一、研究的背景与问题
宽厚板作为钢铁材料中的重要品种之一,广泛应用于航天军工、能源动力、交通运输、海洋船舶等领域,是国防建设和国民经济发展的重要支撑,在整个国防和经济布局中占有举足轻重的地位。2010年以来,我国宽厚板制造过程自动化水平取得长足进步,但在关键工序质量参数感知、多工序协调、优化决策等方面存在突出短板,原有制造技术已很难适应日益苛刻高端制造产业链的品质要求。以海洋工程装备、高技术船舶、大型施工装备等为代表的高端装备制造业为例,对宽厚板产品的尺寸外形精度提出了高于现行国家标准的技术要求,宽度尺寸波动要求控制在几个毫米以内,不平度要求≤2mm/m等,外形尺寸检测仍以人工线下测量为主,多个关键参数无法在线感知。严苛的质量要求对过程精准控制水平和品质保证能力提出了极大挑战,严重制约了我国宽厚板制造技术的再发展。
新一代信息技术的快速发展正在推动着制造业向着智能化生产方式变革,而通过智能化技术推动钢铁工业发展则是中国从钢铁大国走向钢铁强国的必由之路。我国宽厚板制造行业自动化基础普遍较好,拥有工业制造领域最为丰富的应用场景,以CPS信息物理系统和数字孪生为代表的新兴技术在感知、计算、通信、控制等方面展现出得天独厚的强大优势,能够通过数字孪生体和CPS信息物理系统所具有的相互映射、实时交互、高效协同机制,实现系统内控制单元按需响应、快速迭代、动态优化的功能。可见,运用新兴智能化手段进一步精准控制水平,增强质量保证能力,推动钢铁行业技术进步并保证我国钢铁领域内科技引领具有重要意义。
通过对国内近百条中厚板生产线的工艺技术装备现状研究发现,产线普遍在关键工艺质量参数感知、多工序协调优化方面,长期面临如下突出问题:
1、生产过程中轧制、剪切等工序的自动化达到较高水平,但是各工序控制系统相对孤立,尚未形成联动,部分工序缺失关键质量参数,不能基于反馈进行动态优化控制,机理模型的预测和控制精度低,严重影响产品质量、生产效率和成材率的提升;
2、缺少钢板轮廓识别和板形检测关键大型仪表,导致轧后钢板头尾形貌、轮廓和板形等关键质量参数难以在线精准识别,仍以人工方式线下测量,无法与轧制过程形成在线反馈控制,难以通过在线工艺优化来保证最终产品质量;
3、依靠人工经验的传统组板系统订单匹配度低、精准剪切控制能力偏低,无法根据钢板实时轮廓信息优化组板策略导致组板余材过多,影响生产效率和成材率。剪切工序也无法根据实时轮廓形状优化剪切策略。此外,剪切工序与轧制过程、组坯过程除基础的产品信息交互之外,无其它过程质量数据交互,迫切需要将轧后钢板实际轮廓形状与订单合同进行实时动态匹配,急需开发面向多目标约束的优化剪切和动态组板策略,以实现减少切损的同时提高订单的匹配度。
针对宽厚板制造领域内过程精准控制科学问题和相关技术瓶颈,2010年由山钢与东北大学等单位组建联合研发团队,在国家十三五重点研发计划《基于CPS架构的多工序协调优化与质量精准控制及应用示范》(2017YFB0304103)项目和山东省《宽厚板智能轧制数字化车间是的试点示范》项目的支撑下,依托山东省山钢王国栋院士工作站科研平台,深入推进开展产学研合作和协同创新,发挥高校基础研究理论创新优势与企业产工程技术优势,联合开展本项目关键共性技术的科研攻关工作。
研发团队聚焦“组板-轧制-剪切”关键工序,第一次在行业内明确了多工序协调优化机制及其所需要解决的科学问题。应用所研制的轮廓和板形检测仪器装置实现了热轧工序关键质量数据感知能力大幅提升。集中解决了CPS信息物理系统构建、“数据+机理”模型双驱动外观尺寸控制模型、多工序协调优化决策等多项长期难以突破的技术难题,成功构建了宽厚板制作过程多工序间高效协同的原创性技术理论体系。所开发的宽厚板轮廓板形CPS智能制造技术应用实现了产线关键工艺质量数据高质量贯通,轧钢过程中的精准控制能力明显增强,宽厚板产线多工序协调优化控制水平得到大幅度提升。
