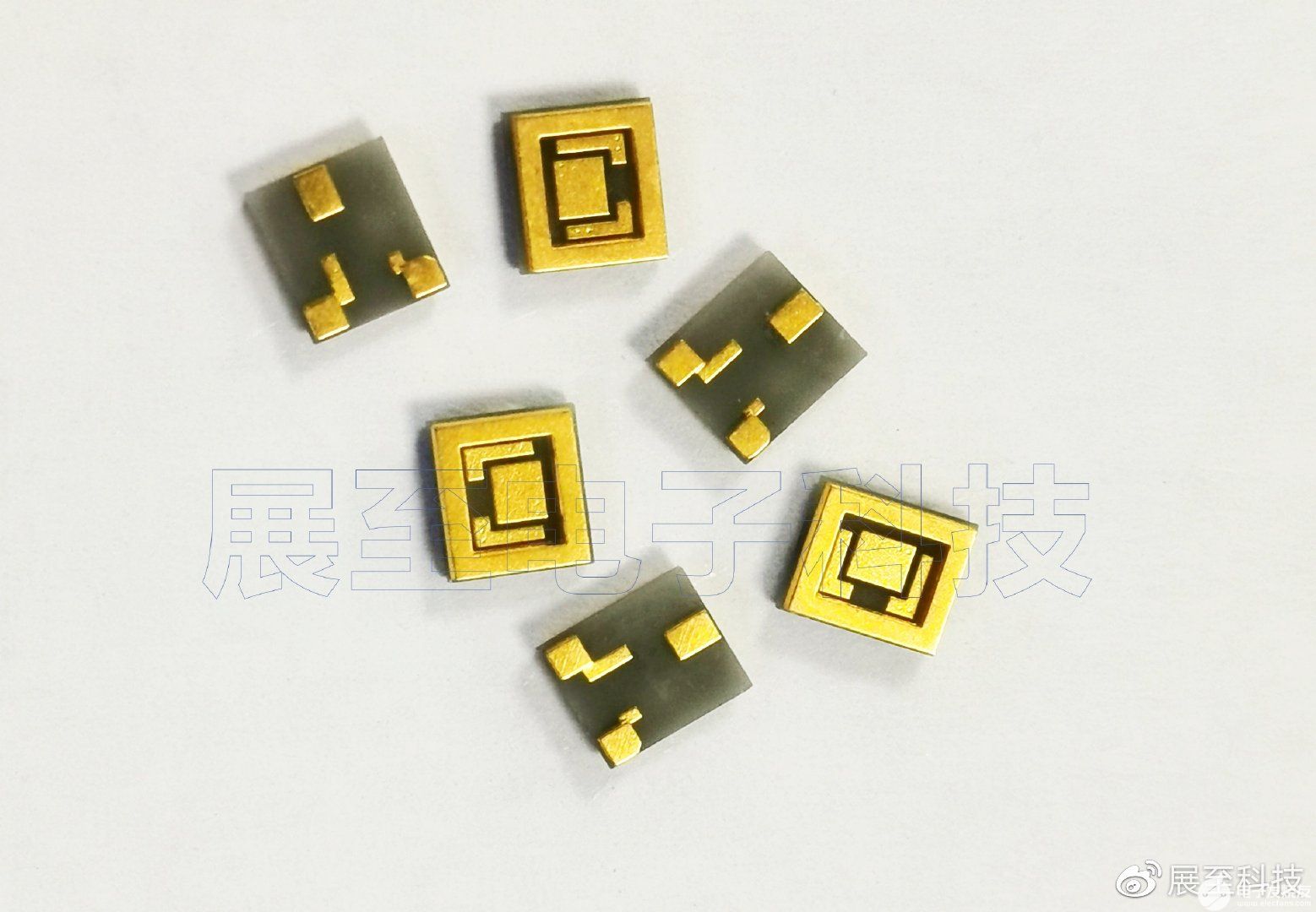
评论