二、解决问题的思路与技术方案
本项目创新应用机器视觉、数字孪生和信息物理CPS等先进技术,将宽厚板生产过程中的工艺参数映射到数字空间中,融合机理模型+数据模型建立包括动态在线设定、轮廓板形感知反馈的宽厚板双闭环优化CPS信息物理系统,如图1所示。内环系统通过机理模型和机器学习满足过程控制的实时高精度设定(浅色箭头),外环系统通过机器视觉技术感知宽厚板三维形貌,并建立数字孪生体反馈优化模型参数(深色箭头),实现控制模型参数动态优化。这样就可以在虚拟数字空间优化工艺参数和工序间的协调关系,把实测三维形貌数据传输到数字空间对应的数字孪生体,通过相应的算法模型计算获得优化策略,并通过指令反馈到物理空间中相关工序执行相关操作,实现宽厚板制造过程参数动态实时优化。
图1 技术路线图
三、主要创新性成果
本项目针对行业领域内所面临的共性技术难题,聚焦轮廓和板形在线检测技术和仪器装置、轮廓及板形动态CPS系统、多工序协调优化控制等涉及宽厚板制造过程精准控制的技术瓶颈,通过理论与实践相结合,实现了数字孪生和CPS信息物理系统理论、大型在线检测仪器装置、多工序协调控制、工程化创新应用的一体化创新,并取得了很好的应用实施效果。主要创新成果如下:
1、率先研制出基于机器视觉的宽厚板轮廓和板形在线检测技术以及两大仪器装置,在具有代表性的4300mm级宽厚板产线进行首次稳定化工程应用。
针对热轧宽厚板产线现场存在大量冷却水导致的水汽、辊道上方照明不均并存在反光、钢板表面随机分布除鳞残渣和粉尘、钢板运动过程中震动打滑等恶劣工况,基于人眼双目视觉理论提出了多阵列相机组图像采集机制,研究出高斯噪声、椒盐噪声、脉冲噪声等多类型混杂噪声高效滤除算法,开发了包涵自适应图像分割、激光条纹图像特征、自适应ROI、翘曲特征提取等算法库和模型库,探索并建立了七大类上千个品种规格宽厚板产品的冷/热态尺寸映射模型体系,实现了冷/热态大尺寸不规则运动钢板的轮廓和板形在线高精度检测。所研制的检测装置在宽度方向检测精度达到±2mm、长度方向检测误差小于5‰、侧弯量检测精度达到±5mm,头尾不规则变形区检测精度达到±5mm,板形平直度检测精度达到±1mm。动态钢板轮廓和板形在线检测仪器装置的成功开发,实现了轧制后1000℃~室温工艺区间内的钢板三维信息在线感知,完全取代了人工估计和线下测量的传统生产方式,在大型检测仪器装置研制方面填补了国际空白。同时,也为依据工艺规则并融合数据反馈开展钢板外形尺寸智能化控制提供了数据支撑。
2、基于板形在线检测信息构建了多源数据与多模型联合解析的板形动态数字孪生模型体系,探索并开发出具有板形在线识别、精准计算、闭环控制和动态优化等特征的板形CPS系统,为轧制过程平面形状精准控制提供了全新的智能化技术支撑。
图3 本项目采用的平面形状数字孪生体模型构建方法
基于钢坯轧制过程板形成因机理解析,以钢坯轧制过程中平面形状的过程控制参数动态优化为核心,开发出钢坯精轧成型过程中的带载辊缝形状、辊系弹性变形、轧件长度预测、平面形状可控点、形变区域微跟踪等多个机理预测模型体系,并进行了工业化应用,轧制过程平面形状精准可控能力大幅度提高。为进一步提高智能化控制能力,依托现有控制系统中的工艺实绩、模型设定、来料尺寸和成分等多源信息建立数据模型,并在几何建模、“数据+机理”模型融合的基础上探索构建出板形数字孪生体,如图3所示。在引入利用本项目研制的板仪装置检测的板形数据的基础上,开发出具有板形信息动态反馈、设定精准计算、轧制过程闭环控制和模型动态优化等特征的板形CPS系统,一举突破了轧钢过程中传统的板形控制滞后的工艺瓶颈,形成了板形精准控制智能化新工艺技术。
3、开发出数字孪生驱动的可控点平面形状智能预测技术,创新提出面向多目标约束的剪切优化策略和基于视觉反馈的动态组板策略,成功构建出宽厚板多工序协调优化的轮廓CPS系统,实现了“组板-轧制-剪切”三个关键工序间的协调优化。
依托轮廓数据反馈和平面形状预测模型,开发出基于工艺约束的智能化子板排布策略和基于多背包问题的母板组板模型,实现了连铸出钢材、余材板坯、余材钢板的科学动态组板,最大程度降低了组板损耗。根据钢板宽度、长度、侧弯、板形以及头尾部不规则区域尺寸等轮廓信息在线检测,结合当前合同订单信息在线计算钢板剪切策略,确定最佳剪切线位置,实现智能化剪切。在此基础上,进一步探索了七大类上千个品种规格宽厚板产品在1000℃~室温间的外形尺寸映射模型体系,破解了钢板冷却过程中外形参数无法测量这一“黑箱”过程。围绕轮廓检测数据、组板计划数据、轧制过程平面形状预测高质量融合,在“组板-轧制-剪切”三个关键工序间探索出以钢板二维平面轮廓和板形控制为核心的多工序协调优化轮廓CPS系统,实现了钢板组板科学、钢板外形尺寸控制精准的智能化技术体系。
四、应用情况与效果
应用本项目所研制的检测仪器装置实现了钢板轮廓和板形在线高精度检测,取代了人工线下测量的生产方式,产线关键工序的质量信息感知能力得到明显提升。以轮廓和板形控制为核心,应用所开发的CPS智能制造系统实现了宽厚板组板、轧制以及剪切几个关键工序间的动态闭环协调优化控制。此外,本项目的成功应用还将数字孪生和CPS信息物理系统等新兴技术由概念普及推向至创新应用的新阶段,在宽厚板生产流程的智能制造“无人区”起到示范引领作用。图4为依托本项目所开发的4300mm宽厚板轮廓及板形CPS系统。
本项目所开发的基于机器视觉的宽厚板多工序协调优化CPS系统于2017年在莱钢4300mm宽厚板生产线进行应用,实现了多工序协调优化CPS系统在“组板-轧制-剪切”等主线工序的融合创新,有效提升了工序间的协同效率,产线整体智能化水平得到了明显提升。同时,有效降低了作业人员劳动强度,使产线综合成材率、生产效率、工序成本等得到明显改善。其中,实现了动态调整组板策略,提高余材组板成功率50%;产线生产效率由147吨/小时提高到172吨/小时,提高25吨/小时;产线成材率由项目实施前91.21%提高91.65%,提高0.44%;带出品率由1.38%降低到0.31%,降低1.07%,吨钢电耗由105.37kW/t降低至91.11kW/t,降低14.26kW/t;单支钢板剪切时间由原1.43min降低至1.2min,剪切线生产效率提高13.3%。项目整体成果应用三年以来,创造直接经济效益达2.3亿元。
图44300mm宽厚板轮廓及板形CPS系统
依托本项目所开发的相关技术在我国三钢、唐钢等中厚板等产线进行应用,提高了板形和平面形状控制精度,创造了良好的经济社会效益。
在技术指标先进性方面,本项目涉及的检测仪器装置以及宽厚板轮廓和板形CPS系统均为行业首次研制和首次应用。与传统工艺相比,本项目所研制装置的检测精度明显优于国外相关技术。
审核编辑 :李倩
-
算法
+关注
关注
23文章
4455浏览量
90750 -
机器视觉
+关注
关注
161文章
4043浏览量
118354 -
智能制造
+关注
关注
48文章
5111浏览量
75552
原文标题:基于机器视觉的宽厚板轮廓及板形CPS智能制造技术研发与应用
文章出处:【微信号:vision263com,微信公众号:新机器视觉】欢迎添加关注!文章转载请注明出处。
发布评论请先 登录
相关推荐
中车轧机中压主传动系统在宽厚板领域实现“零”的突破
钢铁企业4300轧机牌坊磨损,24小时快速在线修复完成
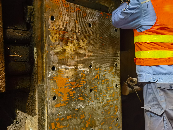
评论